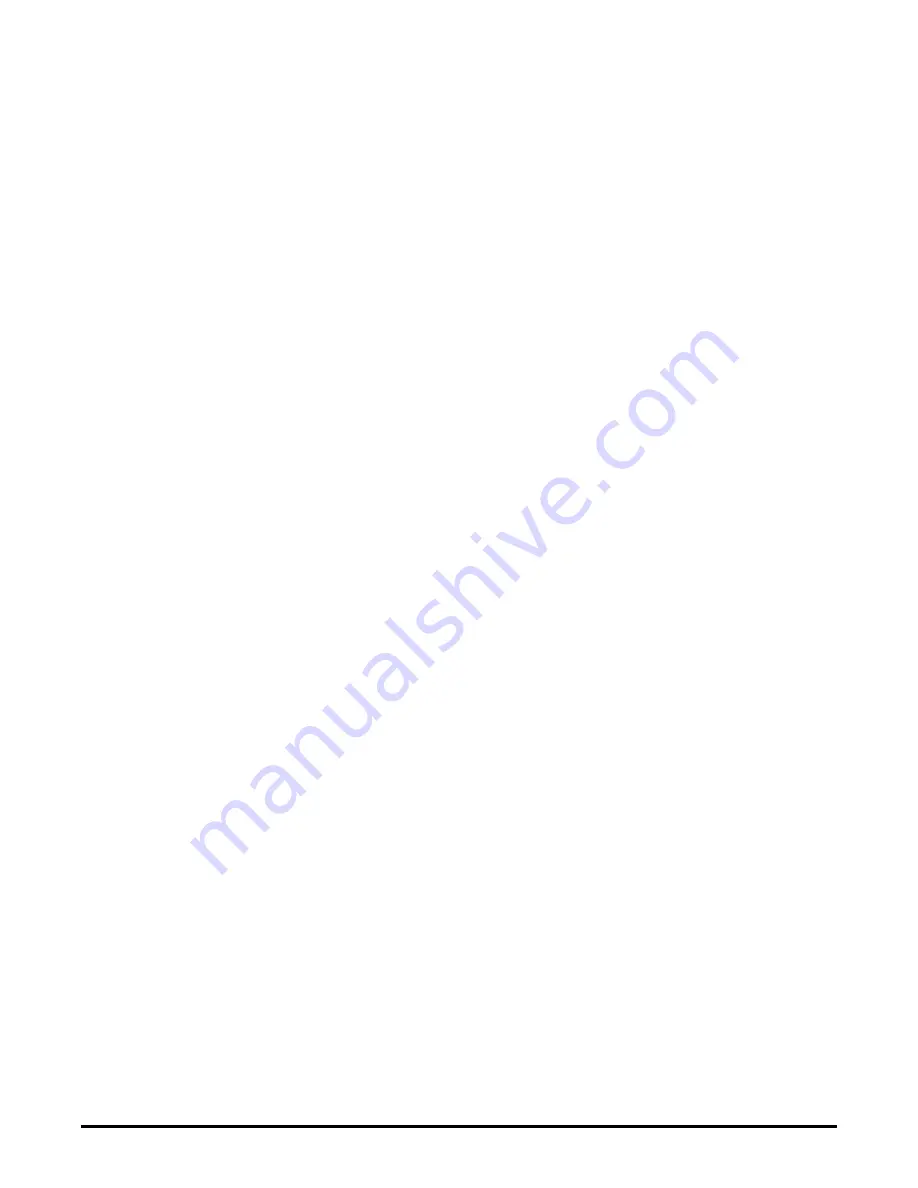
msa3dl7sm-REV0317
Models MSA3 Page 3
an alternating cross pattern.
PILOT VALVE
The pilot valve assembly is accessed by removing the main air distribution valve
body from the pump and lifting the pilot valve body out of the intermediate housing.
Most problems with the pilot valve can be corrected by replacing the o-rings.
Always grease the spool prior to inserting it into the sleeve. If the sleeve is removed
from the body, reinsertion must be at the chamfered side. Grease the o-rings to
slide the sleeve into the valve body. Securely insert the retaining ring around the
sleeve. When reinserting the pilot valve, push both plungers (located inside the
intermediate bracket) out of the path of the pilot valve spool ends to avoid damage.
PILOT VALVE ACTUATOR
Bushings for the pilot valve actuators are threaded into the intermediate bracket
from the outside. The plunger may be removed for inspection or replacement. First
remove the air distribution valve body and the pilot valve body from the pump. The
plungers can be located by looking into the intermediate. It may be necessary to
use a fine piece of wire to pull them out. The bushing can be turned out through
the inner chamber by removing the outer chamber assembly. Replace the bushings
if pins have bent.
AIR EXHAUST
If a diaphragm fails, the pumped liquid or fumes can enter the air end of the
pump, and be exhausted into the atmosphere. When pumping hazardous or toxic
materials, pipe the exhaust to an appropriate area for safe disposition.
This pump can be submerged if materials of construction are compatible with
the liquid. The air exhaust must be piped above the liquid level. Piping used for
the air exhaust must not be smaller than 1" (2.54 cm). Reducing the pipe size will
restrict air flow and reduce pump performance. When the product source is at
a higher level than the pump (flooded suction), pipe the exhaust higher than the
product source to prevent siphoning spills.
Freezing or icing-up of the air exhaust can occur under certain temperature and
humidity conditions. Use of a Warren Rupp Extractor/Dryer unit should eliminate
most icing problems.
BETWEEN USES
When used for materials that tend to settle out or transform to solid form, the
pump should be completely flushed after each use, to prevent damage. Product
remaining in the pump between uses could dry out or settle out. This could cause
problems with valves and diaphragms at re-start. In freezing temperatures, the
pump must be drained between uses in all cases.
CHECK VALVE SERVICING
For flap valve inspection or replacement, remove the flange bolts securing the
suction and discharge elbows and loosen Dresser-type couplings. The flap valves
are exposed for inspection or servicing upon removal of elbows.
DIAPHRAGM SERVICING
Diaphragms are serviced by removing the outer diaphragm chambers which are
secured with 12 bolts. After removing the outer chamber, unbolt the diaphragm
plate by removing 6 socket head capscrews (Allen wrench required). To remove
the diaphragm rod, remove the inner diaphragm plate secured by a nut on the end
of the diaphragm rod. The opposite diaphragm and rod can then be removed as
a unit. The interior components consisting of sleeve bearings, rod seals, and pilot
valve actuator bushings are now accessible for service if required.
REASSEMBLY
All procedures for reassembling the pump are the reverse of the above with
these further instructions:
1. Install the diaphragms with their natural bulge outward. Make certain that the
rubber diaphragm rod bumper is installed on the rod behind each inner diaphragm
plate. Re-torque the 6 socket head capscrews that secure the diaphragm between
the plates to 30 foot Ibs. (40.67 Newton meters) torque reading.
2. Caution should be used while reassembling the check valves. The valves
are designed for some preload over the retainer and the hinge pad. This is done
to insure proper face contact with the seat. After all parts are in place, tighten the