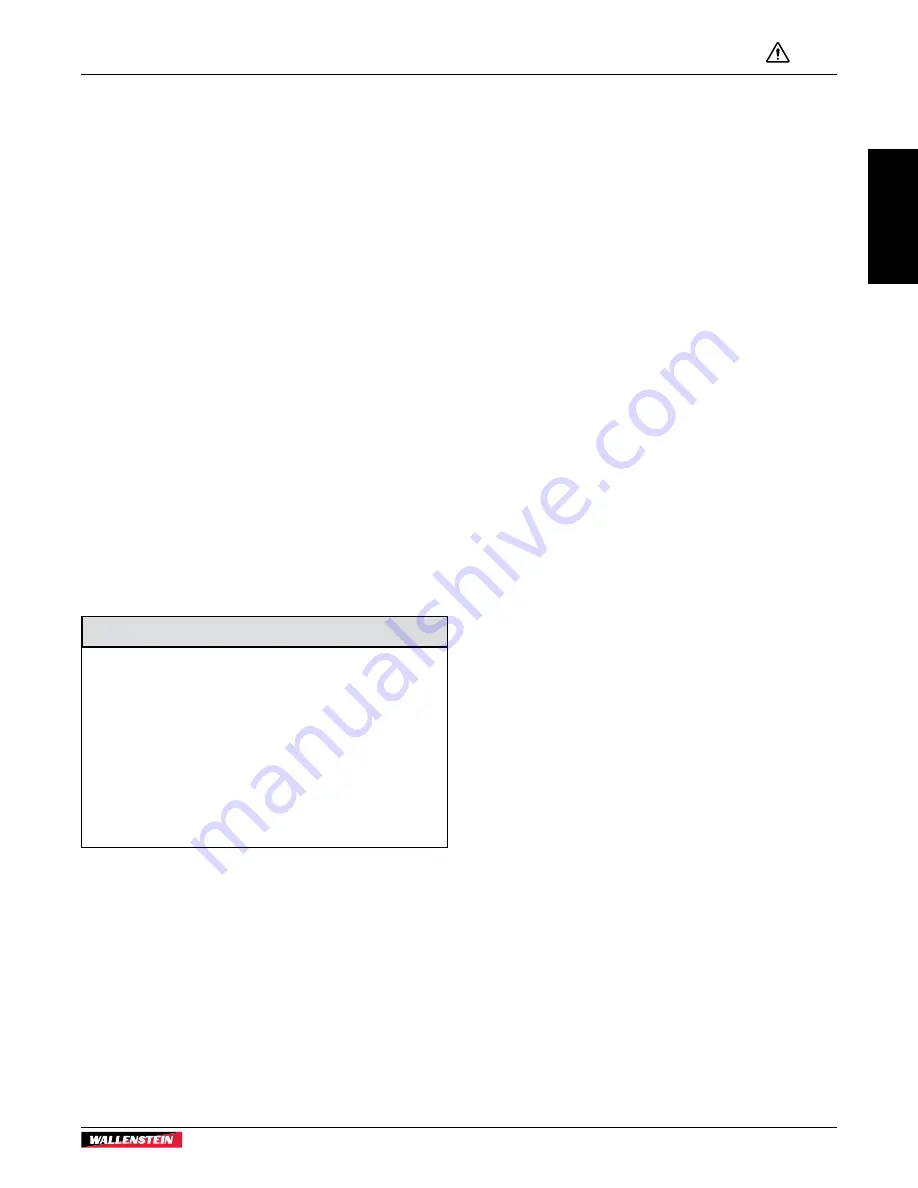
Safety
LXG520R
Grapple
Safety
9
2.4.1 Equipment Safety Guidelines
A few seconds of thought and a careful approach to handling
equipment can prevent accidents.
•
Replace safety or instruction signs (decals) that are not
readable or missing. For locations and explanations, see
.
•
Do not modify the equipment in any way. Unauthorized
modifications may affect the integrity of the machine
or the ability of the machine to perform as designed.
Modifications can impair safety or function. They can affect
the life of the equipment and void the warranty.
•
Make sure the machine is correctly stationed, adjusted, and
in good operating condition.
•
Never exceed the limitations of the machine. If its ability to
do the job, or to do it safely is in question–
STOP!
•
Protective cab shields must be provided on a log loader
unless the absence of shields does not pose a hazard to the
operator.
2.4.2 Safe Condition
References are made to
safe condition
throughout this manual.
Safe condition means putting the machine in a state that makes
it safe to service or maintain.
Before starting any service or maintenance, complete the
following:
SAFE CONDITION
1.
Remove material from the grapple.
2.
Lower the grapple to ground.
3.
Turn off the excavator engine.
4.
Engage the hydraulic control lockout device.
5.
Turn off the main hydraulic switch.
6.
Move the hydraulic controls to make sure that there is no
movement.
2.5 Create a Safe Work Site
For more information, see
2.5.1 Designated Safe Area
A
Safe Area
must be designated for workers who are on foot
and in close proximity to the equipment.
•
The boundaries of a designated Safe Area must be
communicated to all workers within and in close proximity
to the Work Zone.
•
No equipment should enter into or proceed through a Safe
Area unless—
-
The equipment operator first obtains permission in a
clear and unmistakable manner from all of the workers
in that safe work area or from the supervisor of those
workers, and
-
Those workers take a safe position.
2.5.2 Work Zone Arrangement
•
A
Work Zone
includes any area where work with this
grapple is done, but does not include the traveled portion
of a road unless that portion of the road is being used as a
landing.
•
Work being done in a Work Zone in a forestry operation
must be planned and the work area must be located,
constructed, maintained, and operated to ensure that:
-
Logs can be moved safely in the area.
-
Log piles and equipment used to handle the logs do not
become unstable or otherwise create a hazard.
-
Workers are able to work in locations clear of moving
logs and equipment.
-
Workers are not exposed to incoming or runaway logs
or other debris.
-
The area is kept free from buildup of bark and other
debris to the extent that it would pose a risk to workers.
-
An effective method of dust control is used and
maintained.
•
Log piles must, to the extent practicable, be located on
stable and relatively level ground.
•
Log piles must not be higher than the safe operating reach
of the excavator being used to handle the logs.