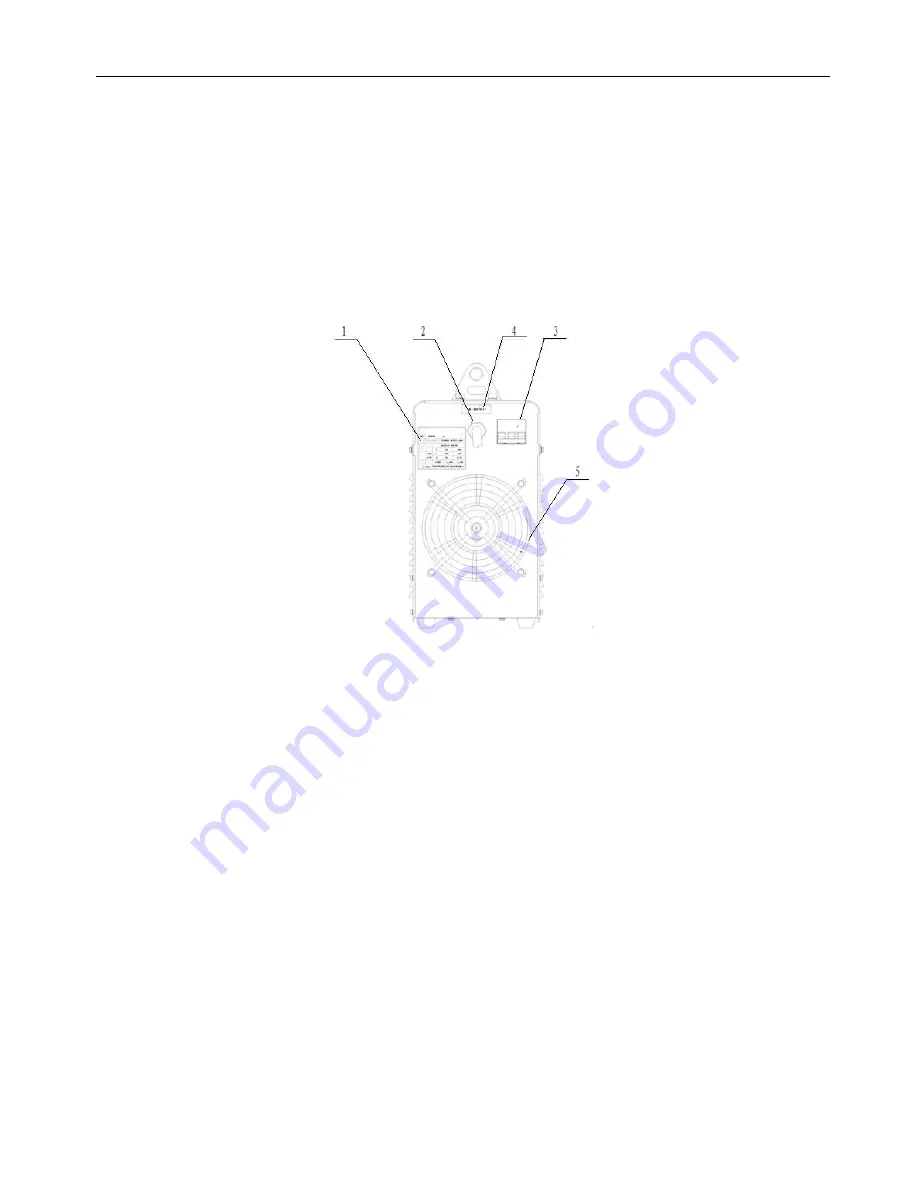
ARC-E 400
12
(6) Welding current regulation knob
Used to adjust welding current on panel
(7) Welding cable (+) quick socket
Connect to electrode holder.
(8) Welding cable (-) quick socket
Connect to workpiece.
1.2 The rear panel and parts number reference
Figure 6: Rear panel
(1)
Specification plate
(2)
Input power cable
It is 4-pin cable. The mixed-colored wire must be firmly grounded, the rest wires connect to
corresponding 3-phase power supply.
(3)
Circuit breaker
The function of circuit breaker is to protect welding machine by automatic trip to turn-off power
supply while in machine overload or failure. Normally, the switch flipped to upward means
power-on. Use switch on the switch box to start or stop welding machine. Don’t use this air switch
as power switch.
(4)
Input warning mark
(5)
Cooling fan