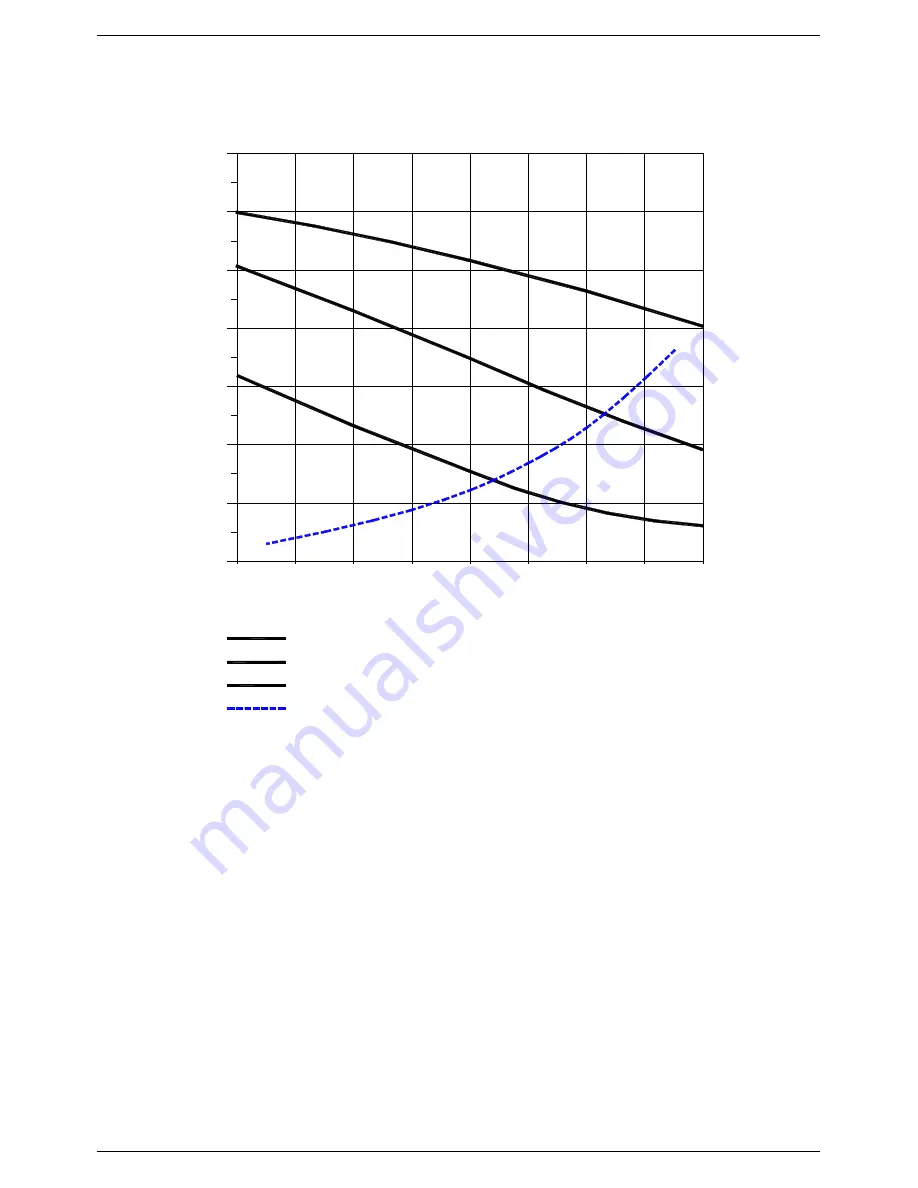
TECHNICAL CHARACTERISTCS
TR05A153.B1107
13
3.5 Circulation pump performance curves
I
II
I
II
III
1400
1200
1600
70
50
60
40
1000
800
400
600
30
10
20
0
0
200
III
Available head at minimum speed
Available head at second speed
Available head at maximum speed
Flow l/h
H
ea
d
(
kP
a)
Appliance Loss
Figure 5: Pump performance curves