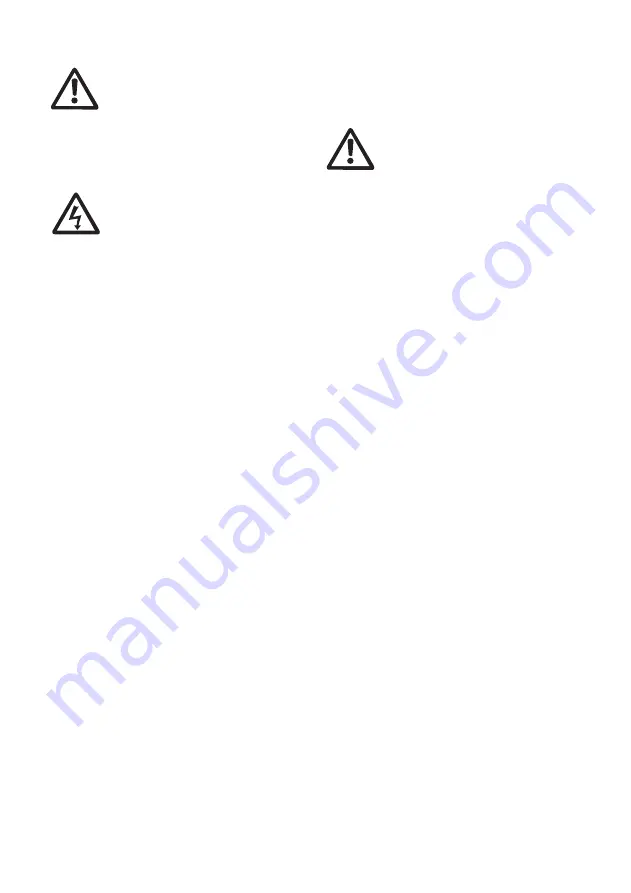
~ 3 ~
6.3. The pump is filled with liquid.
6.4. The suction filter is not blocked by any
foreign objects.
7. Operation and Maintenance
It is dangerous to operate the
pump against a closed discharge
outlet because it will cause
extremely high liquid flow
temperature and damage the
pump in a few minutes.
7.1. Lubrication
The mechanical seal and shaft sleeves
are lubricated by the pumped liquid.
7.2. Suction filter
Always keep suction filter clean and
make sure it is not blocked by impuri-
ties.
7.3. Periodic checks
The following checks should be carried
out periodically to ensure the normal
operation.
7.3.1. Check the quantity of liquid and
operating pressure.
7.3.2. Check there are no leaks on piping
joints.
7.3.3. Check the tripping of the motor
starter.
7.3.4. Check that all controls are
functioned normally.
7.4. The pump must not be used to transfer
explosive liquids. In systems with hot
liquids (over 140oF), extra caution
should be exercised to prevent from
personal injury.
7.5. The pump should not be used to
transfer toxic or contaminated liquids.
Please carefully follow all instructions
in the manual as Walrus may refuse to
accept the contaminated pump for
servicing.
5. Electrical Connection
5.1 The electrical connection
should be carried out in
accordance with local regula-
tions. Never make any
connections unless the
electricity supply has been
switched off.
5.2. The electrical hazard warning
mark is placed outside the
connection box. Be careful.
5.3. Electrical data (voltage and frequency)
are shown on the pump nameplate.
Verify if these data match your electric-
ity supply. A circuit breaker should be
installed and the grounding be
properly connected for your safety.
5.4. Make electrical connection in accor-
dance with connecting diagram located
inside the connection box. The motor
current must be within the rated amps
range indicated on nameplate. Three
phase motor requires a magnetic
starter for safety.
5.5. For three phase motors, please check
the correct direction of rotation of the
pump on the motor fan cover. When
seen from motor fan cover end, the
pump should rotate clockwise. You can
reverse the direction of rotation by
interchanging any two of the incoming
supply wires.
6. Start-up
Before starting the pump, make sure the
following:
6.1. For three phase motors, verify if the
rotating direction is correct. It should
be clockwise viewing from the motor
fan cover end.
6.2. All piping joints are completely tight.
Leakage in piping may cause the pump
hydraulic loss.