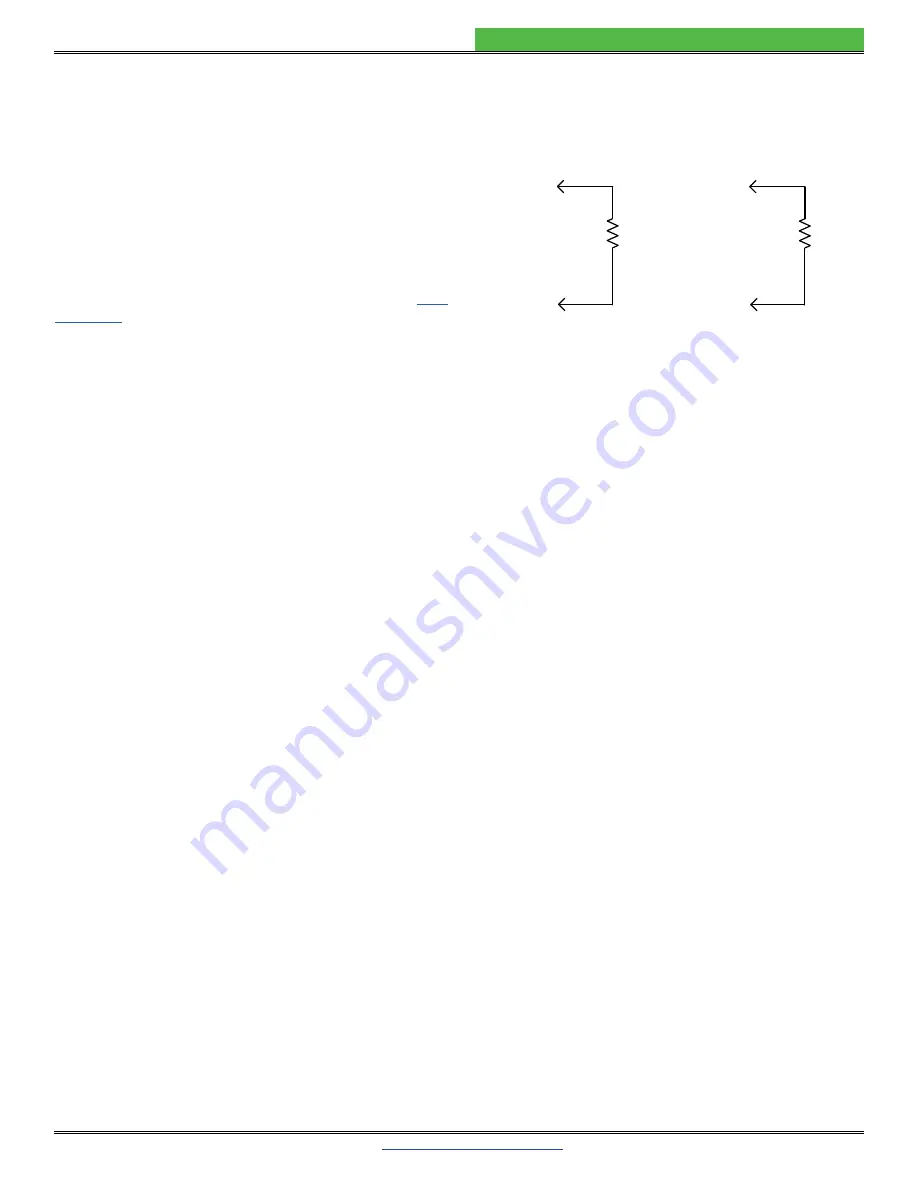
© 2022
3
WHY56ND TEMPERATURE CONTROLLER
QUICK CONNECT GUIDE, cont’d
Figure 3.
Test Load Configuration
RECOMMENDED TEST LOAD
For setup and configuration, we recommend using a test
load in place of the Thermoelectric Cooler (TEC) or resistive
heater, connected directly to Pin 9 and Pin 13 on the
controller, as shown in
NOTE:
Use a max of +5 V power supply with the test
load shown. Values shown can simulate any load up to
the WHY56ND maximum of 2.2 A. Always check the
before operating the WHY56ND controller.
R1
R1 = 10 kΩ, ¼ W resistor
SENS
ERR
Simulated Thermistor
R
LOAD
OUTB
OU
T
A
R
LOAD
= 1 Ω, Rated >25 W
Thermal
Test Load