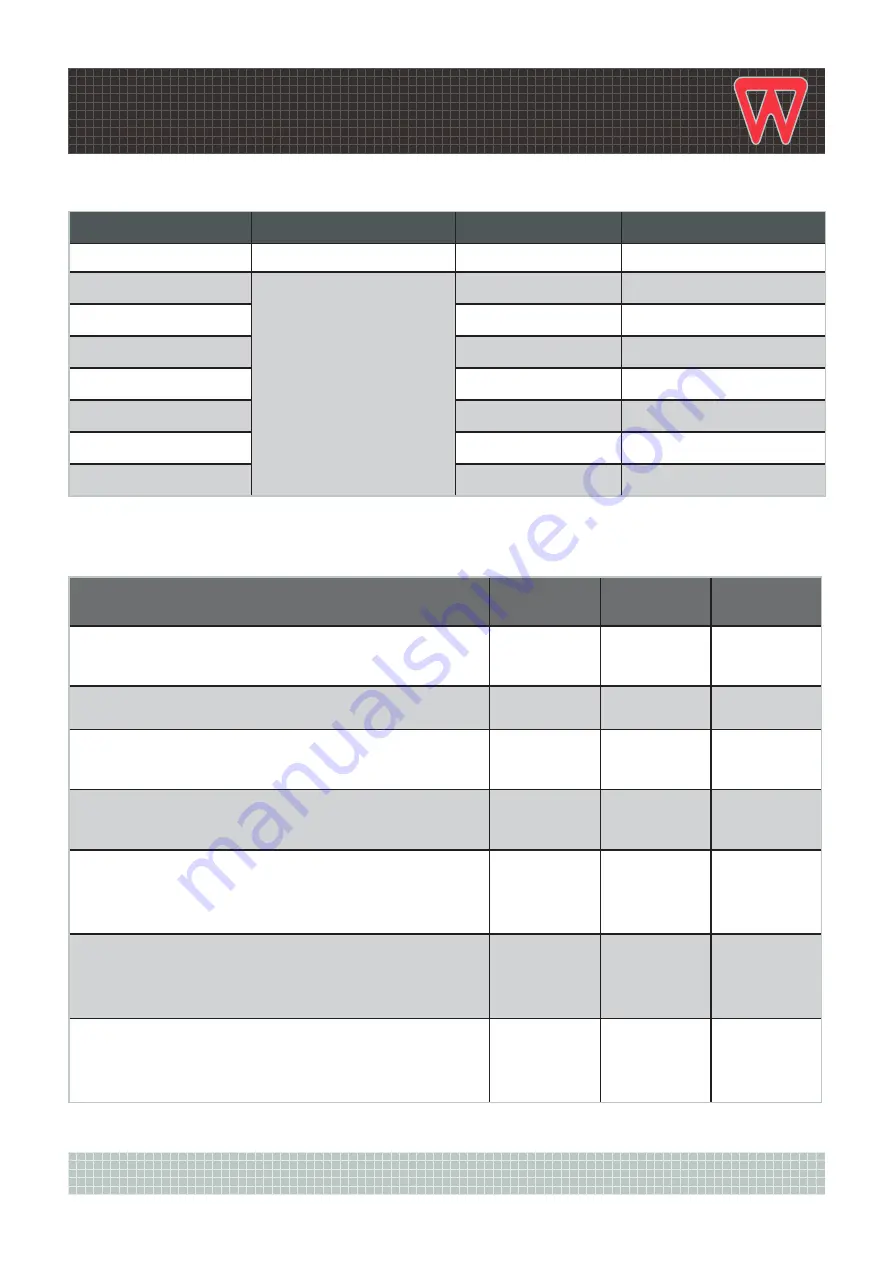
Parts & Service 01/12/2016
902-001-13 Rev 3
Page 17
SECTION 4:
Tables
4.1 TABLE OF SETTINGS
Product Code
Operating Pressure
Flow Rates
Extend Cylinder Rod
Bar (PSI)
l/m in (gal/m in)
mm
TNH-015-022
200 (2900)
2.9 (0.8)
10
TNH-028-037
6.3 (1.7)
10
TNH-045-055
11.7 (3.1)
10
TNH-070-099
28.0 (7.4)
10
TNH-130-170
57.0 (15.0)
10
TNH-210-270
76.0 (20.0)
10
TNH-320-450
132.0 (35.0)
40
4.2 MAINTENANCE SCHEDULE
Maintenance Required
Daily
Weekly
Monthly
Check all pin retainers, bolts & nuts for tightness on
the bucket and thumb. Include pin end cap bolts.
ü
Lubricate all greasing points.
ü
Check hydraulic hoses and fittings for any leaks or
wear – replace immediately if required.
ü
Check the hydraulic cylinder mounting bolts for
tightness – remedy if required.
ü
Thoroughly clean the thumb and ensure there is no
material build up around cylinder mounting point and
pin.
ü
Check the thumb for evidence of fatigue, weld failure
or stress – if evident contact your Wedgelock dealer
immediately for assistance.
ü
Check thumb alignment with bucket teeth. Should
alignment have changed, new shims may be
required.
ü