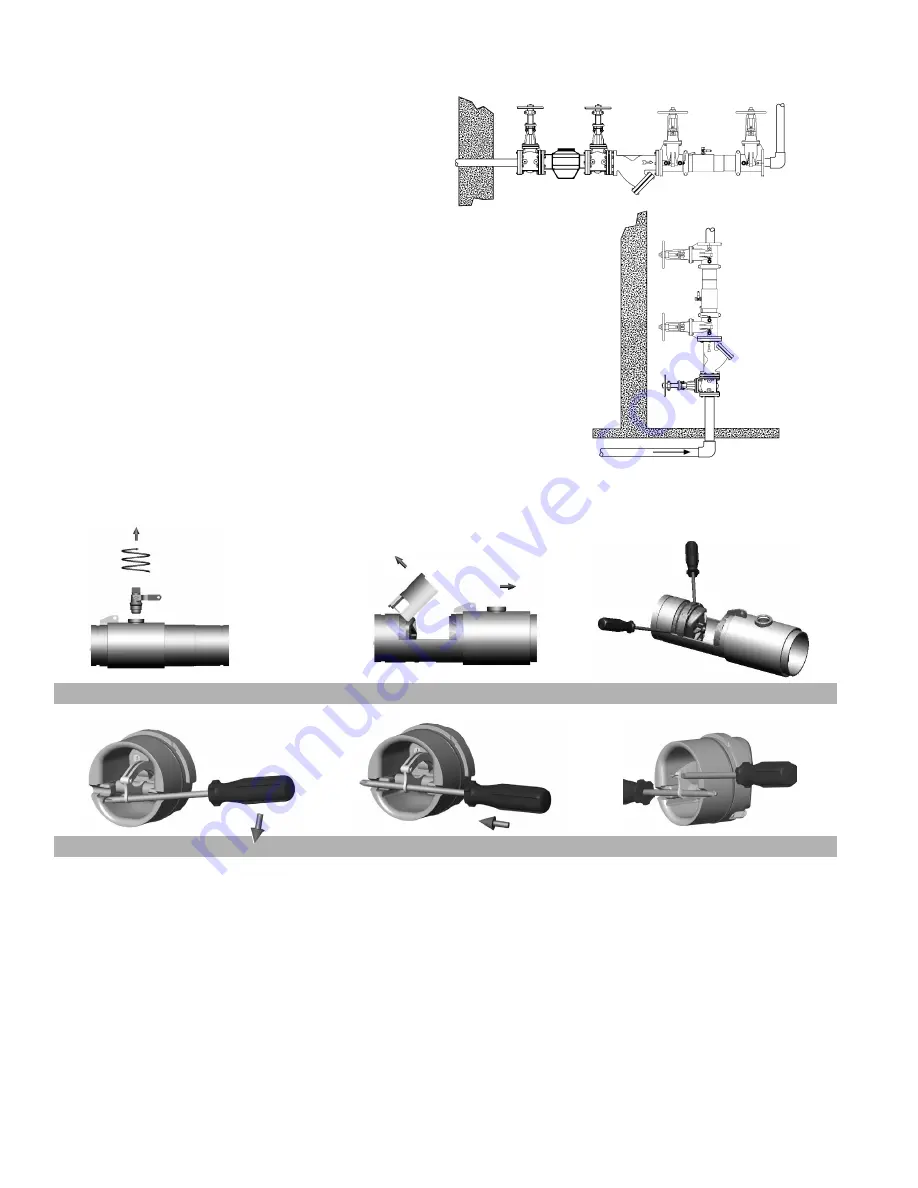
2
Guidelines
Most field problems occur because dirt and debris present in
the system at the time of installation becomes trapped in the
#1 check. The system should be flushed before the backflow
valve is installed. If the system is not flushed until after the
backflow valve is installed, remove both check modules from
the valve and open the inlet shutoff to allow water to flow for a
sufficient time to flush debris from the water line. If debris in the
water system continues to cause fouling, a strainer can be
installed upstream of the backflow assembly.
Watts models 757a and 757aDCDA may be installed in either
horizontal or vertical position as long as the backflow assembly
is installed in accordance with the direction of the flow arrow
on the assembly and the local water authority approves the
installation. The assembly should be installed with adequate
clearance around the valve to allow for inspection, testing and
servicing. 12" should be the minimum clearance between the
lower portion of the assembly and the floor or grade.
Horizontal Installation
Vertical Installation
Figure D
Figure E
Figure F
Figure A
Figure B
Figure C
Prior to servicing any Watts valve, it is mandatory to shut down
the water system by closing both the inlet and outlet shutoff
valves. After shutoff valves are closed, open test cock #2, #3
and #4 to relieve pressure within the backflow assembly.
1. After #3 test cock has been opened to relieve pressure,
remove #3 test cock from housing. (Figure A)
2. Slowly slide the cover sleeve to the downstream side of the
housing. (Figure B)
3. Remove the stainless steel check retainer from the housing.
(Figure B)
4. Remove the #1 check module (Figure C) by inserting two
flat blade screwdrivers into the slots on either side of the
check module and gently pry to check module toward the
open zone.
5. Remove #2 check module with the same instructions as in
#4 above.
6. To clean or inspect either check module, insert a #3 screw-
driver through the downstream side of the check module as
shown in Figure D and E. When the screwdriver is in place,
remove the E-clip (Figure F) and pin connecting the structur-
al members and the check clapper will open with no tension.
7. Thoroughly clean the seating area. The sealing disk may be
removed, if necessary, by removing the screws connecting
the keeper plate to the clapper. The sealing disc may be
reversed and reinstalled if the elastomer is cut or damaged.
8. Wash check module and O-ring and inspect for any dam-
age. If damaged, reinstall new parts.
9. After thorough cleaning, lubricate O-ring w/FDA approved
lubricant, replace pin and E-clip in structural members,
remove screw driver and reinstall check modules and
assemble housing in reverse order of these instructions.
Maintenance Instructions
Basic Installation Instructions