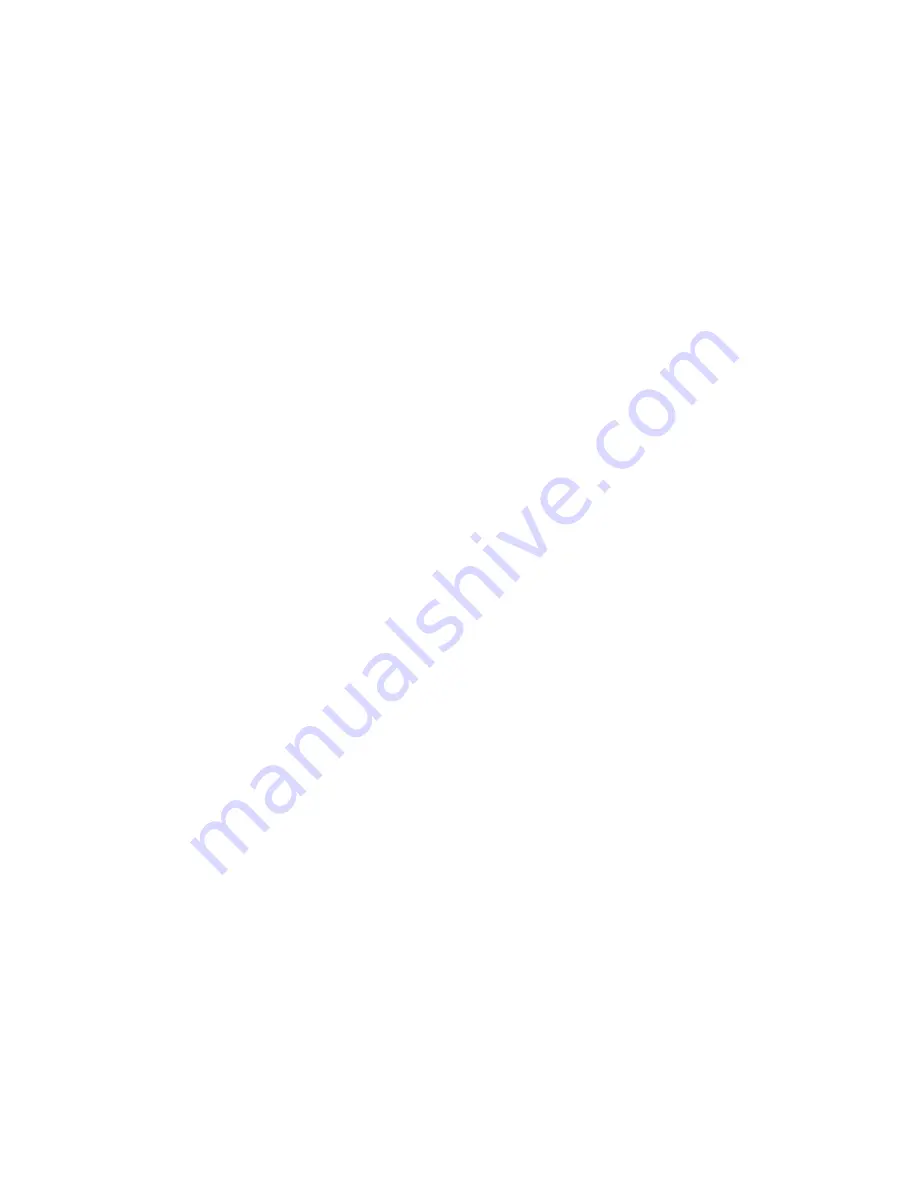
Watson Industries, Inc.
DMS-EGP02 Rev A 03/28/2008
3
CAUTION!
Watson Sensors are rugged devices that have been used successfully in a number of harsh
environments. The components have been qualified to withstand a mechanical shock of 200g 's or
greater, and most enclosures provide an added level of protection. However, dropping a sensor
from waist height onto a hard floor can cause a shock level of 600g's. At this level, damage is
likely to occur.
Introduction
The Dynamic Measurement System (DMS) is a solid-state sensor that provides the user with
dynamic measurements of angular attitude and angular rate, together with linear acceleration, in
three (3) mutually perpendicular planes (see Figure 2). A unique feature is the two sets of
acceleration measurements. One set gives sensor acceleration with respect to the sensor mounting
face while the other set resolves the motion into horizontal and vertical components, irrespective of
the sensor attitude. This allows the earth's gravitational field to be isolated from the measurement
of sensor motion. This System consists of a DMS unit & two GPS antennas.
Product Description
Watson Industries DMS uses solid-state gyros and silicon accelerometers. Interface to the
microprocessor is done through a 16-bit A/D converter. The solid state vibrating structure angular
rate gyros used in this system provide extremely high reliability, low power consumption, shock
resistance and low cost. There are no physical adjustments required by the user. All of the primary
transducers are locked into position during manufacture. Adjustments are made with the aid of PC-
based maintenance software, which communicates with the DMS via the RS-232 serial connection.
Calibration is achieved by using the maintenance software to store data in non-volatile memory
within the DMS. The DMS-EGP02 differs from a “standard” DMS with the addition of a Dual
antenna GPS system. This allows the DMS to output actual heading instead of relative heading.
The GPS receiver also provides a vehicle velocity which is used to improve accuracy in high
dynamic environments.
This unit has two modes. A toggle switch on the front of the DMS changes the unit between modes.
The first mode, with the switch in the up position, the unit operates like a standard DMS. (See
Figure 1). The unit does not use the GPS module, it outputs relative heading, has the ability to take
in commands (double space bar mode) and the vehicle speed is an analog input. The heading needs
to be in the relative mode & velocity input needs to be in the Analog input mode. (See Appendix A
Setting Velocity & Heading Modes)
In the second mode, the DMS uses the GPS module. The switch is in the down position. (See
Figure 1). In this mode, the unit outputs actual heading, does not take in commands and the vehicle
speed is digital. Please note that the Baud Rate needs to be set to 9600 when using the GPS
module (any selectable baud rate is acceptable when the GPS module is not in use). The heading
needs to be in the GPS True North mode and velocity input needs to be in the GPS Ground Track
mode. (See Appendix A Setting Velocity & Heading Modes)
A vehicle speed input is used to assist in the correction of errors. It is also included in the
parameter set that is available for serial output. Although its use is not always required, it is highly
recommended that this signal be supplied to the DMS. The unit requires an analog/digital signal.
The analog signal is scaled to 40 KPH per volt. The digital signal is from the GPS module.
Forward motion should produce a positive signal with respect to signal ground. Many other