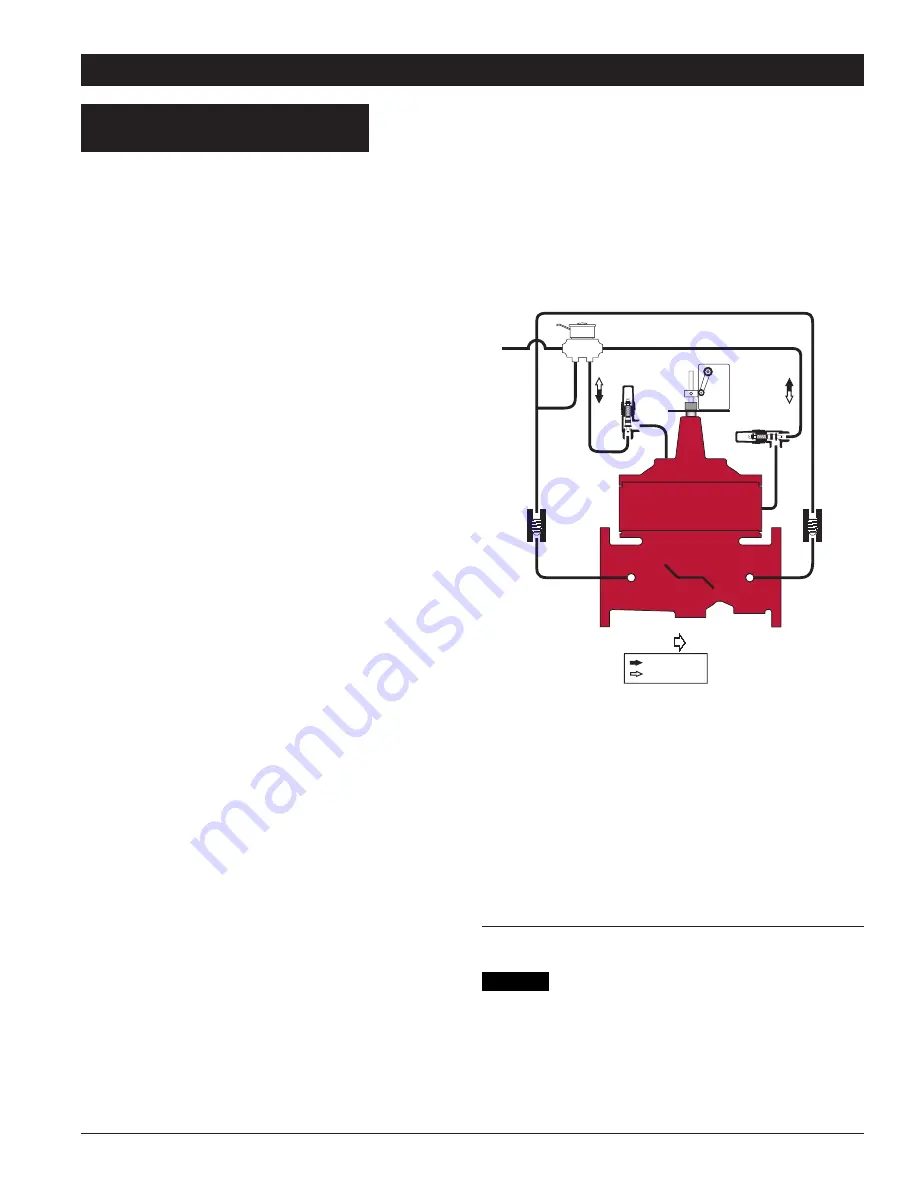
2
ES-A-ACV-LF980GD-16 2115
© 2021 Watts
Pump Control Valve with Mechanical Check Feature
Full Port Ductile Iron Dual Chamber Valve with Mechanical Check Feature
Features
• Opens at adjustable rate on pump start-up
• Closes at adjustable rate on pump shut-off
• Limit Switch turns pump off when valve closes
• Built-in Mechanical Lift-Check Feature prevents flow reversal
• Solenoid equipped with Manual Operator
1
X
3
6
3
2
X
X
Y/FC
Y/FC
4(L)
CLOSES VALVE
OPENS VALVE
FLOW
5
X
Standard Components
Options and Accessories
{
FC – Flo-Clean Strainer
{
L – Dual Limit Switch
Operation
1 – Main Valve (900GD-16 — Dual Chamber with Lift-Check)
2 – 4-Way Solenoid
3 – Check Valve
4 – Limit Switch
5 – Adjustable Opening Speed
6 – Adjustable Closing Speed
Y – Y-Strainer
X – Isolation Cocks
LEAD FREE
*
The information contained herein is not intended to replace the full
product installation and safety information available or the experi-
ence of a trained product installer. You are required to thoroughly
read all installation instructions and product safety information
before beginning the installation of this product.
NOTICE
* The wetted surface of this product contacted by consumable water
contains less than 0.25% of lead by weight.
The Pump Control Valve is designed to minimize the surges asso-
ciated with the starting and stopping of pumps. The valve slowly
opens and closes as required to control pumping related surges.
The pump starts and stops against a closed valve.
Pump start up:
When the pump is signaled to start, the 4-Way
Solenoid is energized and directs fluid and pressure into the power
chamber (below the diaphragm), and relieves fluid and pressure
from the cover chamber (above the diaphragm). The fluid and pres-
sure relieved from the cover chamber is vented to atmosphere or
available floor drain. The valve opens at an adjustable rate, gradu-
ally admitting pumping pressure into the distribution system. Rate
of valve opening is controlled by the adjustable opening speed
control, which restricts the speed at which fluid and pressure
evacuate the cover chamber. The valve remains fully open during
the pumping cycle.
Pump shutdown:
When the pump is signaled to shut-off, the
4-Way Solenoid is de-energized, and directs fluid and pressure into
the cover chamber (above the diaphragm), and relieves fluid and
pressure from the power chamber (below the diaphragm). The fluid
and pressure relieved from the power chamber is vented to atmo-
sphere or available floor drain. The valve closes at an adjustable
rate, gradually reducing pumping pressure. Rate of valve closure is
controlled by the adjustable closing speed control, which restricts
the speed at which fluid and pressure evacuate the power cham-
ber. When the valve reaches the closed position, the limit switch is
actuated, turning the pump off.
Emergency Closure:
The valve is equipped with a Mechanical
Check Feature, which acts independent of diaphragm position, and
provides immediate closure when flow ceases.
Manual Operation:
Engaging the Solenoid Manual operator
simulates power to the solenoid, manually opening the main valve.
Disengaging the Solenoid Manual operator returns the valve to the
closed position.
Series LF980GD-16