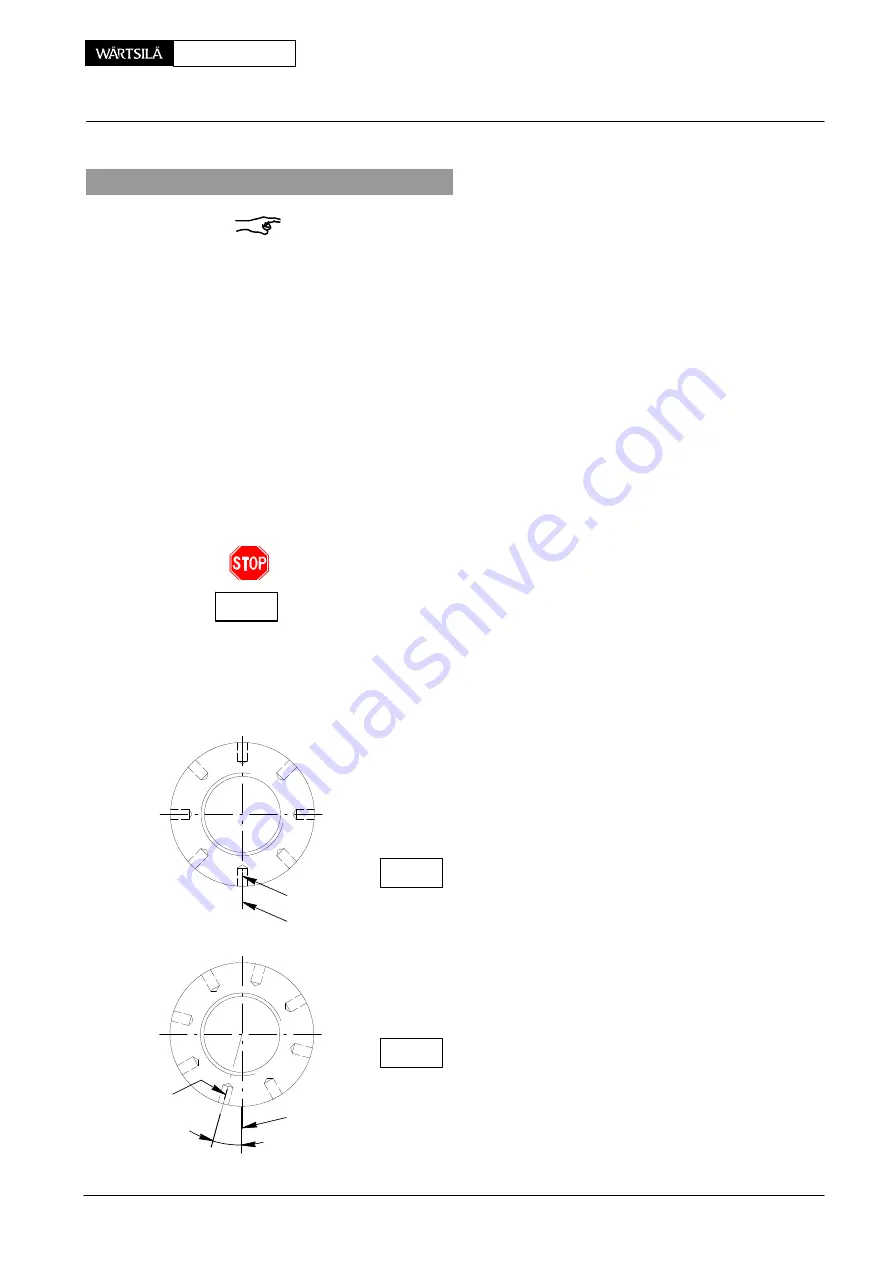
Maintenance
3303−1/A1
RT-flex50-D
Wärtsilä Switzerland Ltd
5.
Tensioning the stud of top end bearing
Remark: For tensioning the studs always follow the sequence shown in Fig. ’D’
i.e. a + a and b + b for each step.
⇒
Clean the threads of studs 1 as well as the area around nuts 2.
⇒
Apply oil to the stud threads and screw on the nuts.
⇒
Tighten the nuts with round bar ’RS’ and equally distribute clearance ’y’ be-
tween the bearing halves (bearing protrusion) as shown in Fig. ’D’.
⇒
Open vent screw 7.
⇒
Place pre-tensioning jacks 94315 diagonally onto studs as shown in Fig. ’D’,
and completely screw them on until there is only little or no clearance at ’x’
(Fig. ’F’).
⇒
Connect the pre-tensioning jacks to hydraulic unit 94942 as shown in Fig. ’D’.
⇒
Actuate the hydraulic unit till bubble-free oil flows out through the vent screws.
Close vent screws.
