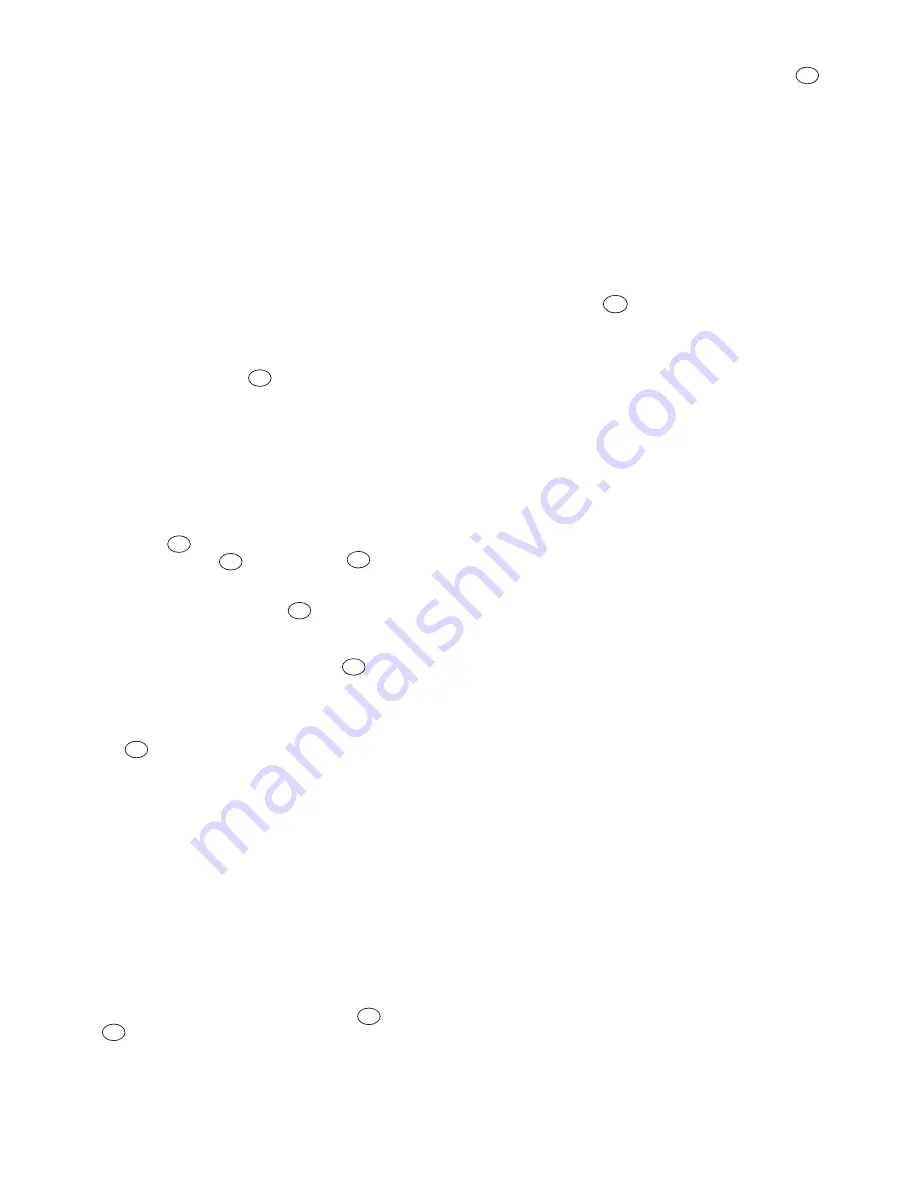
VIII. Setting and Adjusting
Pressure:
The unloading valve is direct acting. The pressure set on
the nitrogen regulator is directly related to the relief
pressure. The higher the nitrogen pressure, the higher the
relief set point. Clean dry air at a minimum of 1,200 psi
(6,000 psi max) may also be used.
Use the following procedure to obtain the correct set point.
A few attempts at working pressure may be required to
confirm the set point (Chart 1).
CAUTION:
Bleed off all air from the fluid system. Trapped air
will become energized and may cause injury to
personnel when the valve relieves.
1. Screw the pressure regulator 8 adjustment screw all the
way out (Counter Clockwise, Fig 4).
CAUTION:
When the handle hits its stop, the top of the
regulator may start to unscrew. Do not unscrew
the regulator top any further. Failure to comply
may cause injury to personnel when pressure is
applied to the valve.
2. Open the valve 20 on the nitrogen bottle or from the air
source. The inlet gauge 6 on the regulator 8 should
indicate the pressure in the nitrogen bottle.
3. Tighten the backpressure regulator 9 adjustment screw
fully (Clockwise).
predicted gas pressure does not produce the desired set
pressure, you may have to adjust the regulator 8 up or
down.
Some of the factors affecting performance include
ambient and liquid temperature, and gas media used (air
vs nitrogen).
9. Reset the nitrogen pressure to the new setpoint and
repeat items 3, 4, 5 of this section. Test the line again
until the valve relieves.
NOTE:
Once the relief valve is adjusted to the correct set
point it is normal for the gas pressure to rise as
fluid in the line 19 approaches the set pressure.
The backpressure regulator will vent gas to
compensate this increase in gas pressure. It is also
normal for the valve to release (unload) liquid at a
lower fluid pressure than when it first opened. The
set pressure should, however, return to the setpoint
fairly rapidly once the liquid pressure has decayed.
CAUTION:
Never block the valve discharge line. It will cause
valve damage.
7
4. Turn the adjustment screw on the regulator 8 until the
gas line pressure reaches a nominal set point. Use the
Chart 1 to find gas pressure versus "set" pressure.
5. Turn the adjustment screw on the backpressure
regulator 9 counter clockwise until the gas starts to
exhaust (gas begins to make a sound). Then slightly turn
the adjustment screw clockwise until the backpressure
regulator just stops exhausting gas.
NOTE:
Always set the pressure in the Rising Direction. If
you pass a set point drop the pressure to about 50
psi below the set point then re-approach the set
point.
6. Test the working pressure by slowly raising the line
(liquid) pressure until the valve begins to relieve. The
treating line pressure should stabilize and stop rising once
this happens.
7. Reduce the line pressure until the cylinder rod 4 and
wear 14 sleeve are fully seated.
8. The relationship between gas pressure and line (liquid)
pressure is defined by Chart 1. These values are from
actual tests using water as the liquid. However, values in
this chart should be considered preliminary and if the
Line Set
Pressure PSI
1000
1500
2000
2500
3000
3500
4000
4500
5000
5500
6000
6500
7000
7500
8000
8500
9000
9500
10000
10500
11000
11500
12000
12500
13000
13500
14000
14500
15000
Required Nitrogen
(or gas) PSI
37
55
73
91
109
127
145
163
181
199
217
235
253
271
288
306
324
342
360
378
396
414
432
450
468
486
504
522
540
Chart. 1