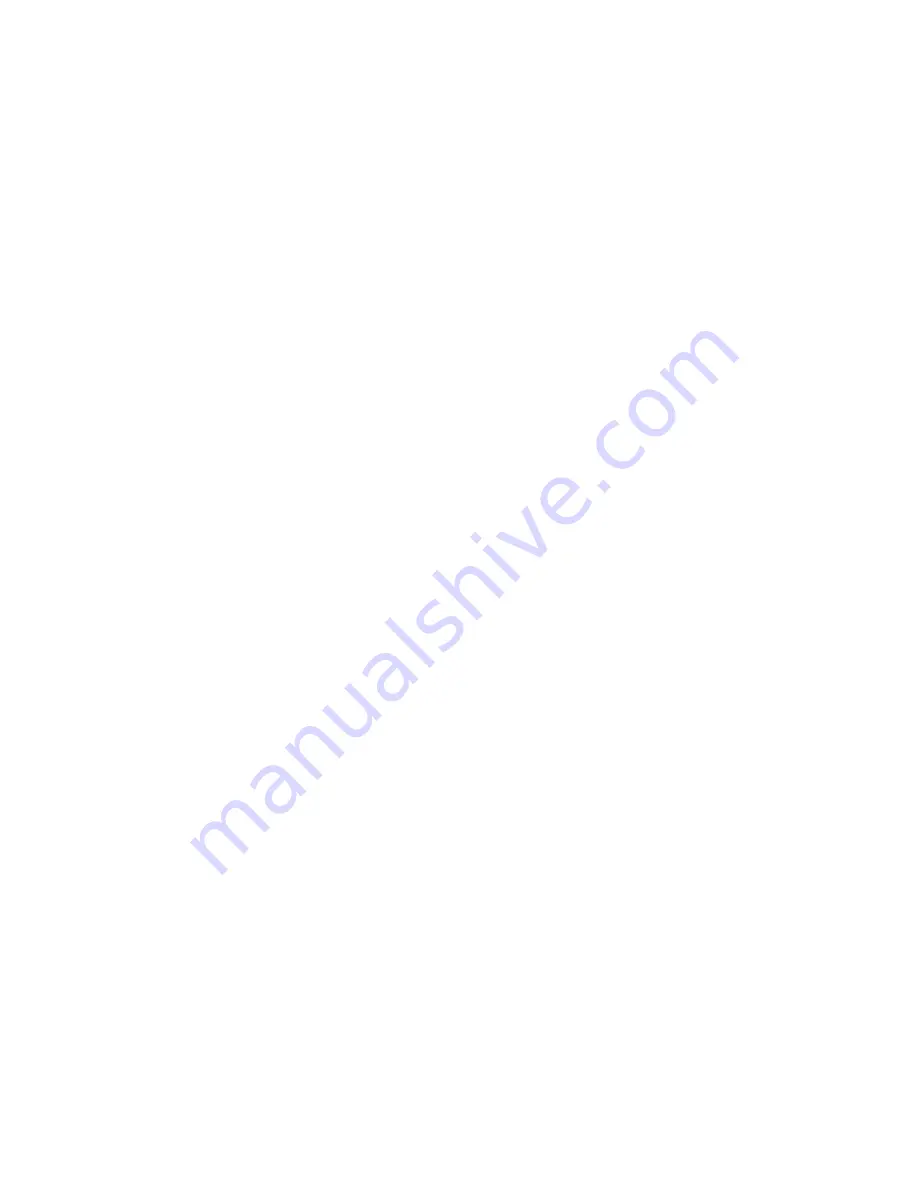
Hopkinsons Fig 9052
VALVE ACTUATOR
Section 1
1.1 GENERAL
The actuator consists of a motor driving an output shaft through an all spur gear train
incorporating a torque indicating mechanism and an automatic mechanical device for changing
the drive from manual to power. The actuator includes a valve travel limit switch unit and a
torque switch unit with combined torque indicator and is of totally enclosed weatherproof
construction, suitable for mounting at any angle or inverted.
1.2 MOTOR AND GEAR TRAIN
A. C. 3 phase motors are of squirrel cage design fitted with 'packed for life' grease lubricated
ball bearings. Dimensions and performance are in accordance with B.S. 2048, B.S. 2960,
B.S. 2613 or B.S.170, whichever is applicable. Class "B" insulation is provided as standard and
the machines are 1/2 hour rated. The windings are terminated on 2 B. A. stainless steel stud
type terminals in an integral terminal box.
The motor is mounted on the top cover of the gear box, and the reduction gear shafts and final
output shaft bearings are located in the main housing and spider plate. The final drive assembly
incorporates a lost motion, or hammer blow device which allows the motor to run up to speed
before transmitting full torque to the valve.
1.3 TORQUE LIMITING DEVICE
The final reduction stage in the actuator drive consists of a single helical spur pinion shaft which is
capable of axial movement against a spring. Upon a predetermined torque being exceeded the
end thrust component causes axial movement of the helical pinion shaft. This movement is
transmitted to the indicator and switches of the torque switch assembly by means of a roller
mounted on the torque switch lever and positioned between flanges on the helical pinion shaft.
The final reduction gear is axially located on the actuator output shaft and the face width of the
helical pinion shaft is sufficient to allow axial movement while remaining in mesh with the gear.
The spring cylinder assembly which is anchored to the spider plate, normally keeps the pinion shaft
in a mid position.
The design of the spring cylinder assembly is such that a limited deflection of the compression
spring is permitted allowing axial movement of the helical pinion shaft in either direction
corresponding to 50% to 110% output torque of the actuator in the opening or closing directions.
3
Weir Power & Industrial - First choice for power and industrial protection