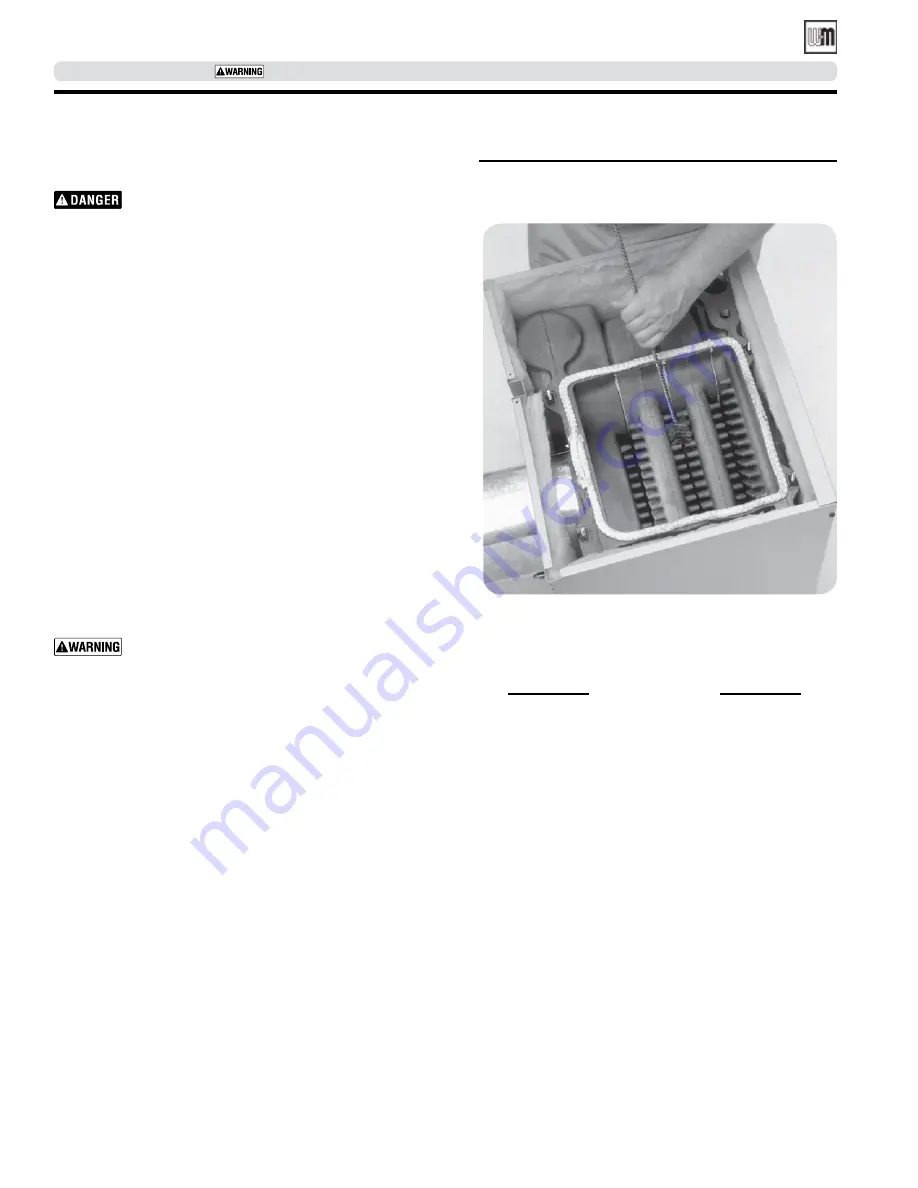
SERVICE TECHNICIAN ONLY — read and follow completely.
Detailed service procedures
Cleaning boiler flue ways
Make sure all electrical connections to boiler are turned
off and wait until boiler is warm, not hot, before clean-
ing. Failure to do so will result in severe personal injury,
death or substantial property damage.
1. Top flue boilers
-remove breeching and jacket top panel.
Rear flue boilers
- remove jacket top panel.
2. Remove flue collector hood, saving hardware for reassembly.
3. Shut off oil valves. Arrange drip pans under the areas of oil piping
that will be disconnected. Disconnect oil line at burner so that
you can swing open the door completely.
4. Line combustion chamber floor with newspaper to catch any
soot that will be loosened in the cleaning process.
5. Starting at the top of the boiler, use a wire flue brush to thor-
oughly clean between all pins at all angles. Be careful not to
damage side walls of rear refractory.
6. Move to the bottom of the flue ways and clean up between the
sections to reach pins left uncleaned in step #5.
7. Once the flue ways are cleaned, carefully remove the paper from
the floor of the combustion chamber.
8. Verify sealing rope around flue area is intact. Visually check condition
and position of insulation in combustion chamber floor, and the re-
fractories at the rear of boiler and in the burner mounting door. Replace
any parts as necessary.
9. Close burner mounting door and tighten nut securely. Place
flue collector hood on top of boiler. Secure with hardware from
step #2.
Maintain a gas-tight seal to avoid possible flue gas
leakage and carbon monoxide emissions, which can
lead to severe personal injury or death.
10. Check breeching for sooting and clean if necessary. Install jacket
top panel and breeching.
11. Reconnect oil line and all electrical connections.
General description of control operation
Automatic air vent
Air is released when cap is unscrewed one turn. If air vent leaks, re-
move small cap on top of vent, push in stem of valve and then release
to clean valve seat. Screw cap completely on, then unscrew one turn.
Temperature limit control
If high boiler water temperature occurs, control shuts down burner, but
allows circulator to run as long as there is a call for heat. Limit should
be set higher than temperature needed for the system.
Maximum limit setting is 220°F.
2007 Energy Act Compliance
In accordance with
Section 303 of the 2007 Energy Act
, this
boiler is equipped with a feature that saves energy by reducing
the boiler water temperature as the heating load decreases. This
feature is equipped with an override which is provided primarily
to permit the use of an external energy management system that
serves the same function.
Figure 24
Thoroughly clean flue ways between all
pins at all angles Start on top of boiler,
finish from the bottom
Water relief valve
Provides discharge if boiler pressure exceeds 30 psig.
Circulator
Circulator provides forced water circulation through boiler
and piping system.
Pressure-temperature gauge
Provides reading of boiler pressure and temperature. Maxi-
mum boiler pressure is 50 psig, maximum water temperature
is 220°F. Temperature will vary according to system and daily
heating demands. The range will be from room temperature
up to limit control setting.
The limit control supplied with the boiler must be set-
up with thermal prepurge or thermal targeting active
unless exempted below:
IMPORTANT
THIS OVERRIDE MUST NOT BE USED UNLESS AT
LEAST ONE OF THE FOLLOWING CONDITIONS IS TRUE:
•
An external energy management system is installed that reduces
the boiler water temperature as the heating load decreases.
•
This boiler is not used for any space heating.
•
This boiler is part of a modular or multiple boiler system having
a total input of 300,000 BTU/hr or greater.
•
This boiler is equipped with a tankless coil (not applicable to
WGO boilers).
Part number 550-142-331/0421
30
WGO
OIL-FIRED NATURAL DRAFT WATER BOILER — SERIES 4—
Boiler Manual