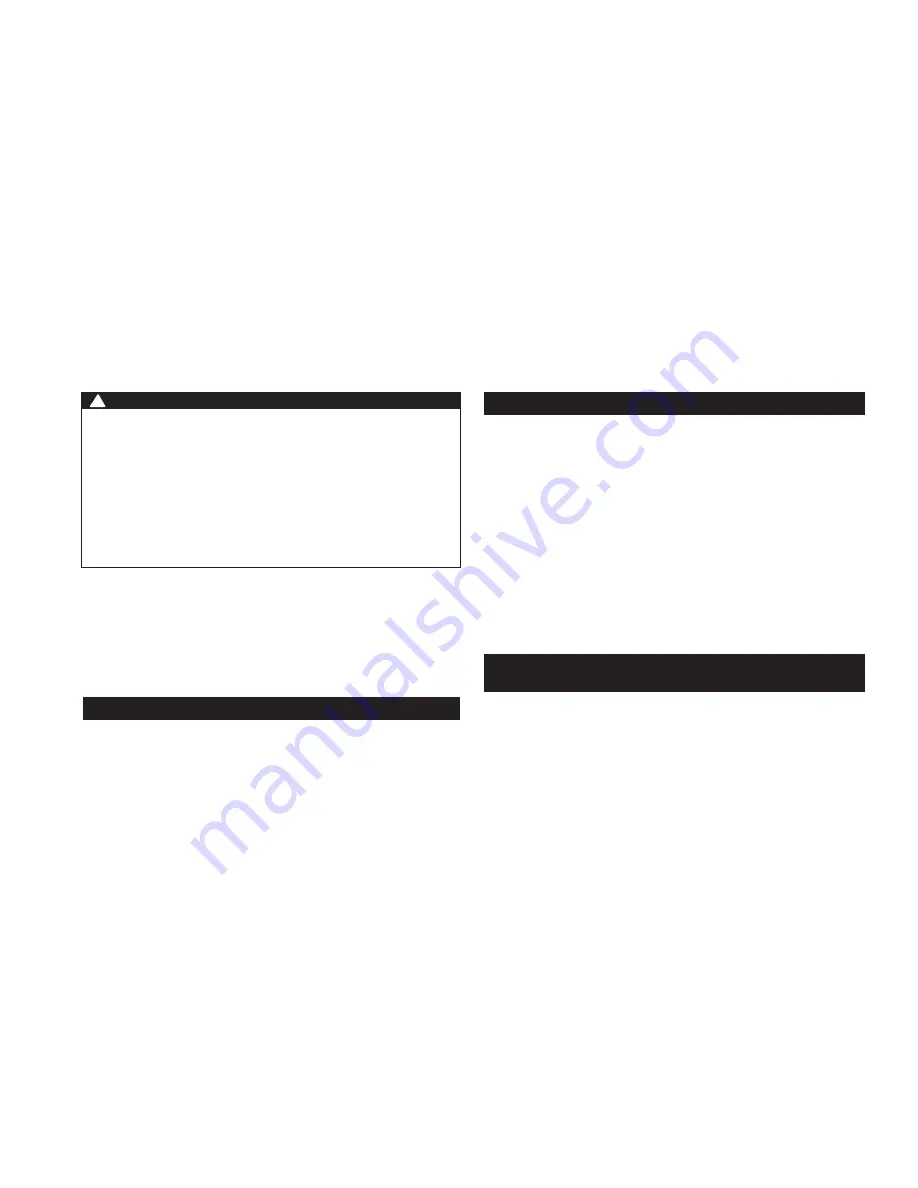
To ensure peak performance and longevity of your automatic
control valve, Watts/Ames recommends following the below
standard maintenance schedule.
•
Monthly Maintenance
– Visual inspection of valve(s) for leaks
– Inspect for proper operation(s); exercise valve.
•
Quarterly Maintenance
– Conduct monthly inspection.
