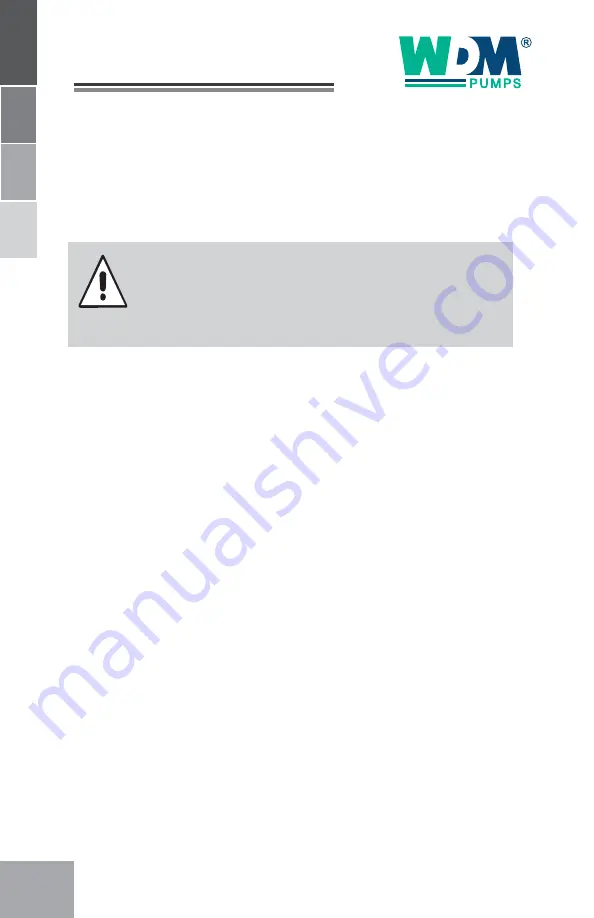
Operation Manual.
12
Packing gland adjustment.
With the pump running,
adjust the packing gland to permit 40 to 60
drops per minute leakage. This is necessary for shaft lubrication.
After the initial startu p, som e additional adjustment may be
required.
All pumps on GE & GU line of WDM Pumps are equipped with
mechanical seals matched to the specific conditions for which the
pump was sold.
To avoid damage to the seal, and to maximize seal life observe the
following precautions:
•
Stay within the temperature or pressure limitations specified
for the mechanical seal used.
•
Do not run the pump dry or against a closed valve! Dry
operation will cause seal failure within minutes.
•
Clean and flush the suction piping before installing and
operating pump. Abrasives including pipe scale, welding slag
and others can
rapidly cause seal failure.
Coupling Alignment.
•
This is a standard anchoring and alignment procedure. If per
formed with care, i t should result in a trouble-free
installation.
•
If the pump and motor were shipped
as an assembly,
mounted on the pump base, remove the coupling guard.
•
Pump and motor where align at factory but handling during
shipping and receiving can shift alignment.
•
Pump and motor should be realign prior to final installation an
operation of the pump.
ATTENTION.
Pumps with mechanical seals require no adjustment. If the
mechanical seal is altered or replaced
with a packing gland,
adjustments may become necessary.