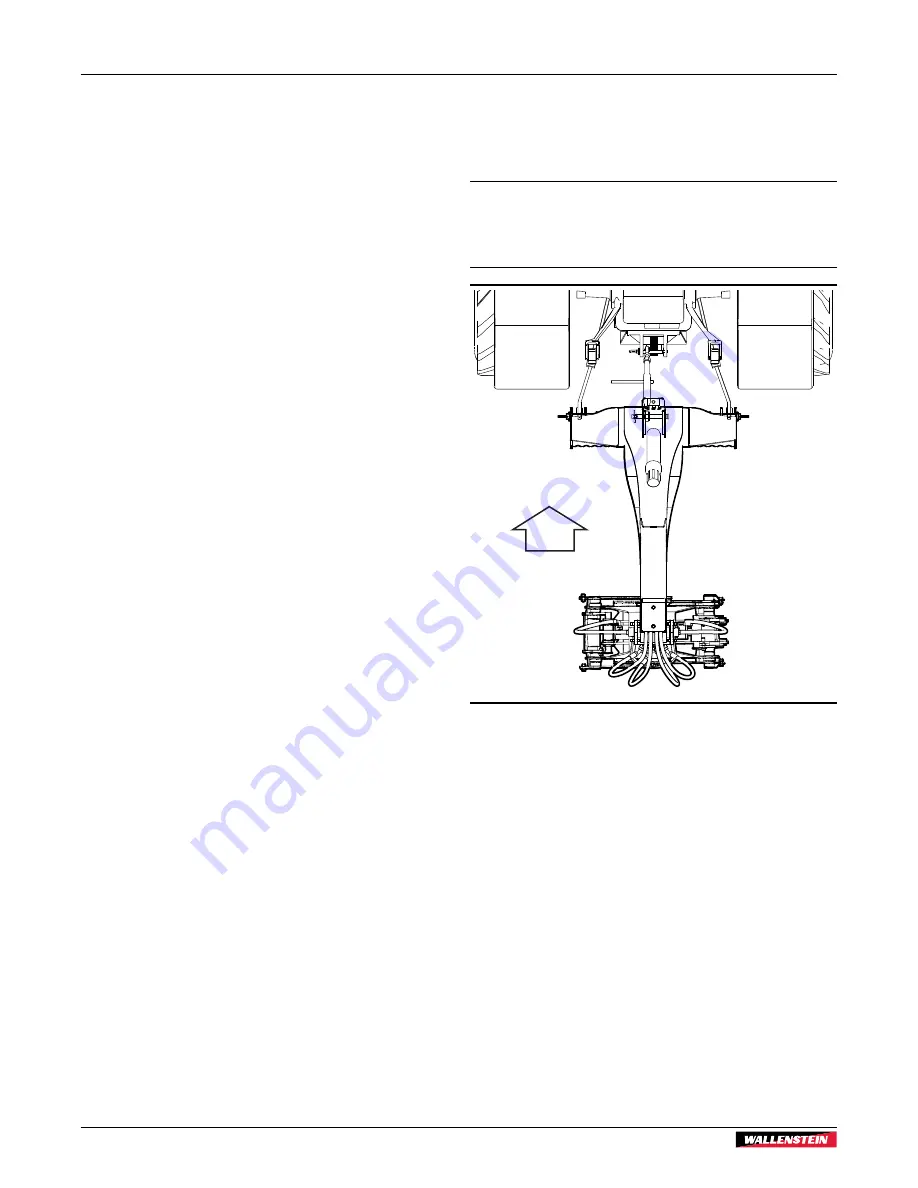
Familiarization
LXG300 Series
Grapples
18
4. Familiarization
4.1 To the New Operator
It is the responsibility of the owner or operator to read this
manual and to train all other operators before they start
working with the machine.
By following recommended procedures, a safe working
environment is provided in the area around the work site.
Untrained operators are not qualified to use the machine.
4.1.1 Training
Each operator must be trained in the proper operating
procedures prior to using the machine.
1.
Review control location, function and movement directions.
2.
Move the unit to a large open area to allow the operator
to become familiar with control function and machine
response.
3.
When a new operator is familiar and comfortable with the
machine, they can proceed with the work.
4.1.2 Job Site Familiarization
Become familiar with the work site prior to beginning. Avoid the
possibility of problems or accidents by reviewing the following.
•
Determine a safe work area / trailer-load location:
-
Area must be clear of stones, branches or hidden
obstacles that might cause a tripping, hooking or
snagging hazard.
-
Ground should be firm and level.
•
Determine a safe log stack location:
-
Stack should be on level ground.
-
Make sure stack location does not interfere with safe
operation of the machine.
•
Precut and de-limb logs.
4.2 Operator Orientation
IMPORTANT! The directions for left-hand, right-hand,
backward and forward mentioned throughout this manual
are determined when sitting in the tractor seat, facing the
direction of forward travel.
01413
FWD
Fig. 9 –
Direction of forward travel