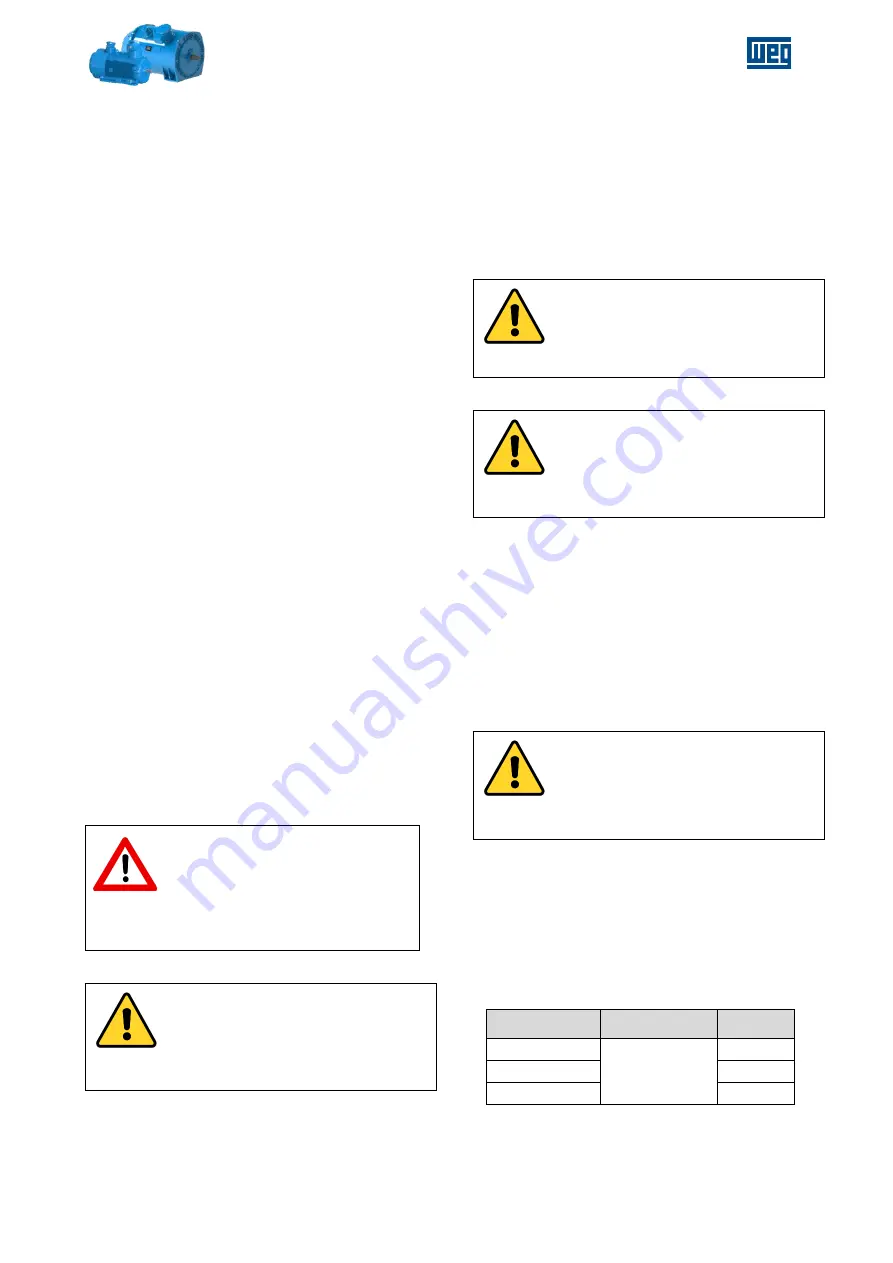
Flameproof motors | 49
www.weg.net
axial surfaces of the locating bearing are not
damaged.
After the split faces of the bottom liner half and the
housing base are aligned, lower the shaft into
place. With a slight hammer blow against the
housing base settle the liner into its seating so that
the liner axis and shaft axis are parallel. The slight
hammer blow produces a high frequency vibration
which reduces the static friction between the liner
and the housing and allows the correct adjustment
of the liner. The self-alignment feature of the
bearing is to compensate for normal shaft
deflection during the assembling procedure only.
The loose oil ring is installed next. The ring must be
handled with special care as safe operation of the
bearing is also dependent on the effective and safe
functioning of the oil ring. The bolts must be tightly
fastened. Split misalignment must be avoided and
any burrs or edges carefully removed in order to
ensure smooth running of the ring. In any
maintenance care must be taken that the ring is not
distorted and its geometrical shape is maintained.
The outside of the two liner halves is stamped with
identification numbers or marks near the split line.
Make sure that these marks align and the split
faces are clean when placing the top liner half into
position. Incorrect fitting may lead to heavy
damage to the bearing liners.
Check to ensure that the loose oil ring can still
rotate freely on the shaft. With the top liner half in
place, install the seal on the flange side (see
paragraph "Shaft Seals").
After coating the split faces with a non-hardening
sealing compound, place the housing cap into
position. Care must be taken that the seal fits
properly into the groove. Ensure also that the anti-
rotation pin is seated without any contact with the
corresponding hole in the liner.
DANGER
When assembling the fan cover of
sleeve bearing motors care must be
taken to correctly align the fan air
defletor to avoid rubbing between
parts.
ATTENTION
Housing or liner may be interchanged
as
complete
assemblies
only.
Individual
halves
are
not
interchangeable.
8.2.10.5 SETTING
OF
THERMAL
PROTECTIONS (PT100)
Each bearing is fitted with a Pt100 temperature
detector installed directly in the bearing liner near
the point where the load is applied. This device
must be connected to a controlling panel with the
purpose of detecting overheating and protect the
bearing when operating under high temperature.
ATTENTION
Alarm and tripping temperatures for
bearings system must be set for 110ºC
and 120ºC respectively.
ATTENTION
The alarm temperature should be set
at
10°C
above
the
working
temperature, not exceeding the limit of
110°C.
8.2.10.6 WATER COOLING SYSTEM
When using water cooling system, the oil reservoir
at the bearing is equipped with cooling coils
through which the water circulates. This circulating
water must present at the bearing inlet a
temperature smaller or equal to the ambient
temperature in order to make the cooling possible.
The water pressure must be 0.1 bars and the water
flow must be 0.7 L/s. The pH must be neutral.
ATTENTION
When connecting the cooling coils,
leaks in or on the bearings housing and
oil reservoir must be avoided so that
lubricating oil is not contaminated.
8.2.10.7 LUBRICATION
SELF LUBRICATED BEARINGS
Oil change -
The change of the oil in the bearings
should be made according to the table below,
referring the bearing working temperature:
Table 8-17 - Oil change intervals and quantity
Bearing size
Lubrication
interval (hours)
Oil quantity
(liters)
9
8000
2.8
11
4.2
14
8