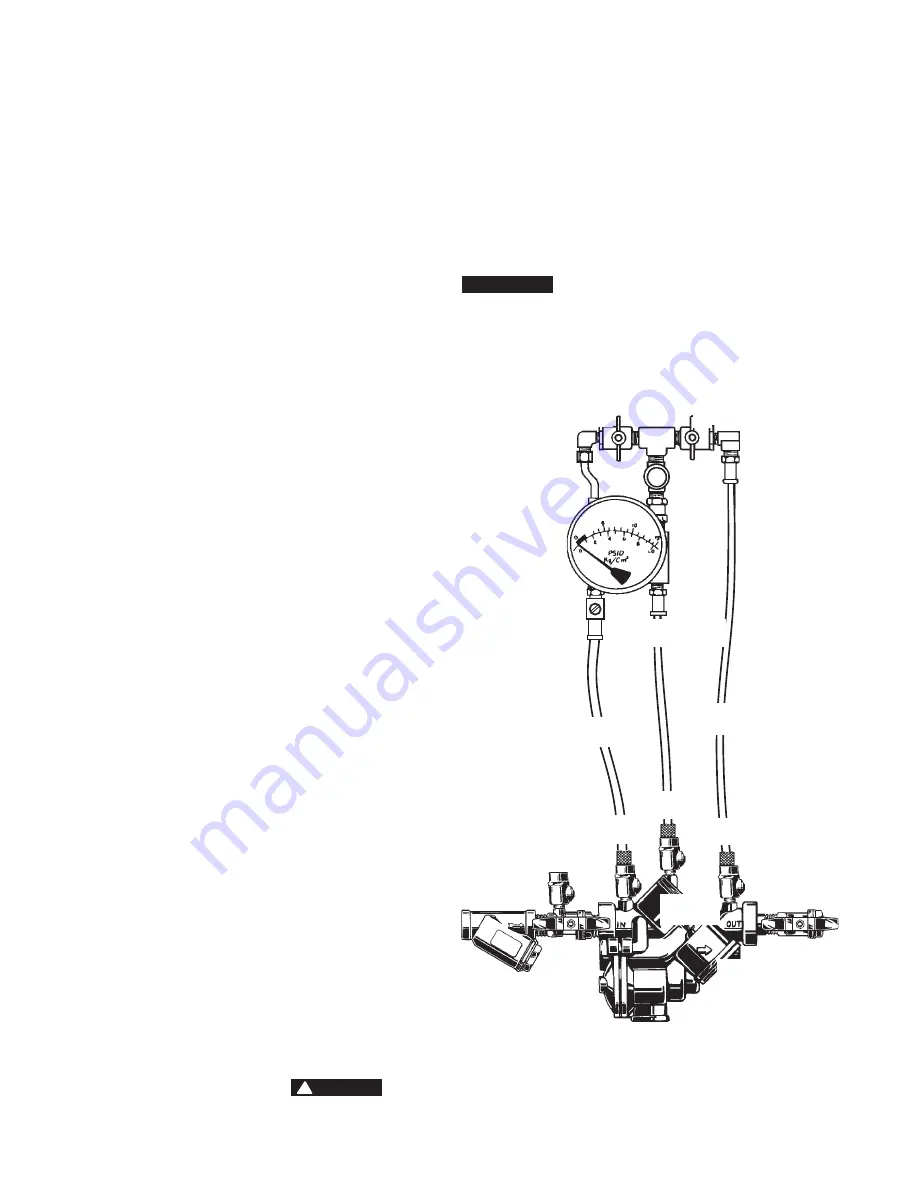
2
Reduced Pressure Zone Backflow Preventers must be
inspected and tested periodically,
in accordance with local codes, to ensure proper operation of
check valves within the unit. A differential pressure gauge is
recommended for Test No. 1 rather than a manometer for the
following reasons: It utilizes minimum time to perform the test.
It eliminates the necessity of closing the inlet ball valve which
could release pipe scale and foreign matter into the backflow
preventer. Only a slight amount of water is ‘spilled’ in test. A
mercury manometer could cause a pollution hazard.
Test Set Up
Reduced Pressure Zone Assembly
Close Valves A, B and C on Test Kit.
Connect high side hose to test cock #2
Connect low side hose to test cock #3. Close shutoff #2.
Open test cocks #2 and #3.
Open vent valve C.
Open ‘high’ valve A and bleed to atmosphere until all the air
is expelled.
Close valve A. Open ‘low’ valve B and bleed to atmosphere until
all air is expelled. Close ‘low’ valve B. Close ‘vent’ valve C.
Connect vent hose to test cock #4.
Test Procedure
Reduced Pressure Zone Assembly
Field Test Equipment Required
Reduced Pressure Zone Backflow Preventer Test Kit
Test No. 1
Purpose:
To test check valve No. 2 for tightness against re-
verse flow.
Requirements:
Valve must be tight against reverse flow under
all pressure differentials. Slowly open the
high
valve A and
the
vent
valve C, and keep the
low
valve B closed. Open test
cock #4. Indicated pressure differential will decrease slightly. If
pressure differential continues to decrease (until the vent opens)
check valve #2 is reported as
leaking
.
Test No. 2
Purpose:
To test shutoff #2 for tightness.
Requirements:
After passing Test No. 1, continue to Test No.
2 by closing test cock #2. The indicated pressure differential will
decrease slightly. If pressure differential continues to decrease
(approaching “zero”), shutoff #2 is reported to be “leaking”.
Test No. 3
Purpose:
To test Check Valve No. 1 for tightness.
Requirements:
Valve must be tight against reverse flow under
all pressure differentials. Close
high
valve A and open test cock
#2. Close test cock #4. Disconnect vent hose at test cock #4.
Open valves B and C, bleeding to atmosphere. Then closing
valve B restores the system to a normal static condition. Ob-
serve the pressure differential gauge. If there is a decrease in the
indicated value, Check Valve No. 1 is reported as “leaking”.
Test No. 4
Purpose:
To test operation of pressure differential relief valve.
Requirements:
The pressure differential relief valve must
operate to maintain the “zone” between the two check valves
at least 2 psi less than the supply pressure. Close
vent
valve
C. Open
high
valve A. Open the
low
valve B very slowly until
the differential gauge needle starts to drop. Hold the valve at
this position and observe the gauge reading at the moment the
first discharge is noted from the relief valve. Record this as the
opening differential pressure of the relief valve.
NOTICE
It is important that the differential gauge needle drops slowly.
Close test cocks #2 and #3. Use
vent
hose to relieve pressure
from test kit by opening valves A, B and C. Remove all test
equipment and open shutoff #2.
Ball Type
Test Valves
(A)
(C)
(B)
Needle
Valve
Auxiliary
Test Cock
High Hose
(Color - Yellow)
Low Hose
(Color - White or Red)
Vent Hose
(Color - Blue)
Test Cock
No. 1
Test Cock
No. 2
Test Cock
No. 3
Test Cock
No. 4
Shutoff
No. 1
Check Valve
No. 2
Shutoff
No. 2
Check Valve
No. 1
909QT shown
CAUTION
!
To prevent freezing, hold Test Kit vertically to drain
differential gauge and hoses prior to placing in case.
No. TK-9 Model “A” Test Kit