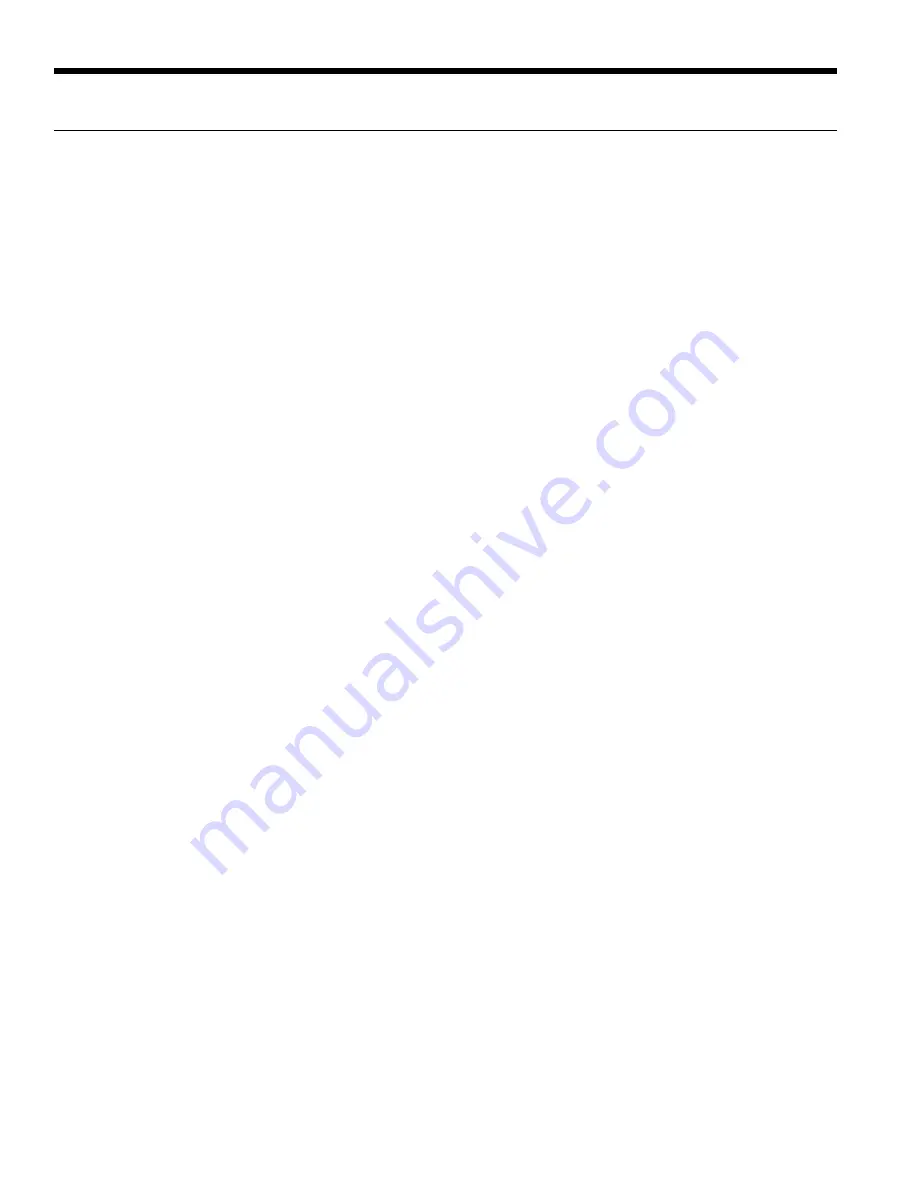
18
NSZ/NDZ INSTALLATION MANUAL
Startup
The unit will not operate until all the inputs and safety
controls are checked for normal conditions. At first power-
up, a four-minute delay is employed before the compressor
is energized.
Component Sequencing Delays
Components are sequenced and delayed for optimum
space conditioning performance.
Accessory Relay
An accessory relay on the control board allows for field
connection of solenoid valves, electronic air cleaners, etc.
The accessory relay has a normally open output and a
normally closed output.
Short Cycle Protection
The control employs a minimum "off" time of four minutes
to provide for short cycle protection of the compressor.
Shutdown Mode
A 24VAC common signal to the “shutdown” input on
the control board puts the unit into shutdown mode.
Compressor, hot water pump and blower operation are
suspended.
Safety Controls
The Envision control receives separate signals for a high
pressure switch for safety, a low pressure switch to prevent
loss of charge damage, and a low suction temperature
thermistor for freeze detection. Upon a continuous
30-second measurement of the fault (immediate for
high pressure), compressor operation is suspended, the
appropriate lockout LED begins flashing. (Refer to the
"Fault Retry" section below.)
Testing
The Envision control allows service personnel to shorten
most timing delays for faster diagnostics. (Refer to the
Field Selection DIP switch SW2-1.)
Fault Retry
All faults are retried twice before finally locking the unit
out. An output signal is made available for a fault LED at
the thermostat. The “fault retry” feature is designed to
prevent nuisance service calls.
Diagnostics
The Envision control board allows all inputs and outputs to
be displayed on the LEDs for fast and simple control board
diagnosis. (Refer to the Field Selection DIP Switch SW2-1.)
Hot Water High Limit
(Domestic Hot Water Option)
This mode occurs when the hot water input temperature
is at or above 130°F for 30 continuous seconds. The DHW
limit status LED on the unit illuminates and the hot water
pump de-energizes. Hot water pump operations resume on
the next compressor cycle or after 15 minutes of continuous
compressor operation during the current thermostat
demand cycle.
Hot Water Justification
Since compressor hot gas temperature is dependant on
loop temperature in cooling mode, loop temperatures may
be too low to allow proper heating of water. The control will
monitor water and refrigerant temperatures to determine if
conditions are satisfactory for heating water. The DHW limit
status LED on the unit illuminates when conditions are not
favorable for heating water.
Heating Operation
Heat, 1st Stage (Y1)
The blower motor is started immediately, the loop pump
is energized 5 seconds after the “Y1” input is received, and
the compressor is energized on low capacity 10 seconds
after the “Y1” input. The hot water pump is cycled 30
seconds after the “Y1” input.
Heat, 2nd Stage (Y1,Y2) Single-Speed Units
The hot water pump is de-energized, which directs all heat
to satisfying the thermostat, and the blower changes to
high speed 15 seconds after the “Y2” input (ECM only).
Heat, 2nd Stage (Y1,Y2) Dual Capacity Units
The second stage compressor will be activated 5 seconds
after receiving a “Y2” input as long as the minimum first
stage compressor run time of 1 minute has expired. The
ECM blower changes from medium to high speed 15
seconds after the “Y2” input.
The Comfort Alert will delay the second stage compressor
until 5 seconds after it receives a “Y2” from the board.
Microprocessor Control