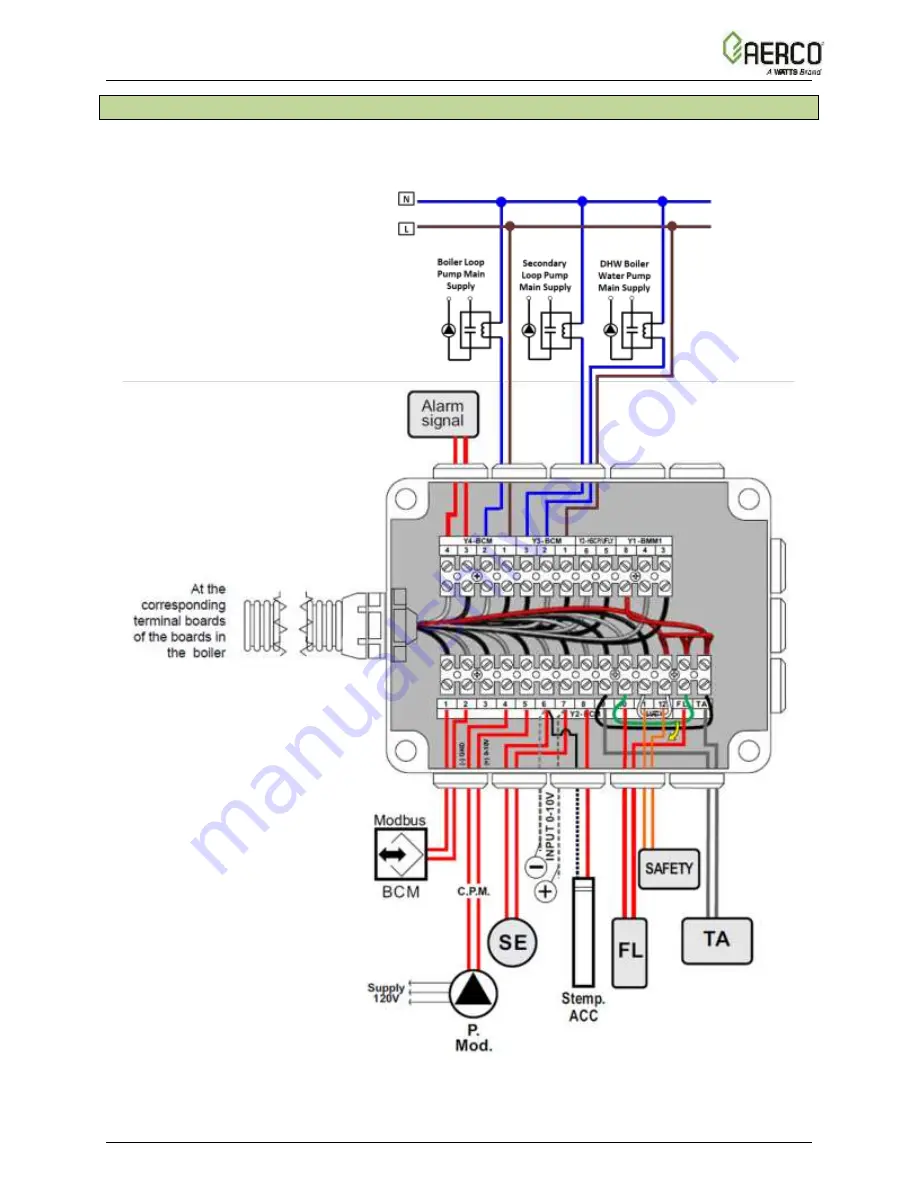
Modulex Light Commercial Series
CHAPTER 4: Installation Instructions
OMM-0158_A
• 6/28/2022 Technical Support • (800) 526-0288 • Mon-Fri, 8 am - 5 pm EST Page
56
of
120
4.31 Input/Output Box Terminal Assignments
Heating system components such as pump, outside air sensor and flow switch must be connected
to the Input/Output box. Alarm contact, analog control input (0--10V) and Modbus communication
are also connected to the Input/Output box. See figure 4-32 for terminal block assignments.
Figure 4-31: Ufly Controller Terminal Assignments