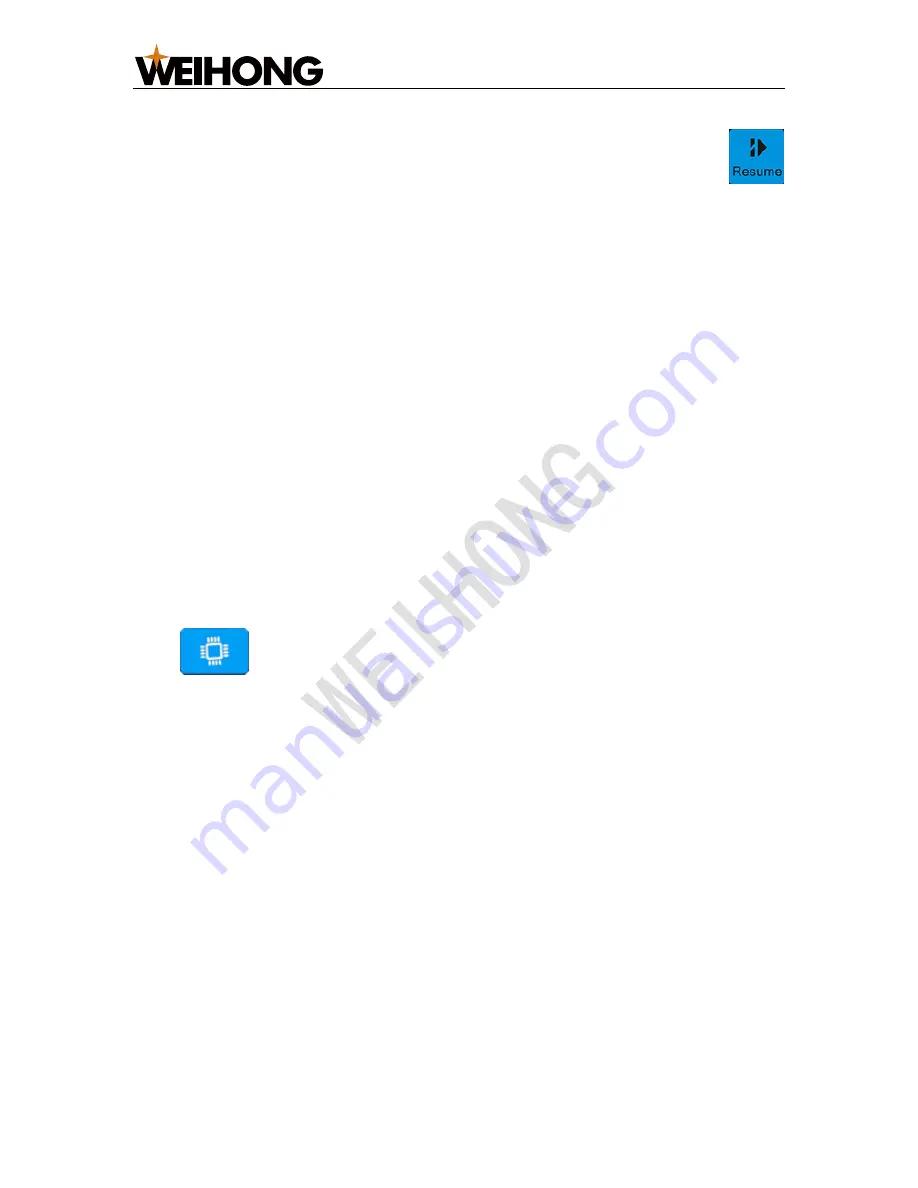
上海维宏电子科技股份有限公司
SHANGHAI WEIHONG ELECTRONIC TECHNOLOGY CO., LTD
50
/
53
•
To resume machining from the exact interrupted position when power
interruption or E-stop occurs and the workpiece origin is secured, press
.
4
FAQs (Operator)
Through this section, you can know the following frequently asked questions by
operators during use, and their corresponding causes and solutions for
troubleshooting:
•
Failed to register the system.
•
Tool calibration overtravel alarm.
•
If the solution does not work or you have any other questions, please contact with
our sales engineers.
4.1
Failed to Register the System
Cause
You exited
System
interface during registering the system.
Solution
Press
→
1
to enter into
Sys.
interface, take a picture of the interface, send it
to your manufacturer, and stay at the interface until the end of registration.
Note:
Once you exited
System
interface, you need to take the picture and send it to your manufacturer
again.