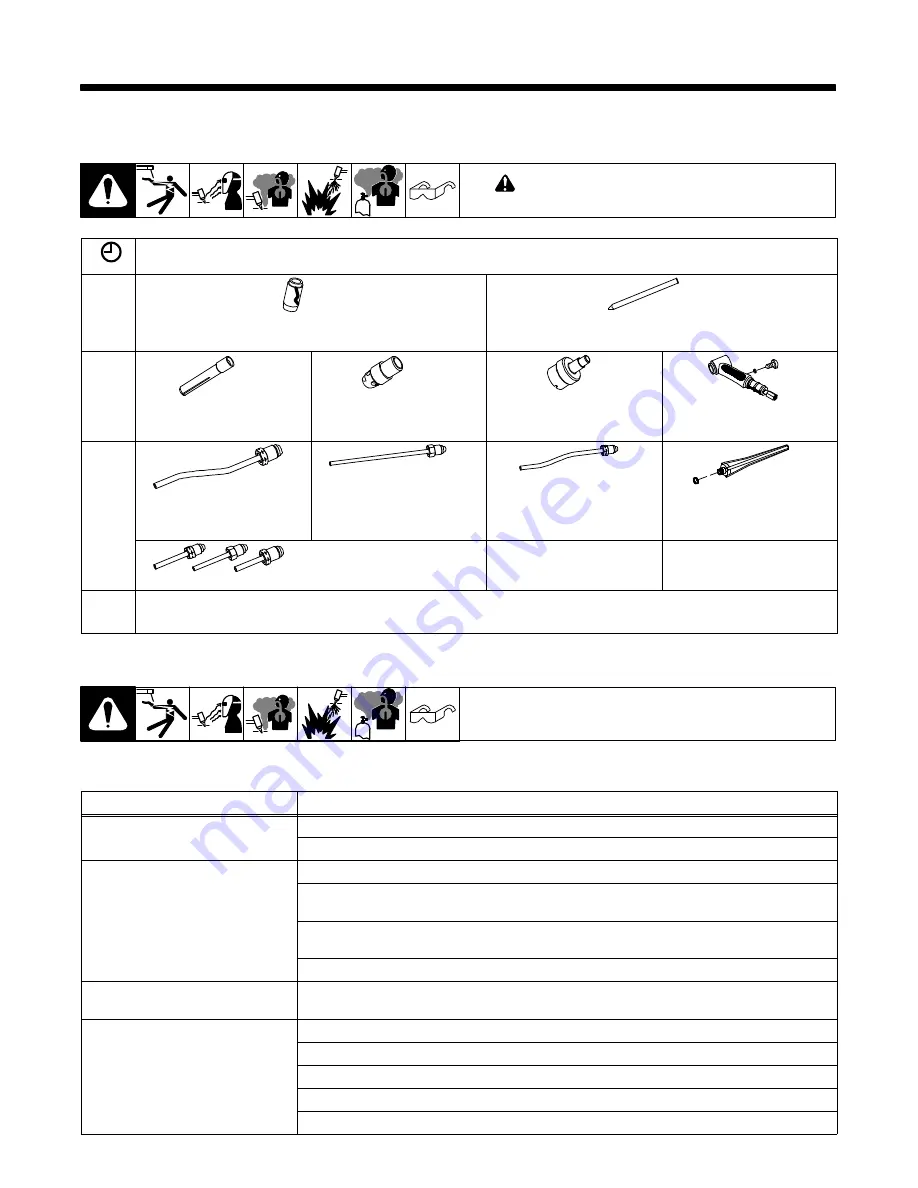
OM-225 427 Page 8
SECTION 4
−
MAINTENANCE & TROUBLESHOOTING
4-1. Routine Maintenance
!
Disconnect torch before maintaining.
= Check
= Change
= Clean
= Replace
* To be done by Factory Authorized Service Agent
Daily
Nozzle For Cracks
−
If Necessary
Check Tungsten Preparation (See Section 5)
Weekly
Collet For Wear
−
If Necessary
Collet Body Threads
−
If Necessary
Gas Lens Screen
−
If Necessary
Gas Valve, If Applicable
−
If Necessary
Monthly
Power Cable For Cracks,
Wear
−
If Necessary
Gas Hose For
Cracks, Leaks, Wear
−
If Necessary
Water Hose, If Applic-
able, For Cracks, Leaks,
Wear
−
If Necessary
*
Back Cap O-Ring
−
If Necessary
Power, Gas, And Water
Cable Connections To En-
sure They Are Tight
Cable Cover For
Tears, Holes, Or Wear
−
If Necessary
When using a water-cooled torch, maintain cooling equipment according to the manufactures recommendations.
*
4-2. Troubleshooting
Before using troubleshooting table, check selection and preparation of tungsten electrode according to Section 5.
Trouble
Remedy
Arc will not start. High frequency present
and visible at the torch.
Check cable and work connections. Be sure weld circuit is complete (see Section 3-3).
Check and be sure shielding gas is present.
Lack of high frequency; difficulty in es-
tablishing arc.
Select proper size and type of tungsten. Properly prepare tungsten according to Section 5.
Check cables and torch for cracks or bad connections. Be sure that torch cables are not close to any
grounded metal. Repair or replace necessary parts.
Check torch consumables. Be sure collet and collet body are correctly installed and tightened (see Sec-
tion 3-1).
Check welding power source High Frequency control, and if necessary, check and adjust spark gaps.
Torch gas valve not working properly (if
applicable).
Have Factory Authorized Service Station/Service Distributor check valve.
No shielding gas flow from torch.
Be sure valves on gas supply are open.
Check cable for kinks or blockage.
Check and tighten all gas supply fittings.
Check cables and torch for cracked insulation or bad connections. Repair or replace (see Section 4-1).
Make sure collet is installed correctly (see Section 3-1).
Summary of Contents for WP-17
Page 2: ......
Page 4: ......
Page 17: ...ENGLISH OM 225 427 Page 13 Notes...
Page 22: ...ENGLISH Notes...
Page 23: ...ENGLISH Notes...