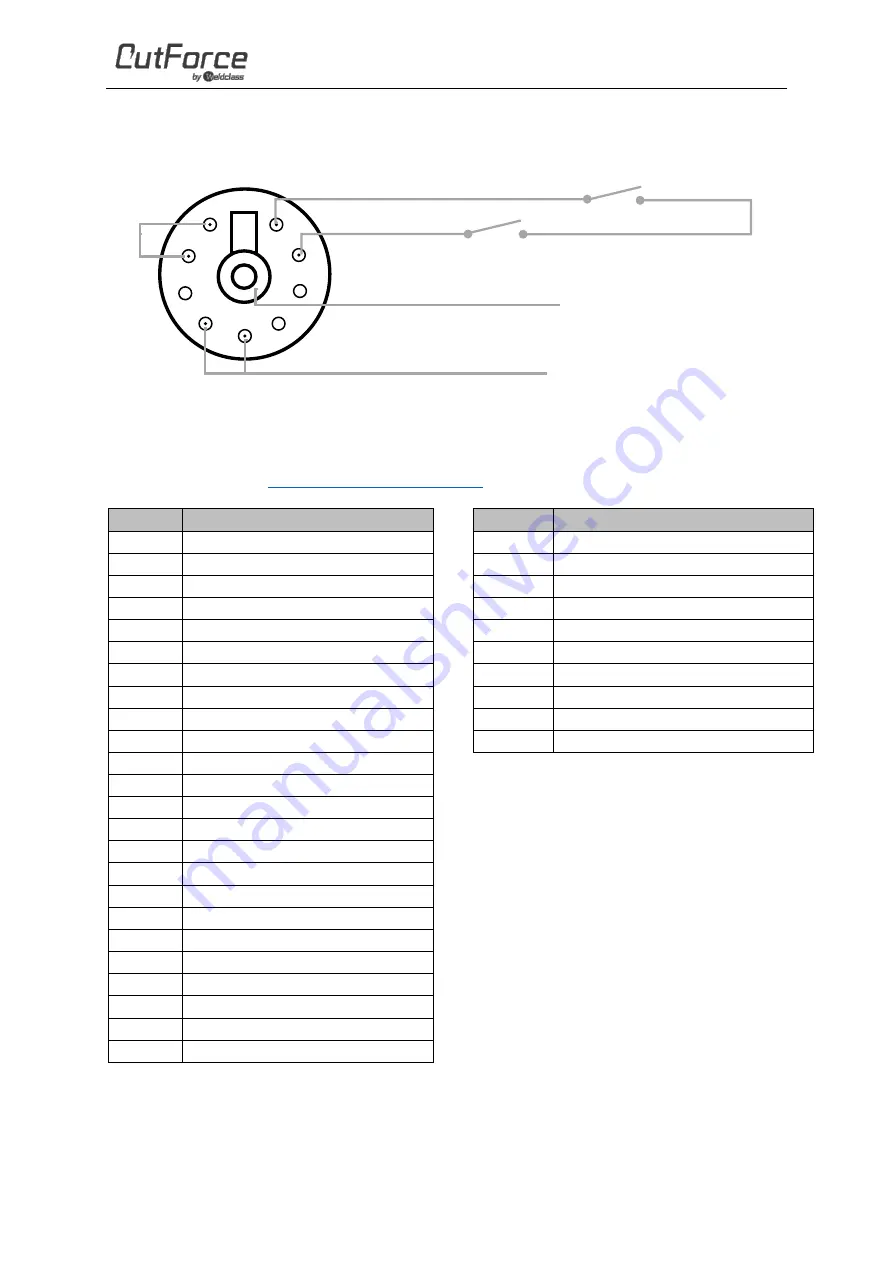
.
20
© Weldclass 2019 | E.&O.E. | Edition 1.0 2019.05
8.3
Plasma Torch Pin Configuration
8.4
Machine Spare Parts
or contact your Weldclass distributor.
Ref.
Description & Part No
1
Front Plastic Panel WC-06335
2
Torch Socket WC-06336
3
Dinse Earth Socket WC-06310
4
Included in 5
5
Control Panel & PCB Assy WC-06339
6
Control Panel Cover
7
Included in 5
8
Included in 5
Not shown
Control PCB (secondary) WC-06330
9
Cover Panel WC-06331
10
Handle
11
Rear Panel
12
Air Regulator/Filter WC-06333
13
On/Off Switch
14
Cable Clamp
15
Fan Grill
16
Fan WC-06264
17
Air Solenoid Valve WC-06332
18
Inductor
19
Solenoid valve bracket
20
Heat Sink
21
Heat Sink
22
Heat Sink
23
IGBT
Table 6
Ref.
Description & Part No
24
Support Pillar
25
Heat Sink
26
Heat Sink
27
Main Transformer WC-06334
28
Insulation
29
Fast Recovery Diode
30
Bridge Rectifier
31
Thermistor
32
Fast Recovery Diode
33
Main PCB WC-06340
Table 7
1
2
6
5
4
3
8
9
7
Trigger
Cap Safety Switch
Pilot Arc
Cutting Current
Summary of Contents for CF-06176
Page 21: ...CF 45P Weldclass 2019 E O E Edition 1 0 2019 05 21 Figure 17...
Page 22: ...22 Weldclass 2019 E O E Edition 1 0 2019 05 8 5 Primary Schematic Circuit Diagram Figure 18...
Page 37: ...CF 45P Weldclass 2019 E O E Edition 1 0 2019 05 37 NOTES...
Page 38: ...38 Weldclass 2019 E O E Edition 1 0 2019 05...
Page 39: ...CF 45P Weldclass 2019 E O E Edition 1 0 2019 05 39...
Page 40: ...40 Weldclass 2019 E O E Edition 1 0 2019 05 www Weldclass com au CF 45P...