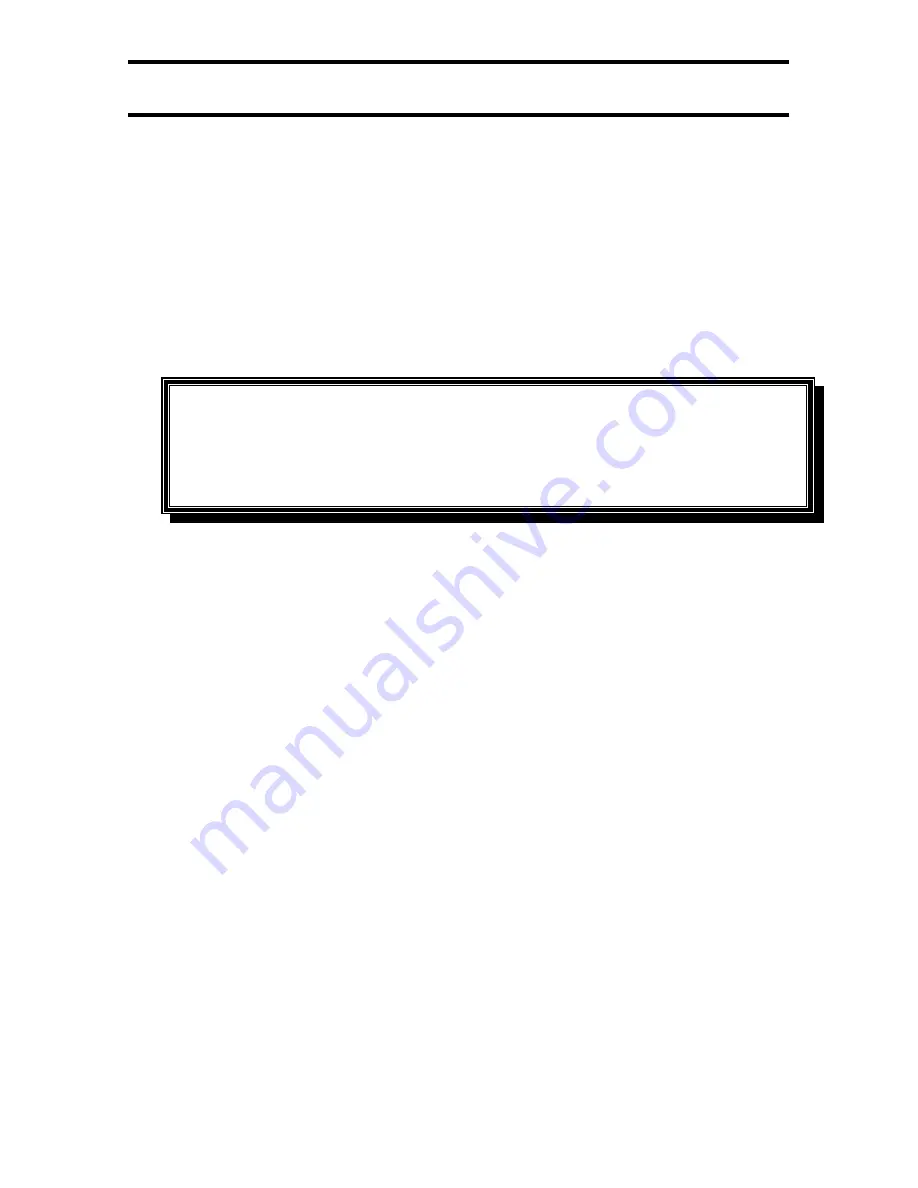
2 INSTALLATION
9070
9
With the transmitter case secured to a wall or panel, open the
chassis to the case and wire the main power connection. Fit the
connection blocks onto the circuit boards.
9
Fit the chassis unit, secure it with the captive screws and replace
any ground (earth) bonding leads.
9
Position the face panel and secure it with the four plastic fasteners.
2.2 SAMPLE
REQUIREMENTS
[
Warning:
Do not exceed the maximum pressures and temperatures
specified. If you use pressure-reducing equipment, install a pressure relief
valve between your equipment and the sample inlet to the monitor for safety
purposes.
Bring the sample to the temperature and pressure suitable for measurement,
using sample coolers and pressure-reducing equipment (see Section 8)
2.3 EXTERNAL
PIPING
CONNECTIONS
2.3.1
INLET
The sample should be connected to the sensor unit using ¼” o.d. tubing of
stainless steel or rigid plastic. Connect this to the sample inlet coupling on the
right hand side of the case’s bottom piece.
The inlet tube should be of sufficient wall thickness to withstand the highest
sample pressure, and pipe lengths should be kept short.
Where particulate matter is present (e.g. magnetite in boiler samples), fit a 60-
micron sample filter to the sample line.
A shut-off valve (not supplied with the monitor) is necessary in the sample
unit.
2.3.2 DRAIN
The drain from the cup at the bottom of the sensor unit case consists of a hose
barb suitable for 3/8” bore plastic or rubber tubing. Alkaline
effluent from the monitor and overflowing sample drains through this single
connection.
6