⇒
Actuate the hydraulic unit and set pressure to 1000 bar (1
st
step) and keep
pressure constant.
Pistons 8 of the pre-tensioning jacks must never exceed the red limiting grooves
’BN’ (Fig. ’F’).
Tighten the nuts with round bar ’RS’ and check with the feeler gauge through slot
’KO’ (Fig. ’F’) that no clearance remains between nut and supporting surface.
Check with the feeler gauge that no clearance remains between bearing cover and
connecting rod.
(Should clearance remain, loosen the fastening and compare the bearing protru-
sion with the nominal value as indicated in
⇒
Proceed in the same manner for the second pair of
the connecting rod studs.
⇒
After tensioning to the 1
st
step mark the position of
the nuts against bearing cover as shown in Fig. ’a’.
⇒
Raise the pressure to 1500 bar (2
nd
step) and keep
constant.
Tighten nuts down and check correct seating with the
feeler gauge.
Check from the markings applied by how much the nuts
were turned after pre-tightening (1
st
step).
Tightening angle to be about 15
_
(Fig. ’b’).
Should considerable differences to these nominal val-
ues be encountered then repeat the tensioning process.
⇒
Release pressure to ’0’ at the hydraulic unit and re-
move pre-tensioning jacks.
Finally check the vertical bearing clearance (see Clear-
ance Table
’Top and bottom end bearings to con-
necting rod’).
CHECK
CHECK
TIGHTENING
ANGLE
Fig. ’a’
Fig. ’b’
x
013.432/05
y
x
009.758/02
y
Loosening and Tensioning the Connecting Rod Studs
2010
CHECK
Summary of Contents for RT-flex50-D
Page 2: ...This page is intentionally left blank...
Page 4: ...This page is intentionally left blank...
Page 6: ...This page is intentionally left blank...
Page 8: ...This page is intentionally left blank...
Page 10: ...This page is intentionally left blank...
Page 16: ...This page is intentionally left blank...
Page 20: ...This page is intentionally left blank...
Page 30: ...This page is intentionally left blank...
Page 56: ...This page is intentionally left blank...
Page 78: ...This page is intentionally left blank...
Page 82: ...This page is intentionally left blank...
Page 86: ...This page is intentionally left blank...
Page 94: ...This page is intentionally left blank...
Page 98: ...This page is intentionally left blank...
Page 102: ...This page is intentionally left blank...
Page 106: ...This page is intentionally left blank...
Page 124: ...This page is intentionally left blank...
Page 140: ...This page is intentionally left blank...
Page 142: ...This page is intentionally left blank...
Page 144: ...This page is intentionally left blank...
Page 154: ...This page is intentionally left blank...
Page 158: ...This page is intentionally left blank...
Page 176: ...This page is intentionally left blank...
Page 180: ...This page is intentionally left blank...
Page 182: ...This page is intentionally left blank...
Page 194: ...This page is intentionally left blank...
Page 204: ...This page is intentionally left blank...
Page 214: ...This page is intentionally left blank...
Page 220: ...This page is intentionally left blank...
Page 224: ...This page is intentionally left blank...
Page 228: ...This page is intentionally left blank...
Page 240: ...This page is intentionally left blank...
Page 244: ...This page is intentionally left blank...
Page 252: ...This page is intentionally left blank...
Page 270: ...This page is intentionally left blank...
Page 276: ...This page is intentionally left blank...
Page 284: ...This page is intentionally left blank...
Page 302: ...This page is intentionally left blank...
Page 310: ...This page is intentionally left blank...
Page 312: ...This page is intentionally left blank...
Page 320: ...This page is intentionally left blank...
Page 326: ...This page is intentionally left blank...
Page 330: ...This page is intentionally left blank...
Page 342: ...This page is intentionally left blank...
Page 344: ...This page is intentionally left blank...
Page 348: ...This page is intentionally left blank...
Page 350: ...This page is intentionally left blank...
Page 360: ...This page is intentionally left blank...
Page 364: ...This page is intentionally left blank...
Page 370: ...This page is intentionally left blank...
Page 378: ...This page is intentionally left blank...
Page 382: ...This page is intentionally left blank...
Page 386: ...This page is intentionally left blank...
Page 390: ...This page is intentionally left blank...
Page 398: ...This page is intentionally left blank...
Page 410: ...This page is intentionally left blank...
Page 412: ...This page is intentionally left blank...
Page 418: ...This page is intentionally left blank...
Page 426: ...This page is intentionally left blank...
Page 436: ...This page is intentionally left blank...
Page 442: ...This page is intentionally left blank...
Page 444: ...This page is intentionally left blank...
Page 468: ...This page is intentionally left blank...
Page 472: ...This page is intentionally left blank...