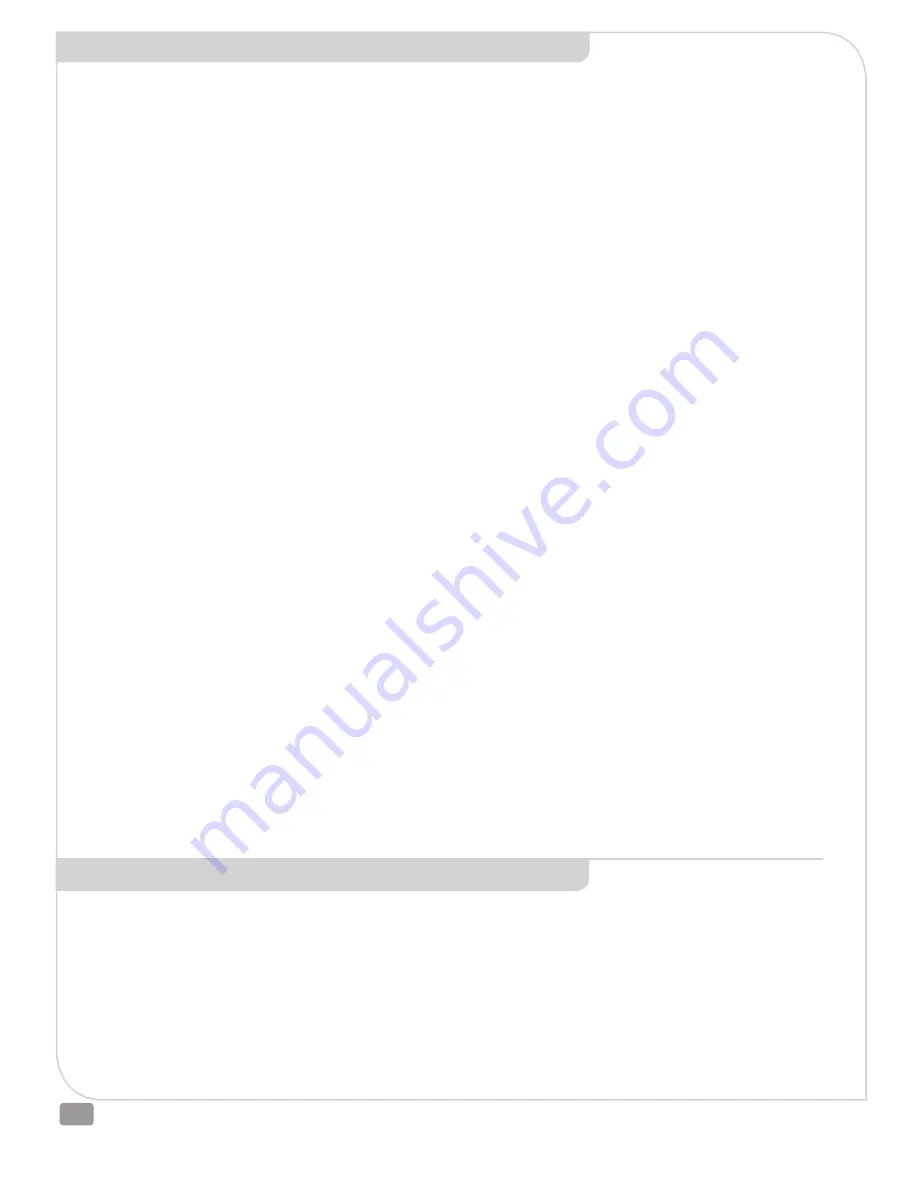
6
2600 Emrick Blvd • Bethlehem, PA 18020 • USA •800-922-0085 • www.warrencontrols.com
FLOAT BALL LEVEL ADJUSTMENT PROCEDURE
1) Remove line pressure and isolate overflow trap. (It is recommended that you have an Inspection Kit on hand
before beginning the procedure.)
2) Remove nuts and bolts from end cover.
3) Remove end cover from float chamber.
4) Remove end cover gasket.
5) Remove capscrews holding valve body to float chamber.
6) Remove internal valve assembly with float ball from float chamber.
7) Install internal valve assembly with float ball in float chamber with float ball extending out of the open end of the
float chamber. Use clamps to secure internal valve assembly with float ball to float chamber.
8) Remove cotter pin and clevis pin from lever bracket. Separate float lever from lever bracket.
9) Loosen jamnut on lever bracket.
10) Adjust engagement of lever bracket with lever bracket base so float ball level is within range of values shown in
Float Ball Level Table with piston disc seated in valve body and pilot assembly seated on piston disc, when clevis
pin, cotter pin, and float lever are reinstalled in lever bracket.
11) Tighten jamnut to secure lever bracket to lever bracket base. Float lever must not bind in lever bracket.
12) Remove clamps and remove internal valve assembly with float ball from float chamber.
13) Remove valve body gasket.
14) Clean gasket surfaces of end cover, valve body, and float chamber.
15) Install new valve body gasket in float chamber.
16) Install internal valve assembly with float ball in float chamber. Watch orientation.
17) Install capscrews in valve body and tighten to secure valve body to float chamber.
18) Install new end cover gasket on float chamber.
19) Install end cover on float chamber.
20) Install nuts and bolts in end cover and tighten to secure end cover to float chamber.
OVERHAUL
Rebuilding of the overflow trap should not be necessary under normal operating conditions. Should the overflow
trap become worn or damaged, parts kits are available. See Parts/ Overhaul.