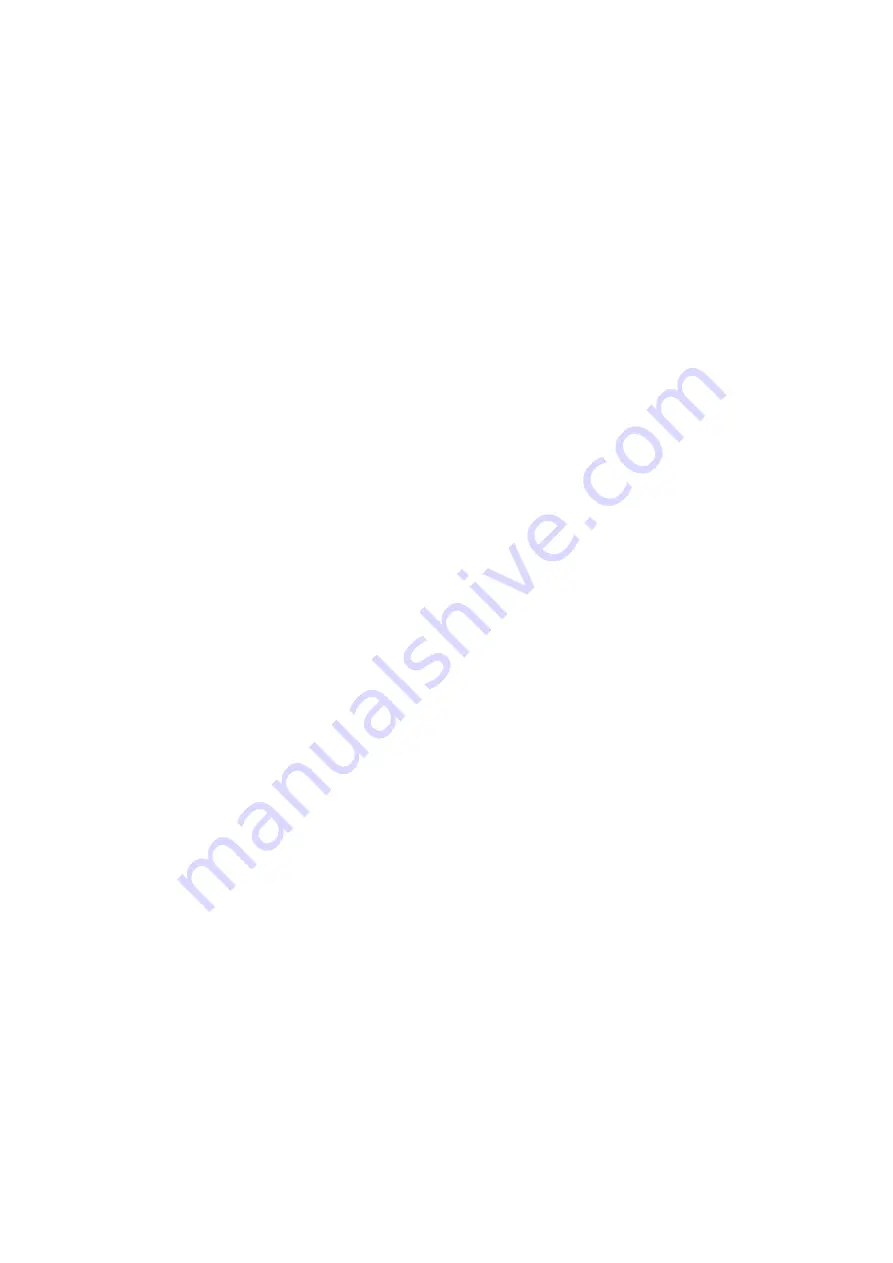
11.8
Establishing the Arc and Making Weld Beads
Before attempting to weld on a finished piece of work, it is recommended that practice welds be made on
a sample metal of the same material as that of the finished piece. The easiest welding procedure for the
beginner to experiment with MIG welding is the flat position. The equipment is capable of flat, vertical and
overhead positions. For practicing MIG welding, secure some pieces of 1.6mm or 2.0mm mild steel plate
(150 x 155Mm). Use 0.9mm flux cored gasless wire or a solid wire with shielding gas.
11.9
MIG Output Settings
Manual MIG welding setting requires some practice by the operator, as the machine has two control
settings that have to balance. These are the Wire Speed control and the welding Voltage control.
Voltage is essentially the power in the welding arc that sets the heat. The wire speed feed simply controls
the rate at which the welding wire is fed into the weld pool. For any voltage position setting, there will be
a specific corresponding ‘sweet spot’ in the wire feeding speed that will give the smoothest and most stable
welding arc. The correct wire feeding speed for a given voltage setting is affected by welding wire type and
size, shielding gas, welding material and joint type.
Synergic function makes the setup of MIG welding much simpler as follows:
1.
Select output setting (the machine calculates the optimal voltage and wire speed ratio)
2.
Adjust inductance setting to refine arc characteristics
3.
Obviously other variables such as welding joint type, position and thickness, air temperature can
affect the optimal voltage and wire feed setting, so voltage can be adjusted to fine-tune for
optimal performance.
11.9.1
Changing to a different welding wire
When changing to a different welding wire diameter, different control settings are required. A thinner
welding wire needs more Current (Wire Speed) to achieve the same current level. A satisfactory weld
cannot be obtained if the Current (Wire Speed) and Voltage settings are not adjusted to suit the welding
wire diameter and the dimensions of the work piece.
11.10
Welding wire Size Selection
The choice of Welding wire size and shielding gas used depends on the following:
1.
Thickness of the metal to be welded
2.
Type of joint
3.
Capacity of the wire feed unit and power source
4.
The amount of penetration required
5.
The deposition rate required
6.
The bead profile desired
7.
The position of welding
8.
Cost of the wire
9.
Environment (can shielding gas be used or not?)