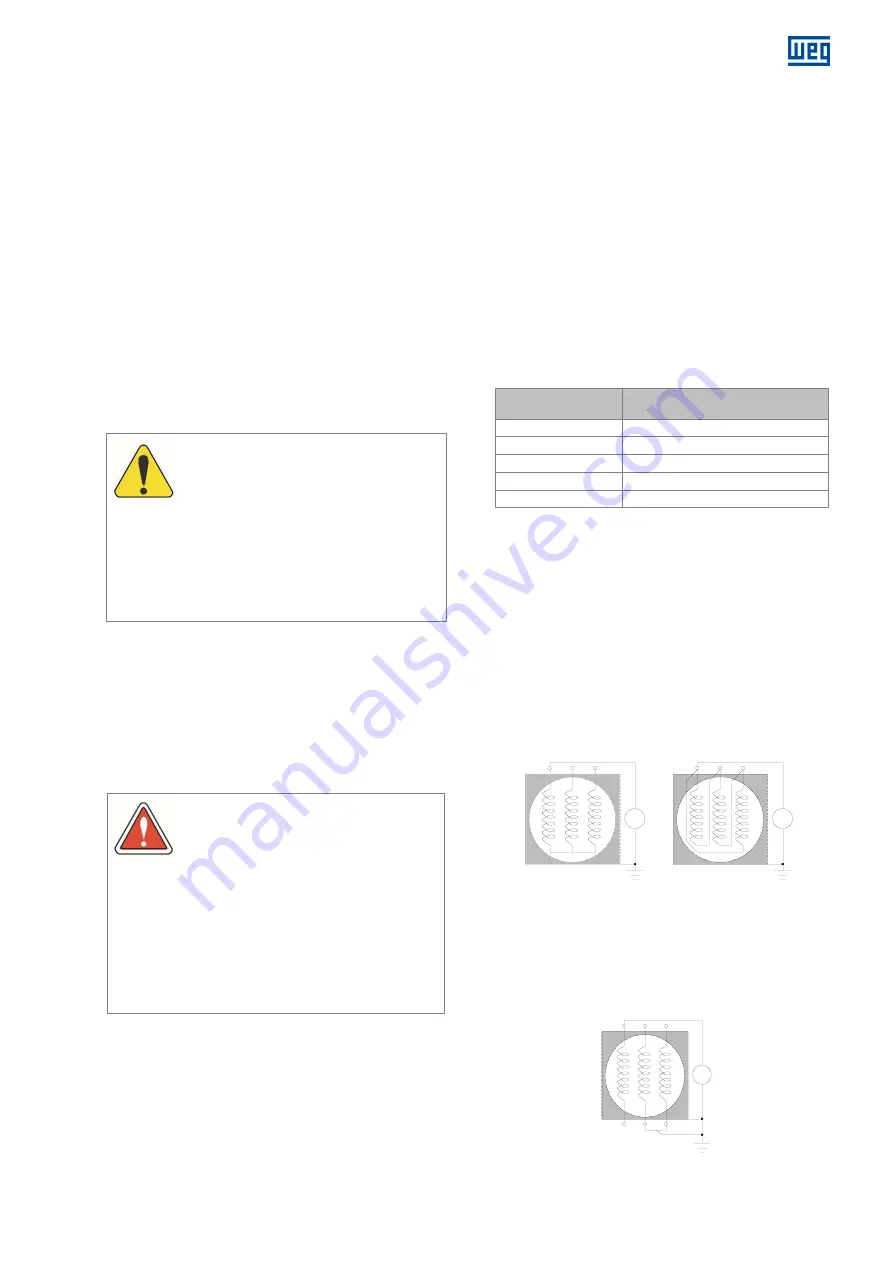
14108242 Installation, operation and maintenance manual – Squirrel cage motor – WGM20 Line l 19
4
INSTALLATION
4.1
INSTALLATION SITE
Electric motors must be installed in easily accessible
places, allowing periodic inspections, on-site maintenance
and, if necessary, removal for external services.
The following environmental conditions must be ensured:
Clean and well-ventilated location;
The installation of other equipment or walls must not
block or hinder the motor ventilation;
The area around and above the motor must be
sufficient for maintenance or handling;
The environment must be in accordance with the motor
protection degree.
4.2
SHAFT LOCK
The motor leaves the factory with a lock on the shaft to
prevent damages to the bearings during transportation.
This lock must be removed prior to motor installation.
ATTENTION
The shaft-locking device must be installed
whenever the motor is removed from its base
(uncoupled) in order to prevent damages to
the bearings during transportation.
The shaft end is protected at the factory with
a temporary protective agent (rust inhibitor).
During the motor installation, it is necessary
to remove this product from the grounding
brush (if any) contact track on the shaft.
4.3
ROTATION DIRECTION
The motor rotation direction is indicated by a plate affixed
to the frame on the drive end and in the motor specific
documentation.
4.4
INSULATION RESISTANCE
4.4.1
Safety Instructions
DANGER
In order to measure the insulation resistance,
the motor must be turned off and stopped.
The winding being tested must be connected
to the frame and grounded until all residual
electrostatic charges are removed.
Capacitors (if any) must also be grounded
before disconnecting and separating the
terminals to measure the insulation
resistance.
Failure to comply with these procedures may
result in personal injury.
4.4.2
General considerations
When the motor is not immediately put into operation, it
must be protected against moisture, high temperatures,
and dirt, thus avoiding impacts on the insulation
resistance.
The winding insulation resistance must be measured
before putting the motor into operation.
If the environment is too humid, the insulation resistance
must be measured periodically during storage. It is difficult
to establish fixed rules for the actual value of winding
insulation resistance, as it varies according to the
environmental conditions (temperature, humidity), machine
cleanliness conditions (dust, oil, grease, dirt) and quality
and condition of the insulating material used.
The evaluation of the periodical follow-up records is useful
to conclude whether the motor is able to operate.
4.4.3
Measurement on the stator windings
The insulation resistance must be measured with a
megohmmeter
. The testing voltage for the motor
windings must be in accordance with Table 4.1
the winding Insulation resistance test
and IEEE43 standard.
Table 4.1: Voltage for the winding Insulation resistance test
Winding rated
voltage (V)
Insulation resistance test -
continuous voltage (V)
< 1000
500
1000 - 2500
500 - 1000
2501 - 5000
1000 - 2500
5001 - 12000
2500 - 5000
> 12000
5000 - 10000
Before measuring the stator winding insulation resistance:
Disconnect all connections to the stator terminals;
Disconnect and insulate all CTs and PTs (if any);
Ground the motor frame;
Measure the winding temperature;
Ground all temperature sensors;
Check the humidity.
The insulation resistance measurement of the stator
windings must be done in the main terminal box.
The megohmmeter must be connected between the
motor frame and the winding.
The frame must be grounded and the three phases of the
stator winding must remain connected to the neutral point,
according to Figure 4.1.
Figure 4.1: Megohmmeter connection
Whenever possible, each phase must be isolated and
tested separately. The separate test allows the
comparison between the phases. When a phase is tested,
the other two phases must be grounded to the same
ground of the frame, according to Figure 4.2.
Figure 4.2: Connection of the megohmmeter to separate phases
M
Ω
M
Ω
M
Ω