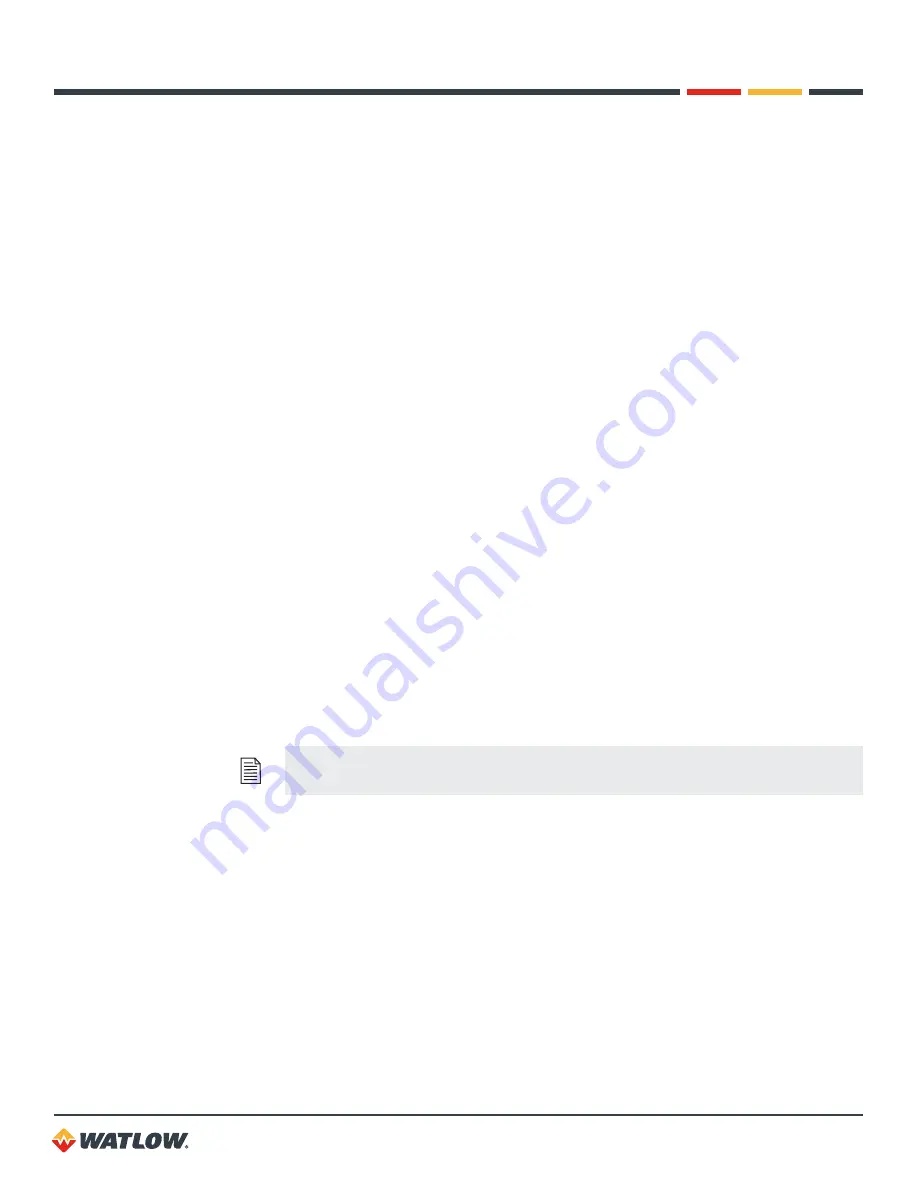
131
Chapter 7:
Turning and Control
This chapter describes the different methods of control available with the CLS200. This chapter
covers control algorithms, control methods, PID control, starting PID values and tuning instructions
to help appropriately set control parameters in the CLS200 system. For more information on PID
control, consult the
Watlow Practical Guide to PID
.
Control Algorithms
This section explains the algorithms available for controlling a loop.
The control algorithm dictates how the controller responds to an input signal. Do not confuse control
algorithms with control output signals (for example, analog or pulsed dc voltage). There are several
control algorithms available:
• On/off
• Proportional (P)
• Proportional and integral (PI)
• Proportional with derivative (PD)
• Proportional with integral and derivative (PID)
P, PI or PID control is necessary when process variable cycling is unacceptable or if the load or
setpoint varies.
NOTE!
For any of these control statuses to function, the loop must be in automatic
mode.
On/Off Control
On/off control is the simplest way to control a process. The controller turns an output on or off when
the process variable reaches limits around the desired setpoint. This limit is adjustable; Watlow
controllers use an adjustable spread.
For example, if the setpoint is 1,000°F and the spread is 20°F, the heat output switches on when the
process variable drops below 980°F and off when the process rises above 1,000°F. A process using
on/off control cycles around the setpoint.
Figure 7.1
illustrates this example.