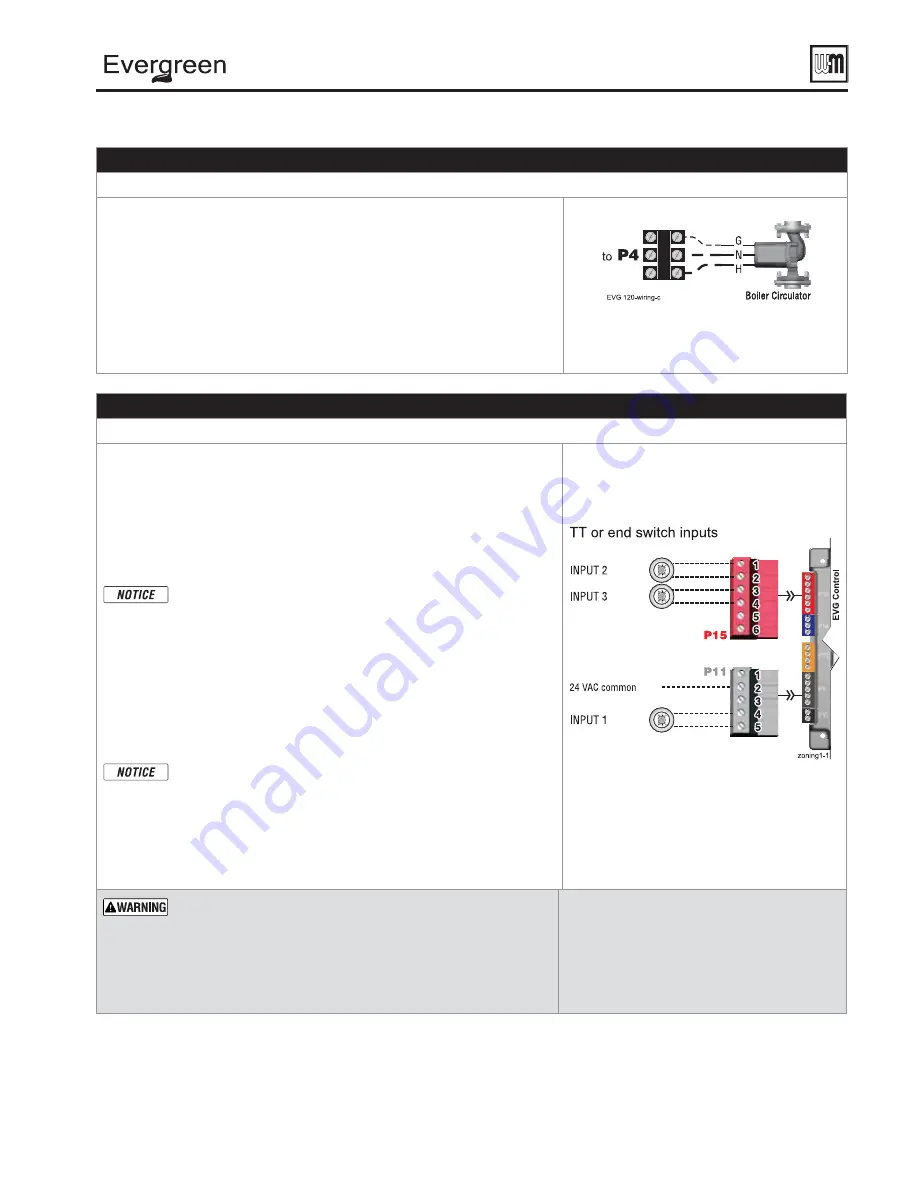
Part number 550-100-191/0917
57
®
g
as-fired water boiler —
70/110/155
Boiler Manual
Field wiring
(see wiring diagram, Figure 60, page 62 ) (continued)
C. 120 VAC to Boiler Circulator
–
REQUIRED
Boiler circulator terminal block to P4 on Control module
(terminal block)
1. Provides 120VAC to the boiler circulator at Boiler circulator terminal.
2. Terminals are: 1 (H), 2 (N), 3 (G).
3. Maximum load: 2.0 amps (use relay if circulator load is higher). See
WARNING above.
4. The boiler circulator (shipped loose with boiler) is used in the boiler loop
of the primary/secondary piping. Primary/secondary piping is required to
be used with the
Evergreen®
boiler to ensure proper fl ow through the heat
exchanger.
See
Figure 60, page 62
for details.
D. Inputs 1, 2 and 3 (tstats, end switches, etc.)
–
As needed for systems
Terminal Strip P11 (input 1) & Terminal Strip P15 (inputs 2 & 3)
(EVG control module)
1. Input 1 – Terminal Strip P11 – 4 & 5 (EVG control module)
2. Input 2 – Terminal Strip P15 – 1 & 2 (EVG control module)
3. Input 3 – Terminal Strip P15 – 3 & 4 (EVG control module)
4. These three inputs on each boiler can indicate a call for heat to the control
by means of a dry contact closure (thermostat, aquastat, or switch). (See
right and
Figure 60, page 62
).
5. The control provides inputs for up to three zones or three systems (priorities).
The control default setting is for three space heating zones tied to
PRIORITY 2, which is defaulted to FINNED TUBE BASEBOARD
system type.
6. For DHW applications, the aquastat can be connected to one of the
three input/output pairs. Take advantage of factory default settings by
using PRIORITY 1 for the DHW system. The default control setting for
PRIORITY 1 is a direct-piped DHW system type.
7. The default control setting uses each input (INPUT 1, INPUT 2, and
INPUT 3) to control its respective 120VAC output (OUTPUT 1, OUTPUT 2,
and OUTPUT 3).
Use of 0–10VDC input for modulation disables Input 1 from
creating calls for heat. See page 61 for instructions.
An input can be assigned to an AUX PUMP/OUTPUT function to
operate a system pump or interlock with a combustion air damper.
Inputs assigned for this function cannot be used for heat demand
operation. See page 82 and page 83 for more information on the
setup and selection of operating conditions.
See
Figure 60, page 62
for details.
Thermostats
—
DO NOT
supply 24-volt power to the thermostat
circuits (Input1, Input2 and Input3 in
Figure 60, page 62
) or
attempt to supply 24 volts for any other application.
For thermostats that require a continuous 24-volt power
source, connect the common wire (“C”) to
P11
Pin 2 (see
Figure 60, page 62
).
Do NOT exceed total amp draw per thermostat.
Zone valves
— If using 3-wire zone valves, use
relays to provide dry contacts to the Control
thermostat connections. The zone valve end
switches of 3-wire valves carry 24 VAC from the
valve.
Thermostat anticipator setting
— 0.1 amps.
Summary of Contents for Evergreen EVG 110
Page 71: ...Part number 550 100 191 0917 71 gas fired water boiler 70 110 155 Boiler Manual Notes...
Page 90: ...Part number 550 100 191 0917 90 gas fired water boiler 70 110 155 Boiler Manual Notes...
Page 116: ...Part number 550 100 191 0917 116 gas fired water boiler 70 110 155 Boiler Manual Notes...