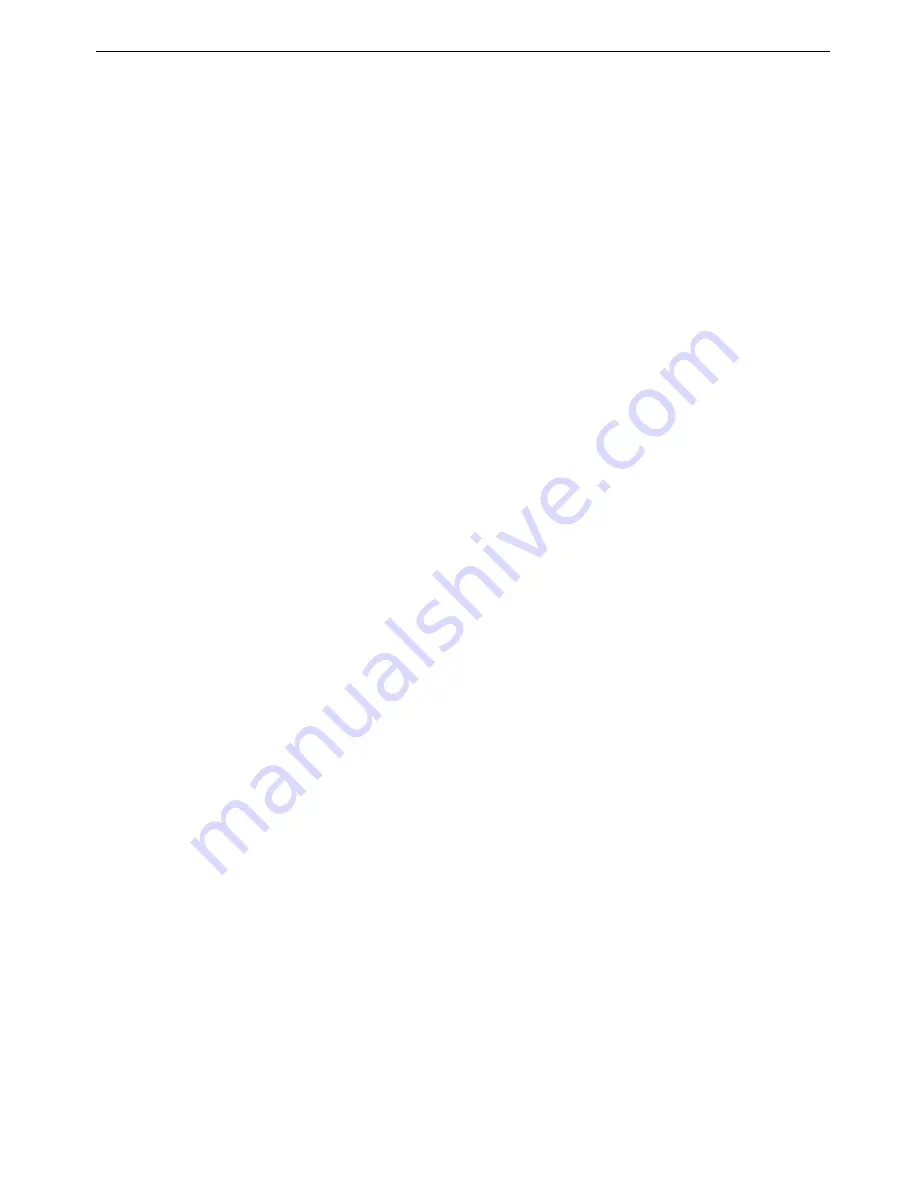
-
21
-
precautions such as filtering of the public supply system. Consideration should be given to shielding
the supply cable of permanently installed arc welding equipment, in metallic conduit or equivalent.
Shielding should be electrically continuous its length. The shielding should be connected to the
welding power source so that good electrical contact is maintained between the conduit and the
welding power source enclosure.
2) Maintenance of the arc welding equipment
The arc welding equipment should be routinely maintained according to the manufacturer’s
recommendations. All access and service doors and covers should be closed and properly fastened
when the arc welding equipment is in operation. The arc welding equipment should not be modified in
any way, except for those changes and adjustments covered in the manufacturer’s instructions. In
particular, the spark gaps of arc striking and stabilizing devices should be adjusted and maintained
according to the manufacturer’s recommendations.
3) Welding cables
The welding cables should be kept as short as possible and should be positioned close together,
running at or close to the floor level.
4) Equipotent bonding
Bonding of all metallic components in the welding installation and adjacent to it should be considered.
However, metallic components bonded to the word piece will increase the risk that the operator could
receive an electric shock by touching these metallic components and the electrode at the same time.
The operator should be insulated from all such bonded metallic components.
5) Earthling of the work piece
Where the work piece is nor bonded to earth for electrical safety, nor connected to earth because of its
size and position, for example ships hull or building steelwork, a connection bonding the work piece
to earth may reduce emissions in some, but not all instances. Care should be taken to prevent the
earthling of the work piece increasing the risk of injury to users, or damage to other electrical
equipment. Where necessary, the connection of the work piece to earth should be made by a direct
connection to the work piece, but in some countries where direct connection is not permitted, the
bonding should be achieved by suitable capacitance, selected according to national regulations.
6) Screening and shielding
Selective screening and shielding of other cables and equipment in the surrounding area may alleviate
problems of interference. Screening of the entire welding installation may be considered for special
applications.