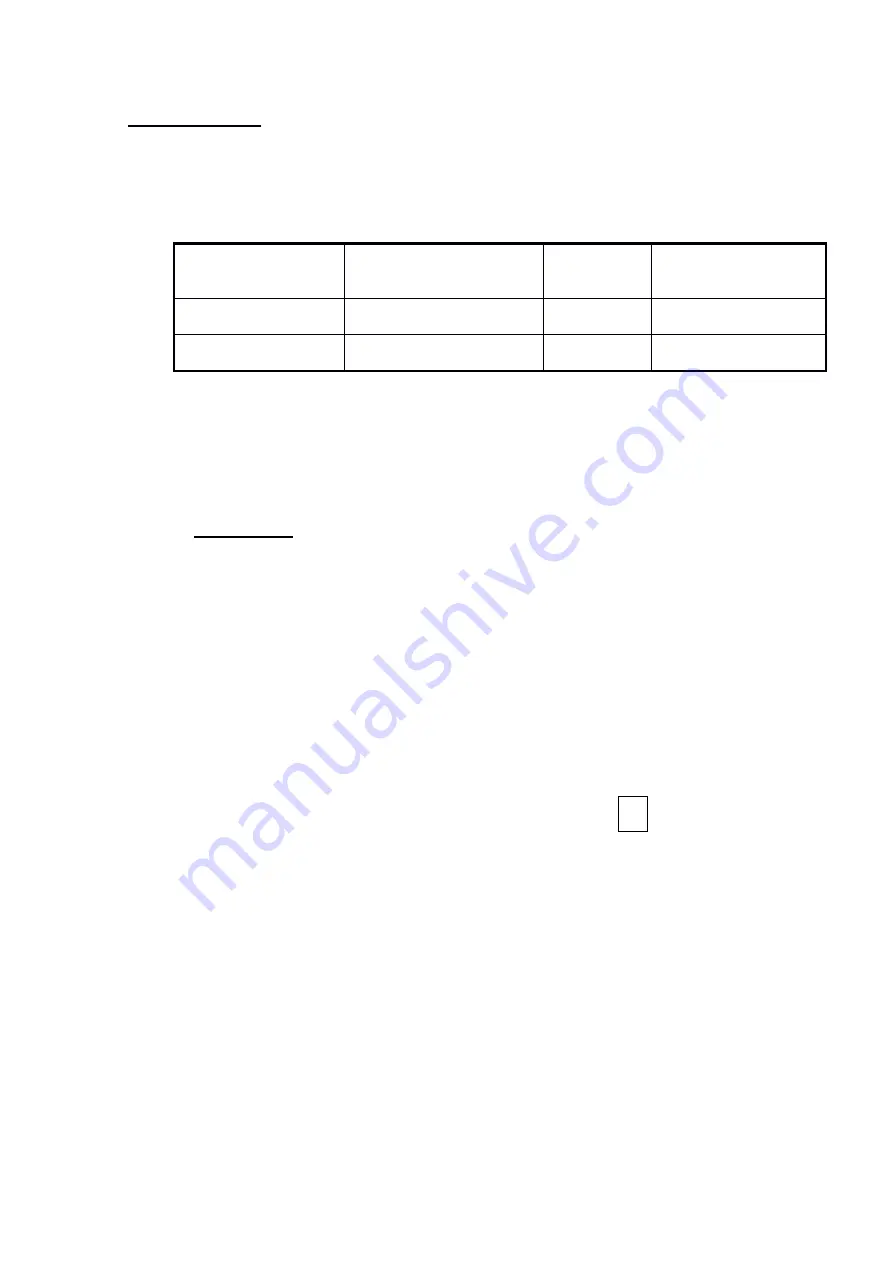
INTIG 250 PULSE DC Pulse Argon Welding Machine
Item
Model
Sectional area of
power cable (mm2)
Air switch
(A)
Sectional area of
ground cable
(mm2)
INTIG 402 PULSE
≥2.5
40
≥25
6.Installation :
a.
The power supply of this machine is 3~ 415
V 50/60HZ, user should prepare the switchboard
and install the air switch (breaker) and ground cable. Connect the green-yellow wire of the
three-phase input cable to the grounding wire on the switchboard reliably according to the
below table:
b. - Connect the argon gas to the air inlet through reducing valve (Use
Ф6 air hose);
c. - When work as Tig, connect
“+” terminal to work-piece firmly; when work as MMA, connect
the “+” terminal according to different electrode;
d.
- Welding torch connection: Air cooling torch: connect the torch gas hose withthe
“Gas outlet
“on the welding machine, connect the torch control plug with the “Torch Switch“on the
welding machine, connect the main cable with
“-” terminal on the welding machine;
7. Operation :
e. Turn on the power switch, the welding machine start to check by itself, the digital meters
and indicators on panel lights on together for 1.5 seconds and lights off 0.5 seconds, then
display normally;
f. - Press the torch trigger switch & adjust the argon gas flow according to different welding
technology.
g. - Set the
“pulse on/off” according to different welding technology, press the “Pulse current”
key to do that. If choose
“pulse off”, set the welding current by adjusting the encoder; if
choose
“pulse on”, set the “peak current”, “PWM ratio”, “Pulse frequency” and “base
curre
nt”, press left/right selection key to choose the parameters need to be set;
h. - Set the
“gas pre-flow time”, “arc starting current”, “Up-slope time”, “down- slope
time
”,”crater current” and “gas post-flow time” according to different welding technology;
i. Welding operation:
i. Two steps: take the tungsten electrode close to the work-piece about 1~3mm,
press the welding torch switch without loosen, it start
B
s weld normally after current
up-slope, when finish welding, loosen the welding torch switch, the current down-
slope to crater current. After welding, please do
n’t take away the welding torch at
once, should wait the gas post-flow time finish, to protect the weld crater and
tungsten electrode;
ii. Four steps: take the tungsten electrode close to the work-piece about 1~3mm,
press the welding torch switch without loosen, after arc striking, find the welding
position, then loosen the welding torch switch, the welding current will increase to
the set current, it starts weld normally , when finish welding, press the welding
torch switch again, the current down-slope to crater current, loosen the torch
switch, arc stop and the welding finish. After welding, please do
n’t take away the
welding torch at once, should wait the gas post-flow time finish, to protect the weld
crater and tungsten electrode
j. MMA: connect the work-
piece too “+’”-” according to different welding technology; after
connecting the ground cable and electrode holder, set the welding current/arc force
current/hot starting current according to electrode
diameter; before welding, the welding machine output 18V
~
20V DC voltage, when the
instant moment that electrode touch the work-piece, the welding
machine output welding current and start the normal welding, after arc stop, the open
circuit voltage will remain 1 second.