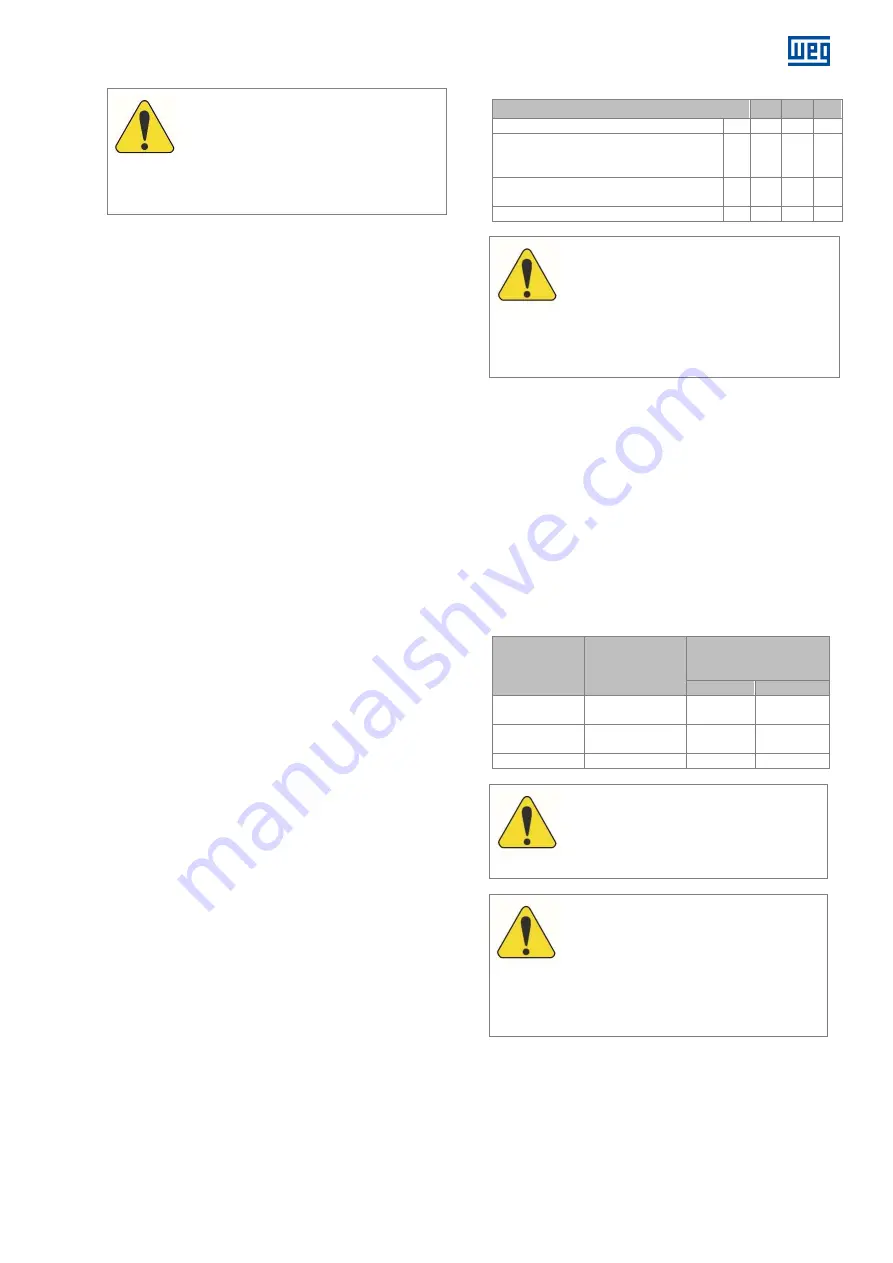
14108242 Installation, operation and maintenance manual – Squirrel cage motor – WGM20 Line l 21
ATTENTION
If the measured insulation resistance,
referred to 40 ºC, is below 100 M
Ω
or the
polarization index is below 2, than before
putting the motor into operation, consult
WEG.
4.5
PROTECTIONS
Motors used in continuous duty must be protected
against overloads by means of a motor integral device, or
an independent protection device, which is generally a
thermal relay with rated or adjustable current equal to or
below the value obtained by multiplying the full load motor
supply current by:
1.25 for motors with service factor equal to or above
1.15;
1.15 for motors with service factor equal to 1.0.
Motors also have protection devices against overheating
(in cases of overloads, locked rotor, low voltage, lack of
motor ventilation).
4.5.1
Thermal protections
The over-temperature protections devices are installed on
the main stator, bearings and other parts that require
temperature monitoring and thermal protection.
These sensors must be connected to an external
temperature monitoring and protection system.
The type of temperature sensor, the connection terminals
and the setting temperatures for alarm and shutdown are
given in the motor CONNECTION DIAGRAM.
4.5.2
Temperature limits for the windings
The temperature of the hottest spot of the winding must
be kept below the limit of the insulation thermal class. The
total temperature is obtained by the sum of the ambient
temperature and the temperature rise (T), plus the
difference between the average temperature of the
winding and the hottest spot of the winding.
The ambient temperature must not exceed 40 °C, in
accordance with NBR IEC60034-1 standard. Above this
temperature, the working conditions are considered
special and the motor specific documentation must be
consulted. The Table 4.4 shows the numerical values and
the composition of the acceptable temperature at the
hottest spot on the winding.
Table 4.4: Insulation class
Insulation class
B
F
H
Ambient temperature
°C 40
40 40
T = temperature rise (temperature
measurement method by resistance
variation)
°C 80 105 125
Difference between the hottest spot and
the average temperature
°C 10
10 15
Total: temperature of the hottest point
°C 130 155 180
ATTENTION
If the motor operates with winding
temperatures above the limits of the insulation
thermal class, the lifespan of the insulation, and
hence that of the motor, will be significantly
reduced, or it may even result in the motor
burnout.
4.5.3
Alarm and trip temperatures
The motor alarm and trip temperatures must be set at the
lowest possible value. These temperatures can be
determined based on the factory tests or through the
motor operating temperature. The alarm temperature can
be set 10ºC above the machine operating temperature at
full load, always considering the highest ambient
temperature on site. The adjusted trip temperatures must
not exceed the maximum admissible temperatures for the
stator winding insulation class and for the bearings
(considering the lubrication type and system), according
to Table 4.5.
Table 4.5: Maximum temperature settings
Component
Temperature
rise (∆t)
Maximum temperature
settings for protections
(ºC)
Alarm
Trip
Winding class F
(155°C)
Class B
120
130
Winding class F
(155°C)
Class F
130
155
Bearings
-
110
120
ATTENTION
The alarm and trip values may be determined
as a result of experience, but they must not
exceed the values indicated in Table 4.5.
ATTENTION
The motor protection devices are listed in the
WEG drawing – Connection diagram.
Not using these devices is the sole
responsibility of the user and, in case of
damage to the motor, it will void the
warranty.