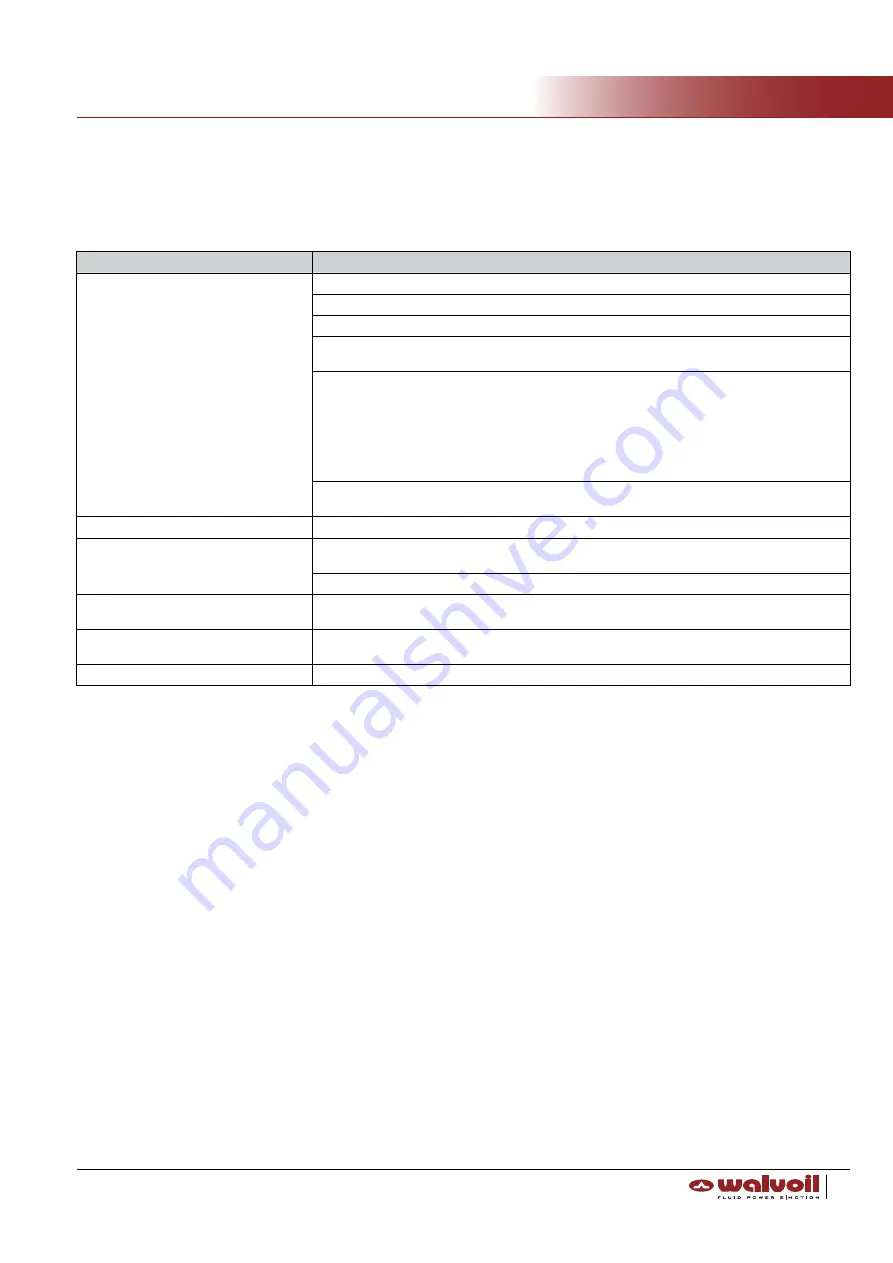
D1WWTD02E
15
Service Manual
DPC130X
Do not carry out maintenance operations on the control valve when an explosive atmosphere is present and the control valve
surface temperature is outside the environmental temperature range as specified before.
It is advisable to periodically check the parts shown in the table below.
___________________________________________________________________________
Standard maintenance rules
______________________________________________________________________________________________________
Disposal
Reference
Item to be checked
General installation
Verify valve is correctly and safely fixed in its seat
Check electric connector and wire condition and wear
Clean the valve carefully, avoiding direct jet, especially on electric parts and connections
In order to prevent rust, dry the valve after cleaning, avoiding scratching and damaging external
surfaces
Periodically check the tightening of:
- Tie rods
- Lever box
- Control kit screws
- Unloading screw
- Electrohydraulic valve screws
- Hydraulic fittings
Constantly check oil contamination status and plant filter condition. Contamination may bring to
several malfunctions
Body
Check presence of excessive rust and corrosion and replace parts or complete valve if needed
Spool
Check presence of scratch, rust and corrosion. It may bring to seals damage or spool sticking. Re-
place parts if needed
Apply grease on spring, lever or positioning kits if the spool operation is not sliding
Sealing
Check and replace any possible hardened, de-formed or damaged O-ring. Check and replace the
O-ring also in case its surface is dirty or shows particles.
LS Valve and Auxiliary Valves
Periodically check pressure setting values, if not correct adjust relief valves and safely lock the nut
at appropriate torque
Electric components
Please refer to attached service manual of these components
When the control valve has to be disposed, first drain the hydraulic fluid completely and dispose of it as industrial waste.