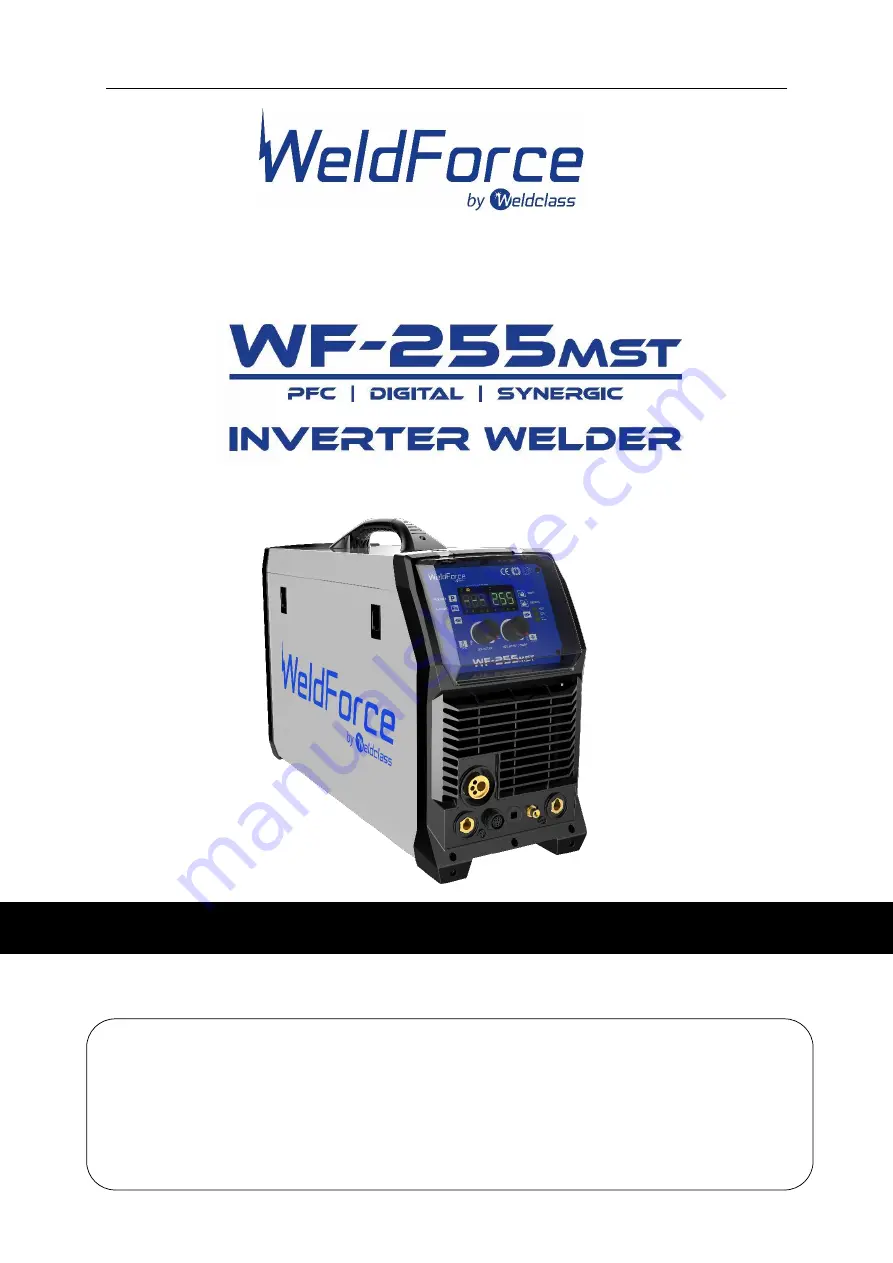
WF-255
MST
© Weldclass 2019 | E.&O.E. | Edition 2.2
1
Edition 2.2
OPERATING INSTRUCTIONS
IMPORTANT!
To qualify for full 36 month warranty, you must register within 30 days of purchase. See inside for details.
Read these Operating Instructions Completely before attempting to use this machine. Save this manual and
keep it handy for quick reference. Pay particular attention to the safety instructions we have provided for
your protection. Contact your distributor if you do not fully understand anything in this manual.
Summary of Contents for WeldForce WF-255MST
Page 7: ...WF 255MST Weldclass 2019 E O E Edition 2 2 7 16 4 Warranty Conditions 79...
Page 39: ...WF 255MST Weldclass 2019 E O E Edition 2 2 39 Figure 25...
Page 40: ...40 Weldclass 2019 E O E Edition 2 2 8 6 Primary Schematic Circuit Diagram Figure 26...
Page 45: ...WF 255MST Weldclass 2019 E O E Edition 2 2 45 Figure 33 Figure 34 Figure 35 Figure 36...
Page 80: ...80 Weldclass 2019 E O E Edition 2 2 www Weldclass com au WF 255MST...