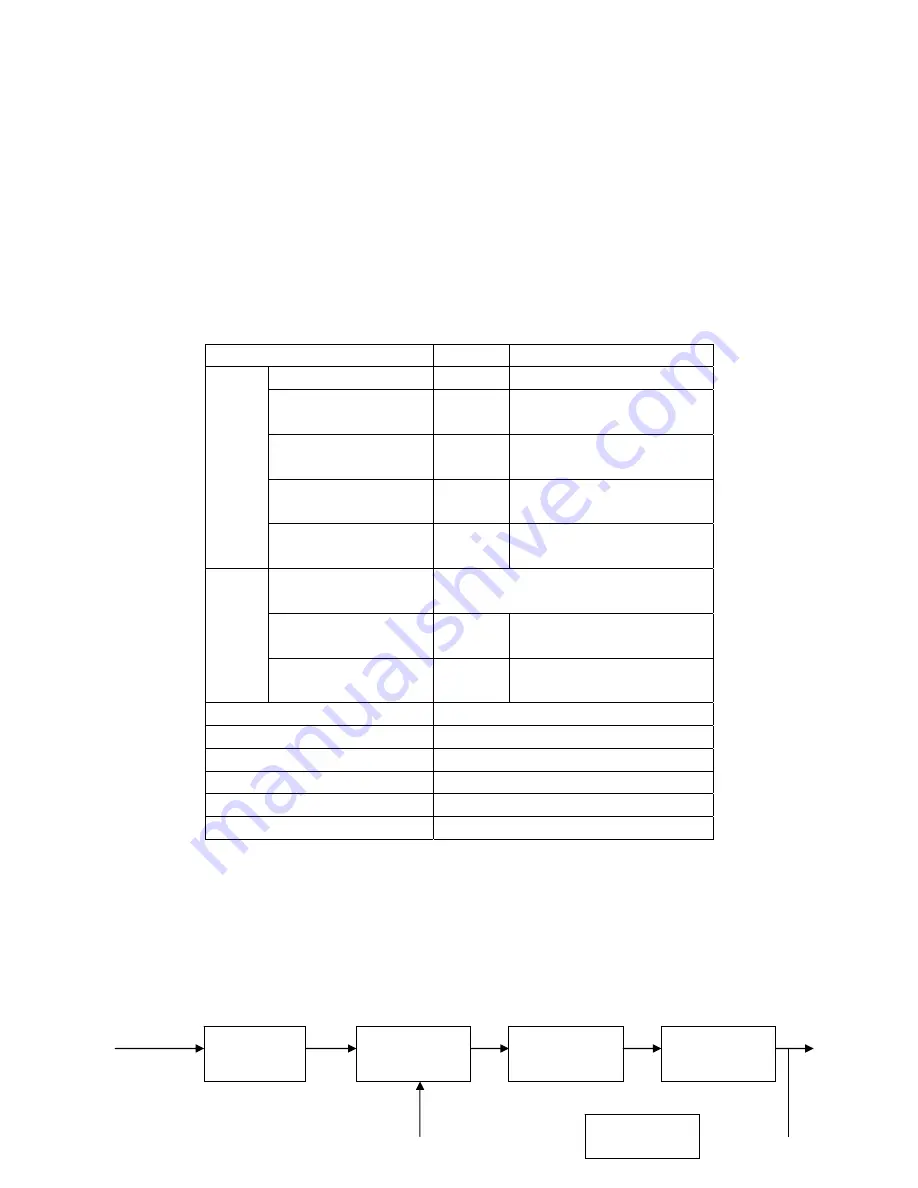
Brief introduction to characteristics:
●
Striking current continuously adjustable
●
Thrust current continuously adjustable
●
Welding current continuously adjustable
●
Digital display current and voltage
●
Overheat indication and overload protection
2. Main Parameters
(Form 1) Performance Parameters
Content of Parameters
Unit
IN ARC 400 IH
Output
On-load voltage
V
70±5%
Rated
Current output
A 400
Rated
Load voltage
V 36
Regulation range
Of welding current
A 20-400
Load
continuous rate
% 60%
Input
Power
parameters
Three-phase 380V 50/60Hz
Rated
capacity input
KVA 18
Rated
current input
A 28
Efficiency
≥
90%
Power factor
≥
0.89
Grade shell protection
IP21S
Insulation grade
F
Overall dimension mm
570×320×530
Weight Kg
34
3. Summary
of
Principle
The invention of inverter arc welding benefits from appearance of the inverter theory
and device. The inverter arc welding power source works rectifying 50/60HZ working
frequency to direct current, inverting to HF by the high power switching device
IGBT( the frequency can reach 20KHZ), then reduce voltage and rectification, output
the dc high-power supply by PWM, the weight and volume of main transformer are
remarkable decreased, and the efficiency is raised over 30%.
380v50Hz
Three-phase
rectifier
High frequency
inverter
High frequency
transformer
Waves filtering
rectifier
Control circuit