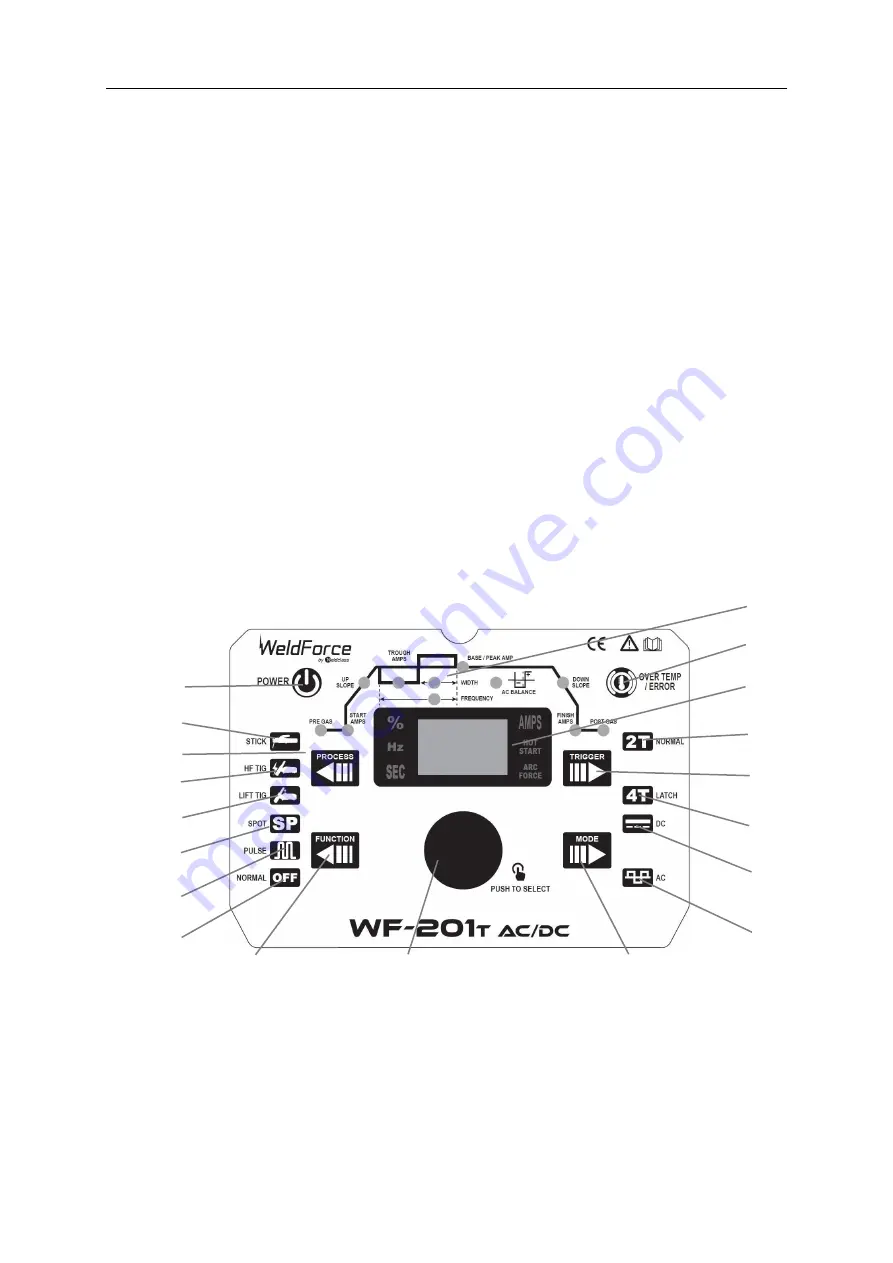
WF-201
T AC/DC
© Weldclass 2019 | E.&O.E.
9
3.3
Control Panel
10.
Power On Indicator Light (POWER)
11.
Stick (MMA) Process Indicator Light (STICK)
12.
Process Selection Button (PROCESS)
13.
High Frequency Start TIG Process Indicator Light (HF TIG)
14.
Lift Arc Start TIG Process Indicator Light (LIFT TIG)
15.
Spot Weld Function Indicator Light (SPOT)
16.
Pulse Arc Function Indicator Light (PULSE)
17.
Normal Arc Function Indicator Light (NORMAL/OFF)
18.
Function Selection Button (FUNCTION)
19.
Selection Knob
20.
Mode Selection Button (MODE)
21.
AC Arc Output Mode Indicator Light (AC)
22.
DC Arc Output Mode Indicator Light (DC)
23.
Latch Trigger Mode Indicator Light (4T)
24.
Trigger Mode Selection Button
25.
Normal Trigger Mode Indicator Light (2T)
26.
LCD Readout
27.
Error/Over Temperature Indicator Light
28.
Arc Parameter Chart
Figure 3