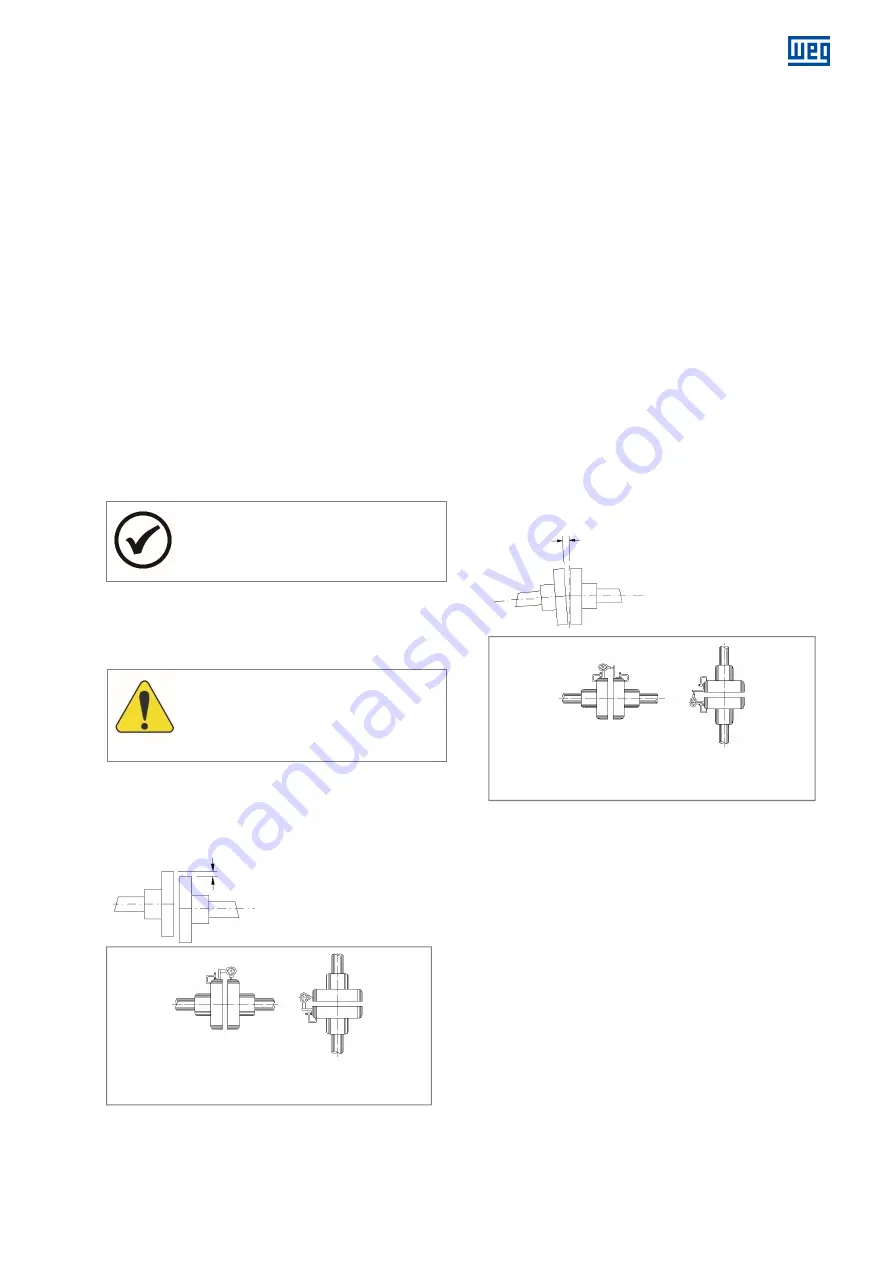
14108242 Installation, operation and maintenance manual – Squirrel cage motor – WGM20 Line l 27
In order to verify if the criteria of the standard are being
met, the following potential vibration excitation frequencies
generated by the motor and coupled machine must be
checked:
The motor rotation frequency;
The double of the rotation frequency;
The double of the motor electric frequency.
According to DIN 4024-1 standard, the natural
frequencies of the base or foundation must be away from
these potential excitation frequencies, as specified next:
The first natural frequency of the base or foundation
(first order natural frequency of the base) must be out of
the range from 0.8 to 1.25 times any of the potential
excitation frequencies above;
The other natural frequencies of the base or foundation
must be out of the range from 0.9 to 1.1 times any of
the potential excitation frequencies above.
4.8.5
Leveling
The motor must rest on a surface with flatness of up to
0.08 mm/m.
Verify whether the motor is perfectly leveled, both in the
vertical and horizontal planes. Make the proper
adjustments by placing shims under the motor. The motor
leveling must be checked with proper equipment.
NOTE
At least 75% of the motor foot support
surfaces must rest on the motor base.
4.8.6
Alignment
The motor must be correctly aligned with the driven
machine.
ATTENTION
Incorrect alignment can damage the
bearings, generate excessive vibration and
even break the shaft.
The alignment must be done according to the coupling
manufacturer recommendations.
The motor and driven machine shafts must be aligned in
the axial and radial directions, as shown in Figure 4.9 and
Figure 4.10.
Figure 4.9: Parallel alignment
Figure 4.9 shows the parallel misalignment of the two
shaft ends and the practical way to measure it by using
suitable dial gauges.
The measurement is performed in four points 90° away
from each other with the two half-couplings rotating
together in order to eliminate effects of support surface
irregularities on the dial gauge tip. Choosing the upper
vertical point as 0°, half of the difference between the dial
gauge measurements at the 0° and 180° points
represents the vertical coaxial error. In case of deviation, it
must be corrected by adding or removing leveling shims.
Half of the difference between the dial gauge
measurements at the 90º and 270º points represents the
horizontal coaxial error.
These measurements indicate when it is necessary to lift
or lower the motor, or move it to the right or to the left on
the drive end in order to eliminate the coaxial error.
Half of the maximum difference among the dial gauge
measurements in a complete rotation represents the
maximum eccentricity found.
The misalignment in a complete shaft rotation, with rigid or
semiflexible coupling, cannot exceed 0.03 mm.
When flexible couplings are used, greater values than
those indicated above are acceptable, provided that they
do not exceed the value allowed by the coupling
manufacturer.
It is recommended to keep a safety margin for these
values.
Figure 4.10: Angular alignment
Figure 4.10 shows the angular misalignment and a
practical form to measure it.
The measurement is done in four points 90° away from
each other, with the two half-couplings rotating together in
order to eliminate effects of support surface irregularities
on the dial gauge tip. Choosing the upper vertical point as
0°, half of the difference between the dial gauge
measurements at the 0° and 180° points represents the
vertical misalignment. In case of deviation, it must be
corrected by adding or removing alignment shims.
Half the difference between the dial gauge measurements
at the 90° and 270° points represents the horizontal
misalignment, which must be properly corrected by
displacing the motor in the lateral/angular direction.
Half of the maximum difference among the dial gauge
measurements in a complete rotation represents the
maximum angular misalignment found.
The misalignment in a complete shaft rotation, with rigid or
semiflexible coupling, cannot exceed 0.03 mm.
Horizontal Mounting Vertical Mounting
Radial measurement
Parallel misalignment
Horizontal Mounting
Vertical Mounting
Axial measurement
Angular misalignment