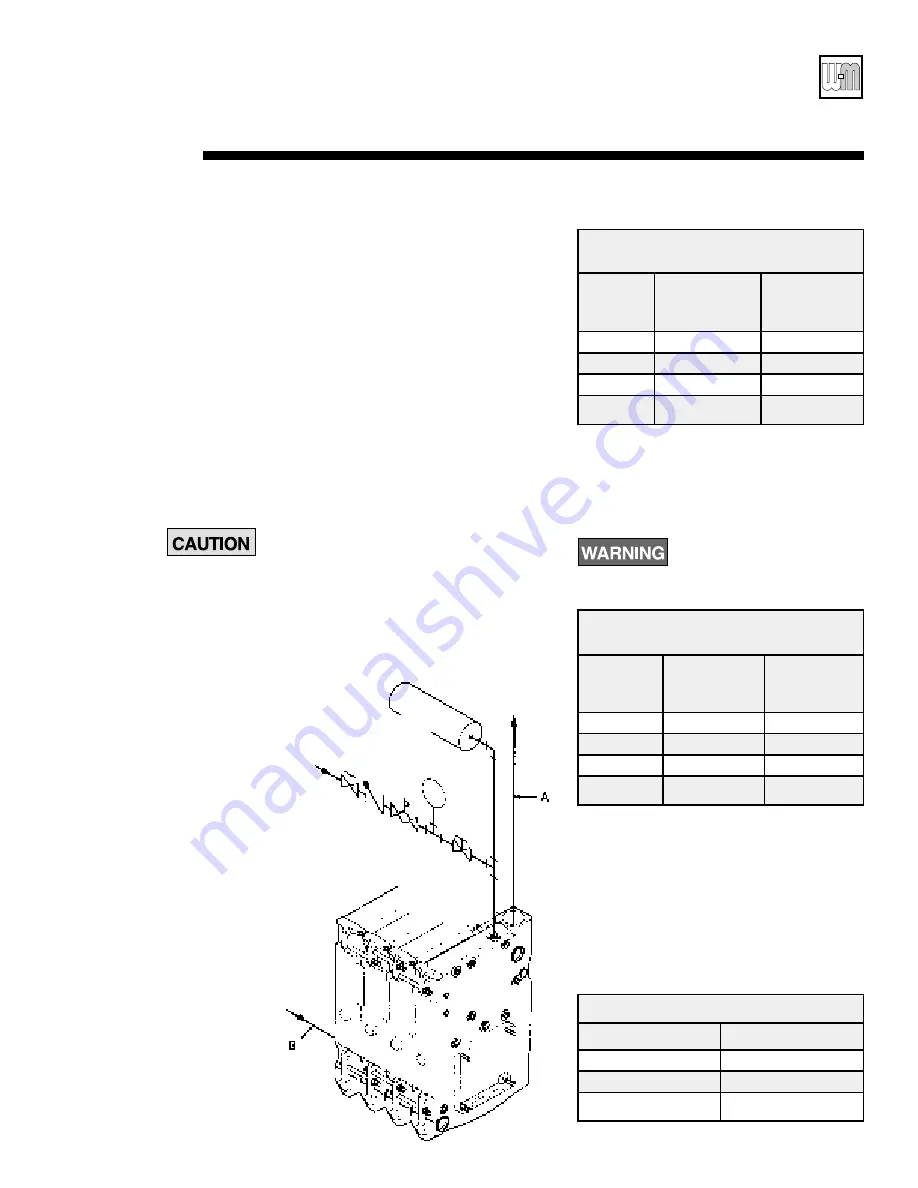
General water piping information:
• System water supply and return piping should
be installed and piping connections attached to
boiler before erecting jacket or installing
controls.
• Do not pipe in through supply and out through
return. This creates reverse water flow through
boiler that must not be used.
• When three-way valves are used for
temperature modulation, install slow-opening
(minimum 10-minute) valves and boiler
mixing pump to minimize potential of boiler
thermal shock. See W-M Bulletin AE-8402.
Install piping:
Install piping as shown in Figure 12 below for
single boilers, page 14 for multiple boilers.
Improperly piped systems or undersized piping
can contribute to erratic boiler operation and
possible boiler or system damage.
1. Connect supply and return piping:
a. Size according to tables below.
1) For
unknown flow rates,
size piping
per Table below, using 20°F. temperature
rise through boiler.
* All piping sizes based on 20°F. temperature
rise through boiler.
2) For
known flow rates or higher flow
rate
through boiler, size piping per Table
below.
Flow at higher velocities than
shown in Table below for pipe
size can damage boiler, causing
substantial property damage.
b. Locate circulator in supply piping.
c. For return piping, use full diameter pipe for
10 times that diameter before making any
reduction. For example, a 4-inch return
should not be reduced any closer to boiler
return tapping than 40 inches.
d. Install system blow-off (drain) valve in
lowest part of return piping close to boiler.
ASME Size requirements are shown in
Table below.
Recommended Minimum Pipe Sizes
for Unknown Flow Rates*
Supply
Return
Boiler
Pipe Size
Pipe Size
Model
A
B
378
2"
2"
478
2-1/2"
2-1/2"
578-678
3"
3"
778-1278
4"
4"
• Installation • Start-Up • Maintenance • Parts
Connect Water Boiler Piping
5a
Part No. 550-141-705
13
Recommended Minimum Pipe Sizes
for Known Flow Rates
Water Supply
Return
Flow Rate
Pipe Size
Pipe Size
GPM
A
B
Up to 35
2"
2"
36 to 50
2-1/2"
2-1/2"
51 to 77
3"
3"
78 to 142
4"
4"
ASME Drain Valve Size
Boiler Model
Valve Size (in.)
378-478
3/4
578-1178
1
1278
1-1/4
Cold
water fill
Expansion
tank
System
supply
(front only)
System return
(front or rear)
Manual
isolation
valve
Manual
isolation
valve
Pressure
reducing
valve
(when used)
Figure 12 Water Boiler Piping
Check
valve
Water
meter