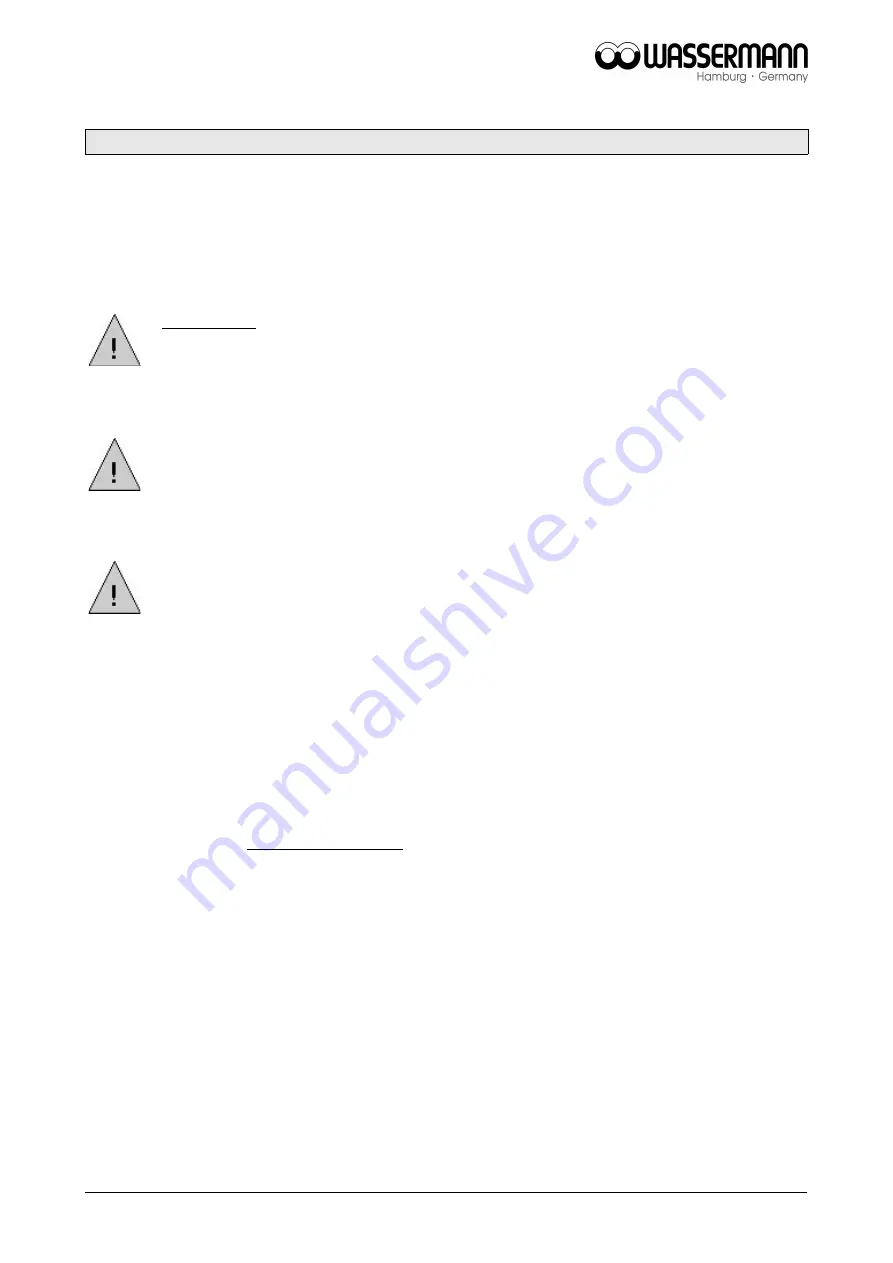
3 Safety guidelines
Configuring and operating this equipment requires
precise knowledge
and
observance
of the instructions in this
user manual
. The equipment is designed only for its intended
application.
WARNING:
Servicing and repairs should be carried out only by authorised specialists.
Disconnect the power plug before starting any maintenance work.
Make sure that the equipment is connected to the correct power source.
The safety valve on the pressure vessel opens automatically if the operating
pressure exceeds 7 bar.
The pressure is switched on only after the door is fully closed, thanks to a safety
contact and an orange monitor light.
Dry-run protection switches off at 112°C (brown knob, left side of unit)
Warning:
Scalding risk with hot polymerisation.
Open the lid slowly!
5
Summary of Contents for Polyquick
Page 1: ...Polymerisation Unit Polyquick USER MANUAL...
Page 20: ......