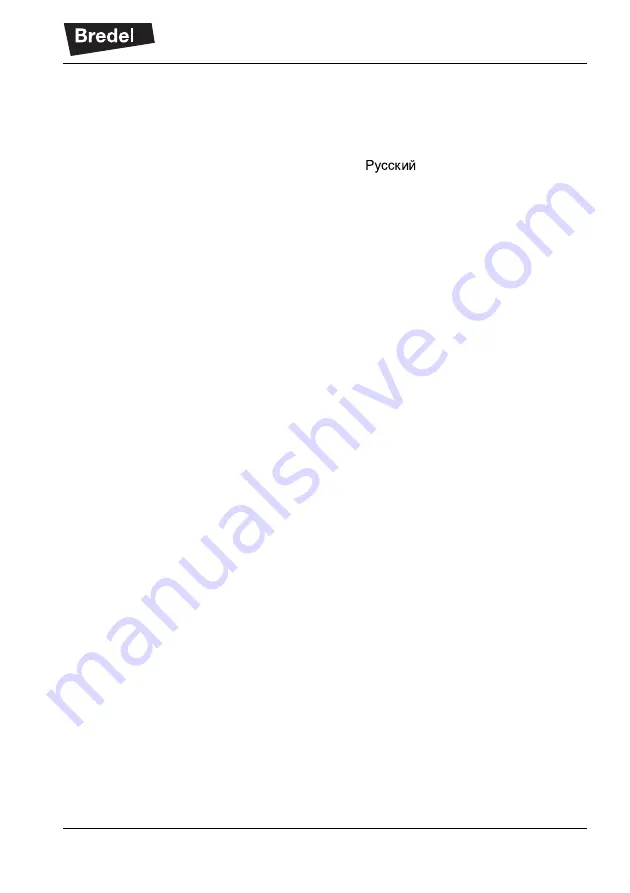
1
Disc
The disc, which is inserted in the cover, contains the user manual(s) of the Bredel 265,
Bredel 280 and Bredel 2100 hose pumps in the following languages:
The disc also contains quick-reference instructions for the replacement of the pump
hose. This replacement instruction is only for users that are familiar with the
replacement procedures in the user manual.
How to use the disc
1
Put the disc in the disc drive.
2
Close the disc drive.
The disc will start automatically.
3
Wait until the various language versions appear on screen.
4
Select the required language (click 1x with the left mouse button).
The PDF reader program will automatically start and the required user manual
appears on screen.
Shortcuts
In the left margin you will find the various chapters and paragraphs. These can be
accessed directly by clicking on the required chapter or paragraph.
In the text you will find hyperlinks to chapters or paragraphs. These hyperlinks are linked
with the required chapters or paragraphs. By clicking a shortcut the required chapter or
paragraph appears on screen.
System requirements
The program on the disc requires a PC with the following minimum system
requirements:
•
Disc drive
The following software must be installed on the PC:
•
PDF reader program
•
an Internet browser
Français
English (US)
Español
English (UK)
Polski
Portiguês
Nederlands
Svenska
Suomi
Summary of Contents for Bredel 2100
Page 2: ...2...
Page 95: ...NOTES 95 Notes NOTES...