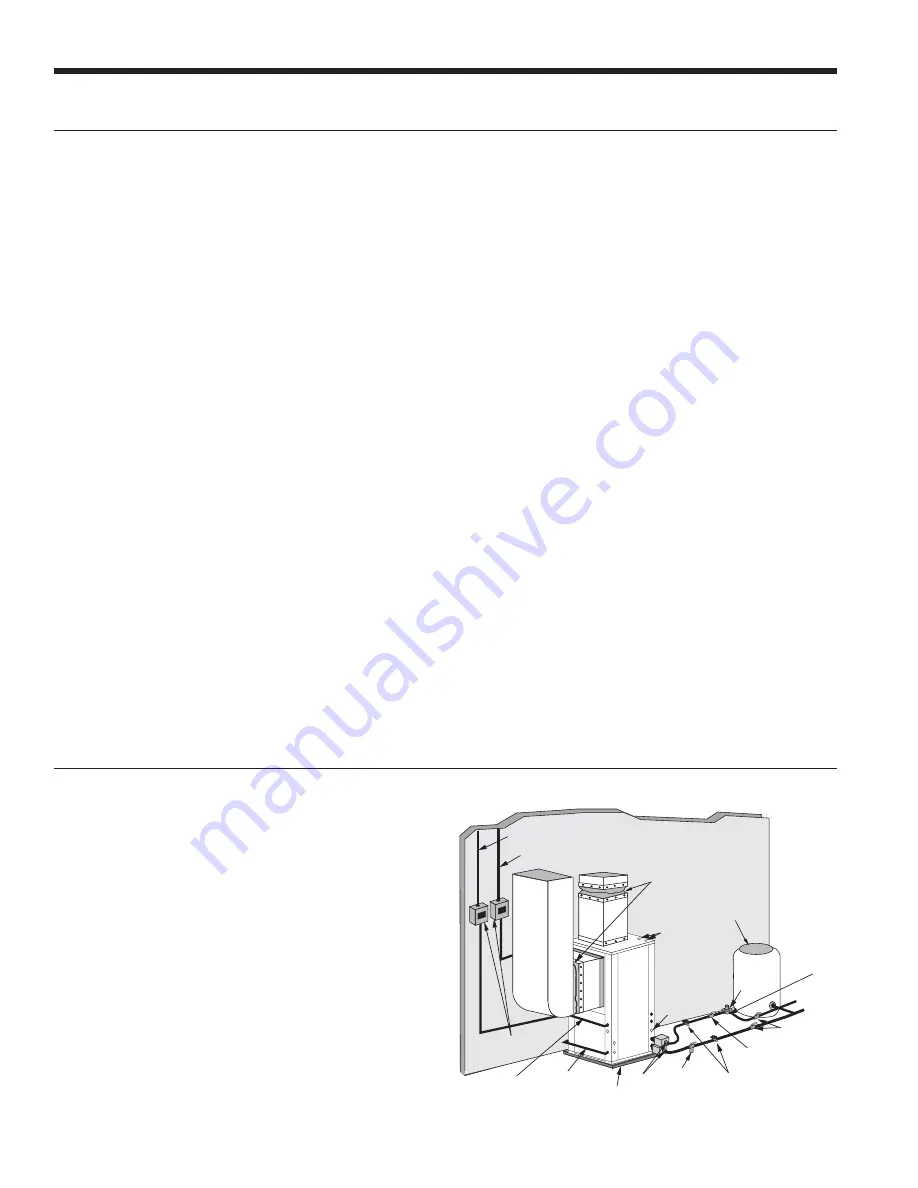
14
ENVISION
2
COMPACT - 50 HZ INSTALLATION MANUAL
Typical open loop piping is shown below. Always maintain
water pressure in the heat exchanger by placing water
control valves at the outlet of the unit to prevent mineral
precipitation. Use a closed, bladder-type expansion tank
to minimize mineral formation due to air exposure. Insure
proper water flow through the unit by checking pressure
drop across the heat exchanger and comparing it to the
figures in unit capacity data tables in the specification
catalog. 0.09-0.13 L/s of flow per ton of cooling capacity is
recommended in open loop applications. Due to only minor
differences in flow rate from low to high, only one solenoid
valve should be used. The valve should be sized for full flow.
