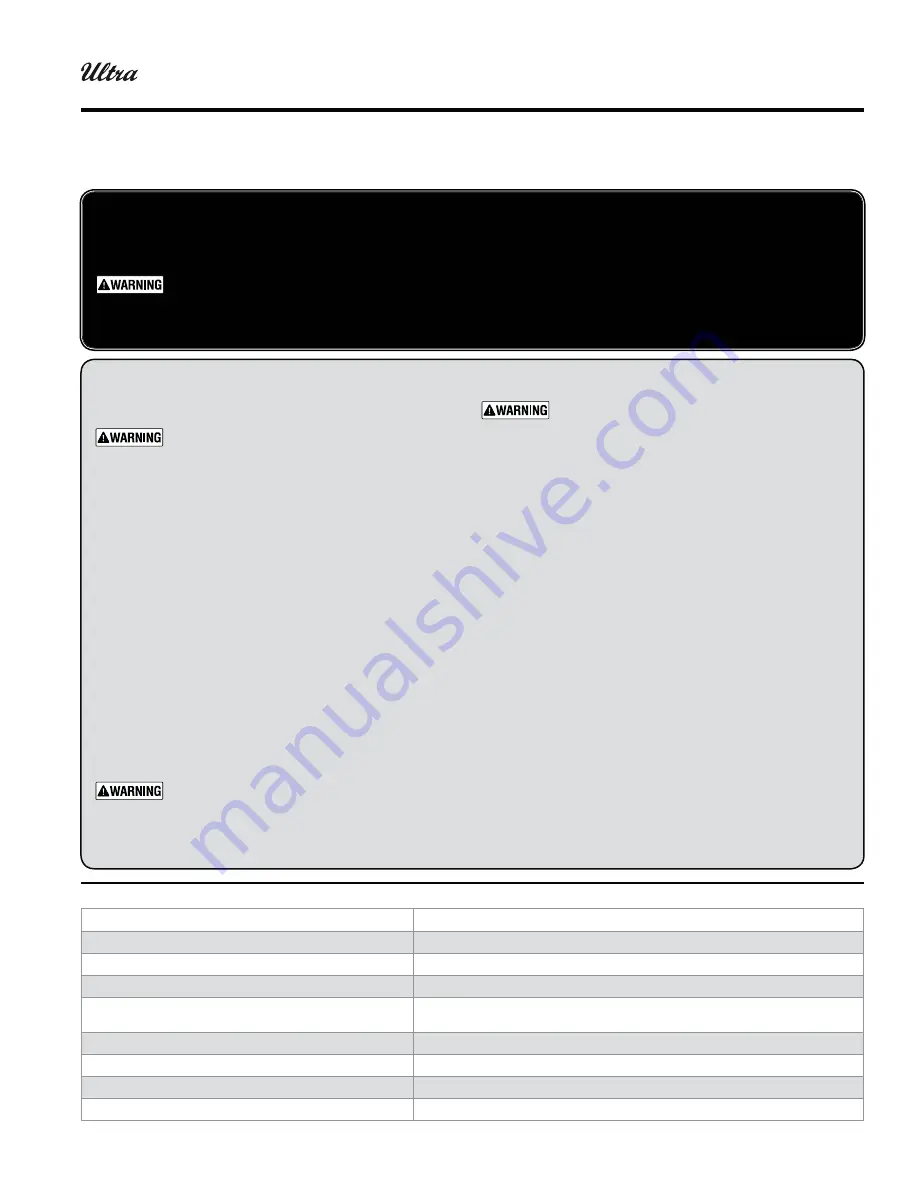
33
Part number 550-100-029/0810
GAS
-
FIRED
WATER
BOILER
SERIES
1 & 2
—
Control supplement & Service guide
Boiler maintenance procedure
VERIFY PROPER OPERATION AFTER SERVICING
(see Ultra Boiler Manual for procedures)
Removing and reinstalling components can change boiler behavior. After any maintenance procedure, you must
prove the boiler is operating correctly. To do so, follow the complete procedure for boiler and system start-up,
beginning on page 31 of the Ultra Boiler manual. Failure to comply could result in severe personal injury, death
or substantial property damage.
OBTAIN REQUIRED MAINTENANCE KIT
BEFORE PROCEEDING!
Removing heat exchanger and burner components
may damage gaskets or components. You must
have the following Weil-McLain Maintenance
kit available to correctly perform the required
maintenance procedures. Failure to complete
could result in severe personal injury, death or
substantial property damage.
For
5LTRA
or
5LTRA
— part number
383-500-605
(
in-
cludes igniter, igniter gasket, cover plate gasket, cover plate insulation,
burner gasket, venturi gasket, Sentinel inhibitor test kit
)
For
5LTRA
,
-230
or
-310
— part number
383-500-620
(
in-
cludes igniter, igniter gasket, cover plate gasket, cover plate insulation,
burner gasket, venturi gasket, Sentinel inhibitor test kit
)
In addition, for
!,,BOILERS
, obtain exchanger cleaning too,
Weil-McLain part number
.
DISCONNECT POWER BEFORE
PROCEEDING
%LECTRICAL SHOCK HAZARD
— Disconnect all
electrical power to the boiler before attempting
maintenance procedures. Failure to complete
could result in severe personal injury, death or
substantial property damage.
Re-install jacket front door
Re-install boiler jacket front door after servicing.
The boiler front door must be securely fastened
to the boiler to prevent boiler from drawing air
from inside the boiler room. This is particularly
important if the boiler is located in the same
room as other appliances. Failure to keep the door
securely fastened could result in severe personal
injury or death.
Clean and treat boiler water
Obtain Sentinel X100 inhibitor and Sentinel inhibitor test kit
from Weil-McLain.
After filling the system as directed in these instructions, use a
caulking gun to inject the X100 inhibitor into the system, fol-
lowing the instructions on the tube. Allow time for the water to
circulate and mix. Then check the inhibitor level. Add additional
inhibitor if necessary.
Test the pH of a sample of system water at least annually. The
pH of the water mixture must be between 7.0 and 8.5. (Or use
the Sentinel inhibitor test kit to check concentration.) If pH is
outside this range (or inhibitor test kit indicates low level), the
inhibitor level may not be sufficient to prevent corrosion. Add
X100 inhibitor if the need is indicated.
If antifreeze is used, use only antifreeze listed by Weil-McLain
as suitable for use with Ultra Gas Boilers. Follow all guidelines
provided. A list of approved antifreeze products is available at
www.Weil-McLain.com.
Tools and test equipment required for maintenance procedure, troubleshooting and combustion verification
&IGURE
4OOLSNEEDEDFORTROUBLESHOOTING
0URPOSE
25mm Torx screwdriver
change gas valve or to add orifice from natural to propane
7 mm Nut driver
burner screws
10mm & 11mm nut drivers
Front cover plate of heat exchanger
4 mm Allen wrench (long-handled) and/or 8mm open-
end wrench
Remove blower assembly from heat exchanger
Digital multi-meter
Read AC and DC voltage, read ohms
Gas manometer
Measure gas pressure
Combustion analyzer (Digital preferred)
Measure CO
2
, CO and O
2
Contact thermometer
For checking surface temperatures of heat exchanger and pipes