– Validate/Re-establish necessary setpoints of controls/pilots.
•
Annual Maintenance
– Conduct monthly & quarterly inspections.
– Inspect & clean all strainers.
– Inspect valve coating, touch up as required.
•
3-5 Year Maintenance
– Conduct monthly, quarterly, & annual maintenance.
– Inspect & replace valve elastomers (diaphragm, O-rings,
valve/pilot seats)
– Re-establish necessary set points of controls/pilots.
Automatic Control Valve Maintenance Schedule
Troubleshooting Guide
Warning:
The valve cannot be serviced under pressure.
Upstream and downstream Isolation Valves must be installed
to protect system piping. Accurate diagnosis and trouble-
shooting requires the valve to open fully, and may subject
downstream piping and equipment to high pressure and/or
flow rates. The downstream Isolation Valve should be kept
closed while diagnosing the valve.
Extreme caution should be used while performing the
troubleshooting techniques listed below.
WARNING
!
Recommended tools for diagnosis: (3) PRESSURE GAUGES,
installed to monitor the inlet pressure, outlet pressure, and cover
chamber pressure. If included, a POSITION INDICATOR should
be installed to visually assess the position of the disc &
diaphragm assembly.
Test 1: Diaphragm Seal Test
1. Close upstream & downstream isolation valves. Close pilot
isolation valves or remove pilot control tubing to isolate valve
cover from incoming fluid & pressure. Remove uppermost
cover plug, test cock, or limit switch.
2. With the valve cover chamber vented to atmosphere,
partially open the upstream isolation valve, allowing incoming
pressure to lift the disc & diaphragm assembly. A volume of
water will be displaced from the cover chamber as the valve
opens; consult valve specification sheets for approximate
cover capacity. A continuous flow of water from the open port
indicates a damaged diaphragm or loose disc & diaphragm
assembly. Disassemble valve and replace diaphragm or tighten
disc & diaphragm assembly.
Test 2: Seat Seal Test
1. Close downstream isolation valve and install pressure gauges
on an open inlet and outlet port of main valve.
2. Open upstream isolation valve to allow pressure on to the
valve cover. Allow valve to fully close.
3. Monitor downstream pressure gauge; reading should hold
steady below incoming pressure. If pressure on downstream
side rises to match upstream pressure, leakage is occurring
through the seat of the main valve. Disassemble valve, inspect
and repair/replace any required parts.
a. If gauge pressure rises to match outlet pressure (down-
stream of closed isolation valve) yet remains below inlet
pressure, the isolation valve may be leaking as opposed to
main valve seat.
Test 3: Freedom of Movement/Valve
Travel Test
1. Close upstream and downstream isolation valves. Install valve
position indicator.
2. Partially open upstream isolation valve and allow cover to fill
with fluid & pressure, closing the valve fully. Mark the position
indicator’s full closed position.
3. Isolate cover chamber from receiving fluid and pressure by
closing isolation valves or removing control tubing.
4. Carefully vent cover chamber to atmosphere by opening test
cock or removing a cover plug. Observe the valve position
indicator as the valve travels to the full-open position. The disc
& diaphragm assembly should move freely from fully closed to
fully open position without binding or “grabbing” at any point
during its movement.
a. The disc & diaphragm assembly may momentarily “hesi-
tate” while travelling from fully closed to fully open position
– this is a normal characteristic of diaphragm operated
control valves, and does not indicate mechanical binding
or improper valve operation.
b. A continuous discharge of water from the cover chamber
after venting to atmosphere indicates leakage past the
diaphragm.
5. If necessary, disassemble valve and inspect/repair disc &
diaphragm assembly.
4 IOM-A-ACV-980-16-19_680-16-19 2115
EDP# 1917102
© 2021 Watts
IOM-A-ACV-980-16-19_680-16-19 2115
EDP# 1917102
© 2021 Watts 5