Discharge water from the unit is not contaminated in any
manner and can be disposed of in various ways, depending
on local codes, i.e. recharge well, storm sewer, drain field,
adjacent stream or pond, etc. Most local codes forbid the use
of sanitary sewer for disposal. Consult your local building and
zoning departments to assure compliance in your area.
Open System - Groundwater Application
Flexible
Duct Collar
Vibration
Absorbing Pad
P/T Plugs
Drain
Hot Water Generator
Connections
Low Voltage
to Thermostat
and Valve
Unit Supply
Aux. Heat Supply
Water Out
Water In
Shut Off Valves
Boiler Drains
For HX Flushing
Disconnects
(If Applicable)
Rubber Bladder
Expansion Tank
Solenoid
Valve
Shut Off Valves
(to isolate solenoid
valve while acid flushing)
Strainer
Flow Control
Valve
(on outlet of
Solenoid Valve)
Compressor
Line Voltage
Open Loop Ground Water Systems
System Cleaning and Flushing cont.
be opened for initial flush and blowdown, making sure
water fill valves are set at the same rate. Check the pressure
gauge at the pump suction and manually adjust the make-
up water valve to hold the same positive pressure both
before and after opening the drain valves. Flushing should
continue for at least two hours, or longer if required, until
drain water is clean and clear.
The supplemental heater and/or circulator pump, if used,
should be shut off. All drains and vents should be opened
to completely drain the system. Short-circuited supply and
return runouts should now be connected to the unit supply
and return connections.
Refill the system with clean water. Test the system water
for acidity and treat as required to leave the water slightly
alkaline (pH 7.5 to 8.5). The specified percentage of
antifreeze may also be added at this time. Use commercial
grade antifreeze designed for HVAC systems only.
Environol™ brand antifreeze is recommended.
Once the system has been filled with clean water and
antifreeze (if used), precautions should be taken to protect
the system from dirty water conditions. Dirty water will
result in system-wide degradation of performance, and
solids may clog valves, strainers, flow regulators, etc.
Additionally, the heat exchanger may become clogged
which reduces compressor service life and can cause
premature unit failure.
In boiler/tower application, set the loop control panel
set points to desired temperatures. Supply power to all
motors and start the circulating pumps. After full flow has
been established through all components including the
heat rejector (regardless of season), air vented and loop
temperatures stabilized, each of the units will be ready for
check, test and start up and for air and water balancing.
Ground Source Loop System Checkout
Once piping is completed between the unit pumping
system and ground loop, final purging and charging of
the loop is needed. A high pressure pump is needed to
achieve adequate flow velocity in the loop to purge air
and dirt particles from the loop itself. Antifreeze solution
is used in most areas to prevent freezing. Flush the
system adequately to remove as much air as possible;
then pressurize the loop to a static pressure of 276-345
kPa (summer) or 345-517 kPa (winter). This is normally
adequate for good system operation. Loop static pressure
may decrease soon after initial installation, due to pipe
expansion and loop temperature change. Running the
unit for at least 30 minutes after the system has been
completely purged of air will allow for the “break-in”
period. It may be necessary to adjust static loop pressure
(by adding water) after the unit has run for the first time.
Loop static pressure will also fluctuate with the seasons.
Pressures will be higher in the winter months than during
the cooling season. This fluctuation is normal and should be
considered when charging the system initially.
Ensure the pump provides adequate flow through the unit
by checking pressure drop across the heat exchanger.
Usually 0.14-0.19 L/s of flow per ton of cooling capacity is
recommended in earth loop applications.
Summary of Contents for Envision2 Compact
Page 2: ......