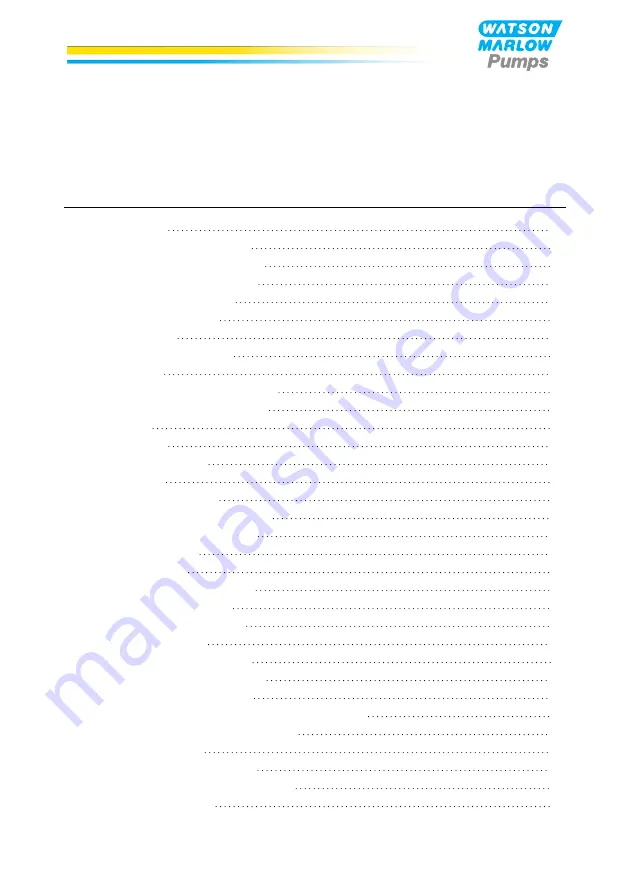
730 EnN Installation, operating, and maintenance manual
m-730en-en-09 02-02-22
1
Contents
1.2 Declaration of incorporation
3 Information for returning pumps
4 Peristaltic pumps - an overview
8 Good pump installation practice
10 Connecting to a power supply
10.2 Wiring the NEMA module - EtherNet/IP™ pumps
10.3 M12 connector screen connection
12 EtherNet/IP™ control wiring