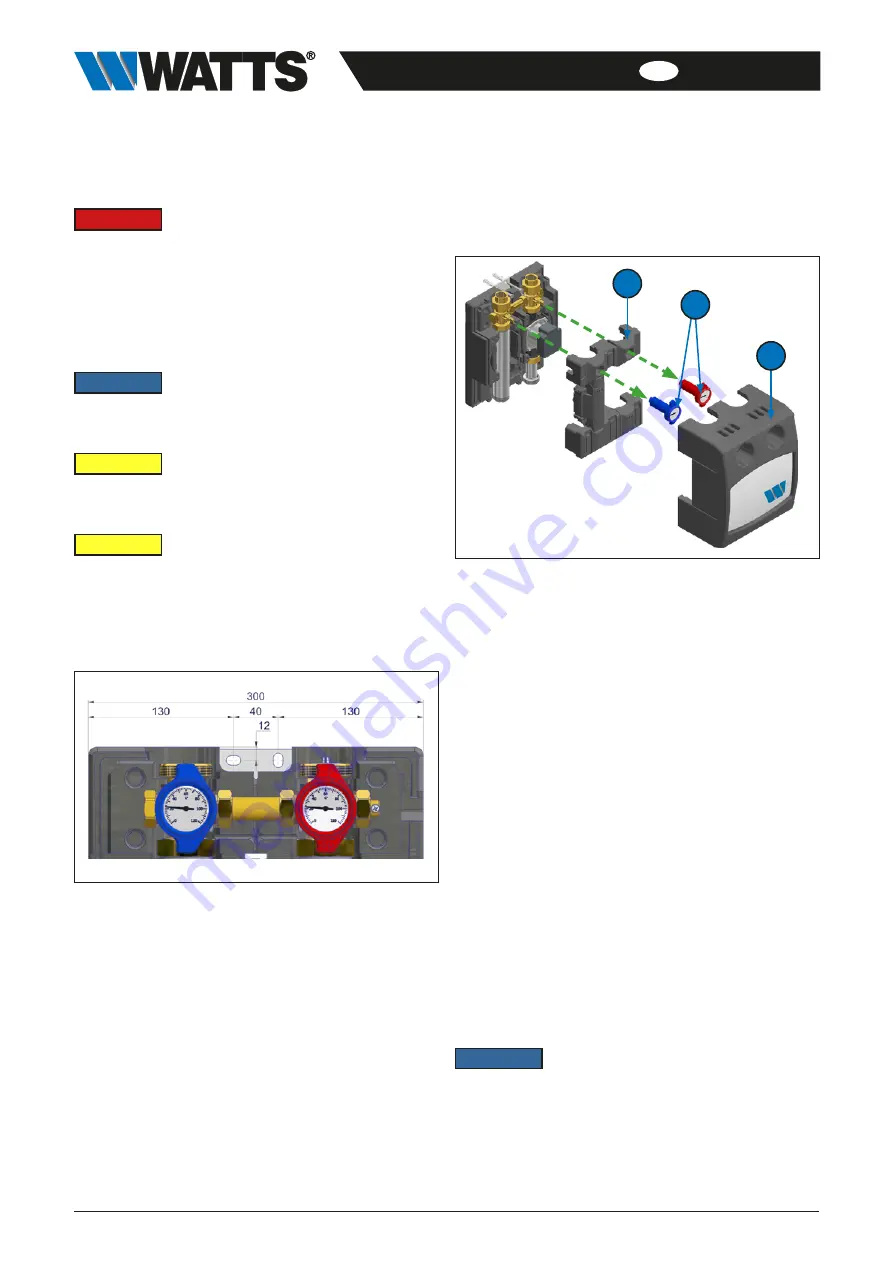
8
EN
ENGLISH
HK-HKM-25-32-IM-DE-W-UK-03-2021-Rev.3 | Part no. 10025988
7 Installation and commissioning
!
DANGER
Electrical energy!
Risk of death from electric shock.
• Work on parts carrying live voltage must be carried out by
qualified electricians only.
• Disconnect the power supply of the system and secure it to
prevent it from being switched on again before carrying out
any installation, maintenance, cleaning or repair work.
NOTICE
The installation and commissioning of
the pump group must be carried out only by trained person-
nel who have been authorized by the manufacturer.
!
!
CAUTION
When repairing the unit or replacing
parts, be sure to observe the specified installation positions
and flow directions of the parts being replaced!
!
!
CAUTION
Material damage!
Pressure shocks may occur if the stop valve is opened or
closed quickly.
• Always open and close the stop valves slowly and in a
controlled way.
7.1 Installation diagram
Fig. 7-1: Installation diagram
7.2 Installation
All screw fittings must be checked and tightened if
required prior to installation and commissioning!
Torque:
• 3/4" fittings 35 Nm
• 1" fittings 55 Nm
• 11/4" fittings 90 Nm
• 11/2" fittings 130 Nm
• 2" fittings 190 Nm
Requirement
• The valves are pre-installed at the factory but must be
checked for leaks during commissioning (pressure test).
1. Dismantle the front panel (A) of the pump group.
C
A
B
Fig. 7-2: Dismounting of the front and intermediate insulation
2. Mark the drilling points for installing pump group (see „Fig.
3. Drill the holes corresponding to the screw and anchor size
(see „Fig. 7-1: Installation diagram“).
4. Place the anchor.
5. Screw the screws into the anchor.
6. Place the pump group to the wall in a vertical installation
position (see „Fig. 7-1: Installation diagram“) .
7. Screw the screws into the anchor.
8. Remove the thermometer handles (B) and dismount the
intermediate insulation (C).
9. Connect the supply and return lines and check that all
screw connections are tight.
7.3 Initial commissioning
Requirement
• The pump group is completely assembled.
Connection of the power supply
1. Connect the power supply (see separate pump
documentation).
9
The pump group switches on automatically after being
connected to the power supply.
2. Vent the heating system.
NOTICE
The pump group must be switched off
during the ventilation process!
3. Mount intermediate insulation (C) and attach thermome-
ter grips (B).
4. Mount the front panel of the pump group.