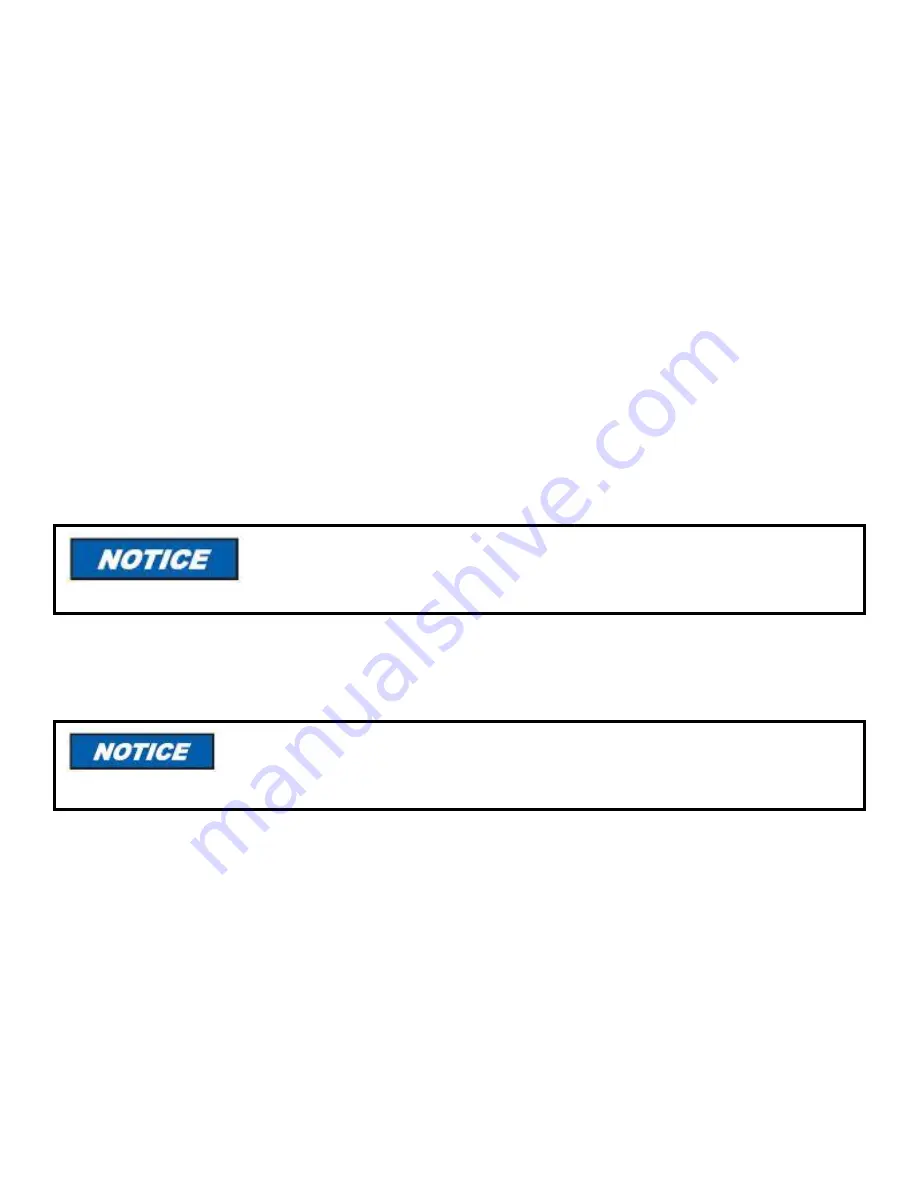
22
GENERAL INSTALLATION INFORMAT
I
ON
When installing the burner, be sure to provide adequate space for easy service and maintenance. Prior to installation of
the oil burner, the heating system should be carefully inspected for defects and cleanliness. The flue passages and heat
absorbing surfaces must be clean to ensure maximum heat transfer. Soot acts as an insulator, which decreases the
transfer of heat. The combustion chamber, flue gas passages, and openings must be tightly sealed to eliminate air
infiltration. Excess air cools the flame and thus lowers efficiency. Inspect the flue for leaks and obstructions.
COMBUSTION CHAMBER
The purpose of a combustion chamber is to maintain a high flame temperature by reflecting the heat back into the flame.
A high flame temperature assures higher combustion efficiency and lower stack losses. It is important to select and install,
the correct nozzle size for a given combustion chamber size (see Table 5 on page 35). On all oil burners the atomized oil
must not touch the sides or bottom of the combustion chamber or incomplete combustion will occur leading to smoke and
soot build-up. To reduce smoke while the burner is running, the burner must have an adequate supply of combustion air
by having a large enough opening on the air band assembly. If too much air is utilized it can lead to high gas exhaust
temperatures, and lower combustion efficiency. Install the burner according to the equipment
manufacturer’s guidelines.
FUEL PUMPS
Model EHASR-DC and EH-DC oil burners are provided with single stage 3450 RPM fuel pumps with the by-pass plug
removed for a single pipe installation. This is satisfactory where the fuel supply is on the same level, or above burner,
permitting gravity flow of oil.
When it is necessary to lift the oil to the burner, a return line should be run between the fuel pump and oil tank. (If lift
exceeds 10 feet, a two stage fuel pump must be used with a return line). When a two line installation is made, the by-pass
plug must be installed. This is supplied with the burner attached to fuel pump, along with a pump data sheet in a plastic
bag.
FUEL LINES
Replace fuel lines with parts approved by the equipment manufacturer. Be sure that all connections are air-tight. Check all
connections and joints. Flared fittings are recommended. Do not use compression fittings. Avoid using fittings in
inaccessible locations. Install an UL certified oil filter of adequate size for all installations.
FUEL TANKS
Check existing tanks for water and sludge accumulation; clean if necessary. Also clean or replace existing piping.
Never exceed 3 PSI pressure to the suction side of the fuel pump. A pressure over 3 PSI
may cause damage to the shaft seal and allow it to leak oil.
Do not install by-pass plug if running single pipe operation, this will over-pressurize the pump
causing an oil leak at the pump shaft seal.