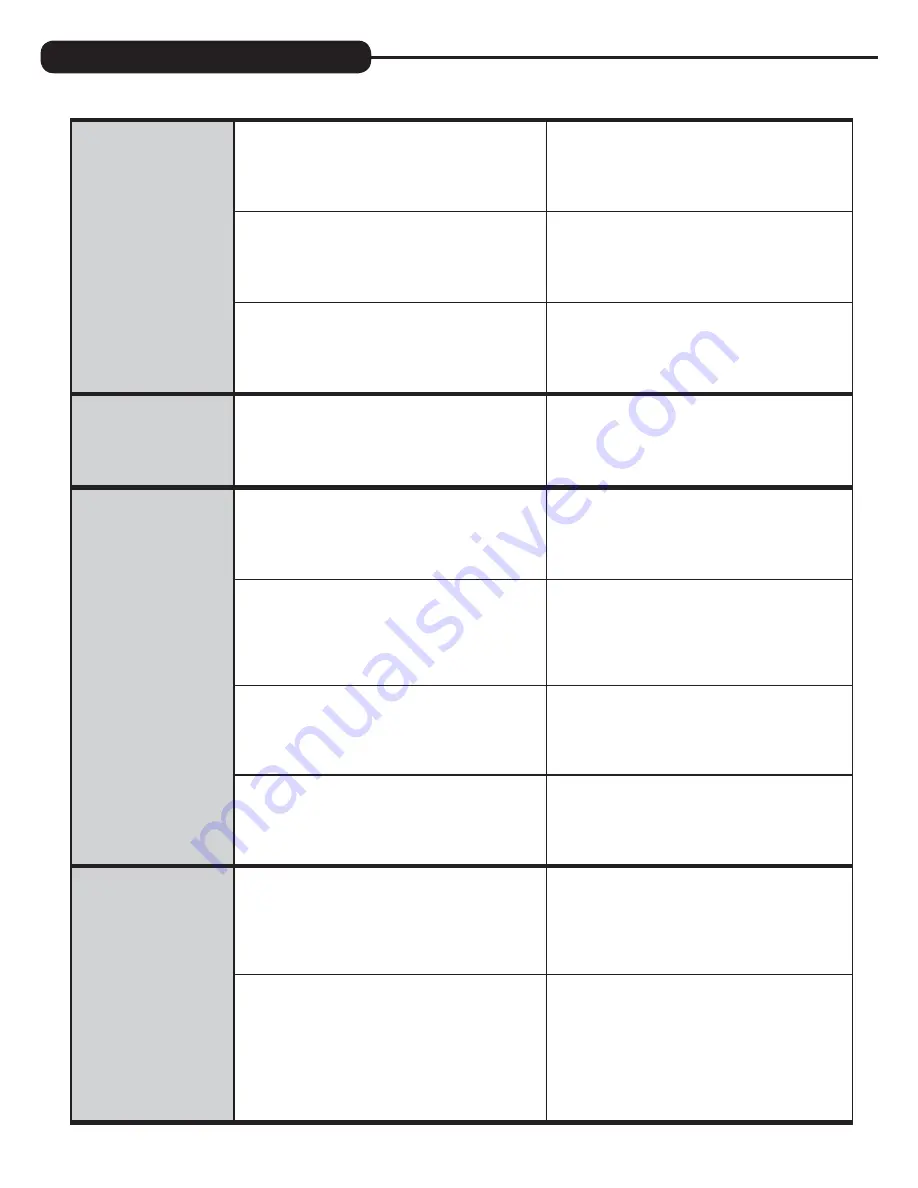
16
16. E3, Err – 1003, Err –
103 = Control valve
motor ran too long and
was unable to find the
next cycle position
A . Motor failure during a regeneration
A . Check motor connections then Press NEXT and
REGEN buttons for 3 seconds to resynchronize
software with piston position or disconnect
power supply from PC board for 5 seconds
and then reconnect .
B . Foreign matter built up on piston and stack
assemblies creating friction and drag enough
to time out motor
B . Replace piston and stack assemblies . Press
NEXT and REGEN buttons for 3 seconds to
resynchronize software with piston position
or disconnect power supply from PC board
for 5 seconds and then reconnect .
C . Drive bracket not snapped in properly and out
enough that reduction gears and drive gear do
not interface
C . Snap drive bracket in properly then Press
NEXT and REGEN buttons for 3 seconds to
resynchronize software with piston position
or disconnect power supply from PC board
for 5 seconds and then reconnect .
17. E4, Err – 1004, Err –
104 = Control valve
motor ran too long
and timed out trying
to reach home position
A . Drive bracket not snapped in properly and out
enough that reduction gears and drive gear do
not interface
A . Snap drive bracket in properly then Press
NEXT and REGEN buttons for 3 seconds to
resynchronize software with piston position
or disconnect power supply from PC board
for 5 seconds and then reconnect .
18. Err – 1006, Err – 106,
Err – 116 = MAV/
SEPS/ NHBP/ AUX
MAV valve motor ran
too long and unable
to find the proper
park position
Motorized Alternating
Valve = MAV
Separate Source = SEPS
No Hard Water Bypass
= NHBP
Auxiliary MAV = AUX
MAV
A . Control valve programmed for ALT A or B,
nHbP, SEPS, or AUX MAV with out having
a MAV or NHBP valve attached to operate
that function
A . Press NEXT and REGEN buttons for 3 seconds
to resynchronize software with piston position
or disconnect power supply from PC board for
5 seconds and then reconnect . Then reprogram
valve to proper setting
B . MAV/NHBP motor wire not connected to
PC board
B . Connect MAV/NHBP motor to PC board two
pin connection labeled DRIVE . Press NEXT and
REGEN buttons for 3 seconds to resynchronize
software with piston position or disconnect
power supply from PC board for 5 seconds
and then reconnect .
C . MAV/NHBP motor not fully engaged with
reduction gears
C . Properly insert motor into casing, do not force
into casing Press NEXT and REGEN buttons for
3 seconds to resynchronize software with piston
position or disconnect power supply from PC
board for 5 seconds and then reconnect .
D . Foreign matter built up on piston and stack
assemblies creating friction and drag enough
to time out motor
D . Replace piston and stack assemblies . Press
NEXT and REGEN buttons for 3 seconds to
resynchronize software with piston position
or disconnect power supply from PC board
for 5 seconds and then reconnect .
19. Err – 1007, Err – 107,
Err – 117 = MAV/
SEPS/NHBP/AUX
MAV valve motor
ran too short (stalled)
while looking for
proper park position
Motorized Alternating
Valve = MAV
Separate Source = SEPS
No Hard Water Bypass
= NHBP
Auxiliary MAV = AUX
MAV
A . Foreign material is lodged in
MAV/NHBP valve
A . Open up MAV/NHBP valve and check piston
and seal/ stack assembly for foreign material .
Press NEXT and REGEN buttons for 3 seconds
to resynchronize software with piston position
or disconnect power supply from PC board for
5 seconds and then reconnect .
B . Mechanical binding
B . Check piston and seal/stack assembly, check
reduction gears, drive gear interface, and
check MAV/NHBP black drive pinion on
motor for being jammed into motor body .
Press NEXT and REGEN buttons for 3 seconds
to resynchronize software with piston position
or disconnect power supply from PC board for
5 seconds and then reconnect .
PROBLEM
CAUSE
CORRECTION
TROUBLESHOOTING GUIDE
Summary of Contents for Impression Plus Series
Page 22: ...22 REPLACEMENT PARTS...