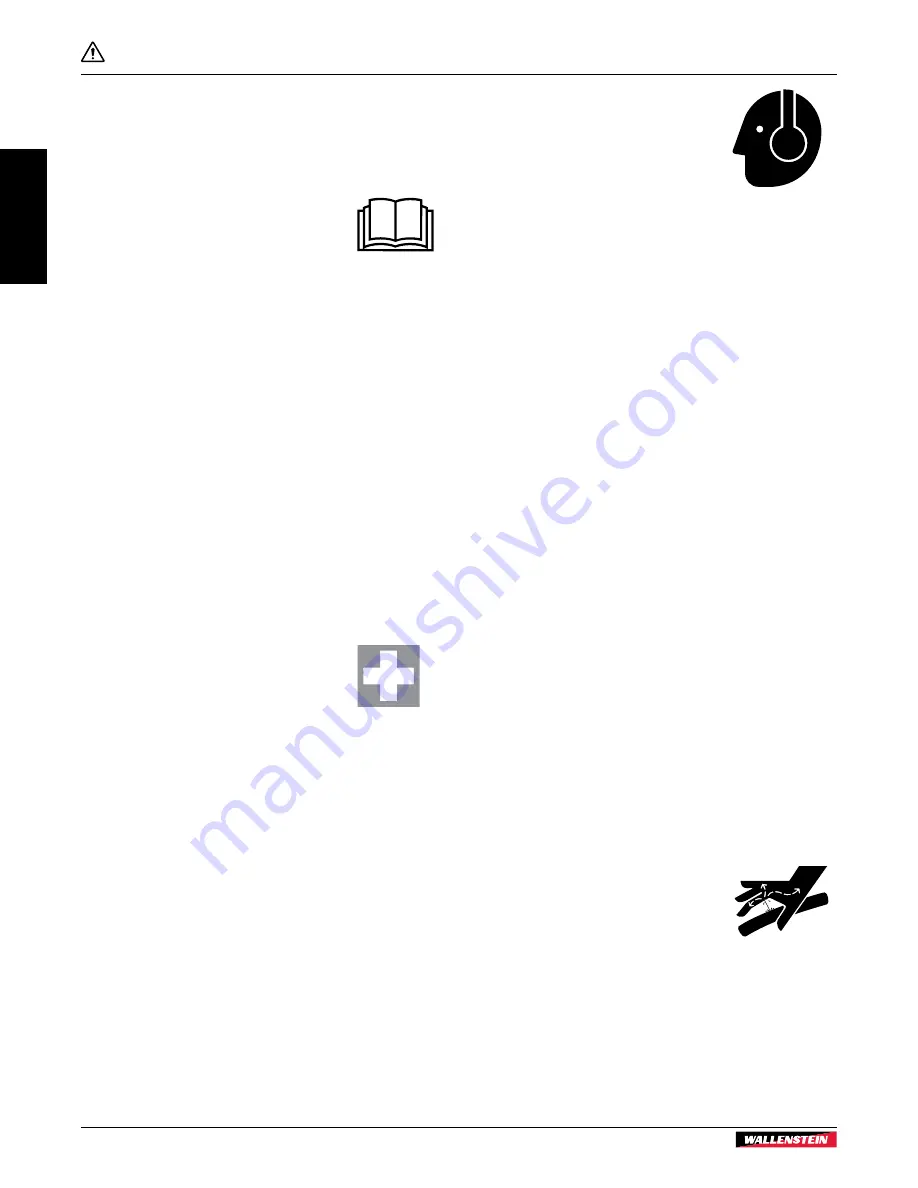
2.4 Safety Rules
Safety is a primary concern in the design and manufacture of
Wallenstein products. Unfortunately, efforts to provide safe
equipment can be wiped out by a single careless act.
•
It is the operator's responsibility to read,
understand and follow ALL safety and
operation instructions in this manual.
•
The operator of this grapple must be a responsible, properly
trained and physically able person familiar with machinery
and trained in the operation of a mini skid steer. Learn
the controls and how to stop the machine quickly in an
emergency before working with the grapple.
•
An employer has the responsibility to train employees how
to operate the equipment they are using. When someone
does not understand the basic operation of a piece of
equipment, they can create dangerous situations very
quickly. Operators must completely understand:
-
Safety section of this manual
-
Safety decals on the machine
-
Mini skid steer operator's manual
•
If this machine is used by any other person, loaned or
rented, it is the owner's responsibility to make certain that
prior to using, every operator is fully trained.
•
Review safety related items annually with all personnel who
will be operating or performing maintenance.
•
Keep a first-aid kit available for use
should the need arise and know how
to use it.
•
Never consume alcohol or drugs when operating this
equipment. Alertness or coordination can be affected.
Consult your doctor about operating this machine while
taking prescription medications.
•
Never swing a load if the operator's line of sight is
obstructed. Do not lift it higher than is necessary to provide
unobstructed vision for the equipment operator.
•
Always wear PPE when operating or servicing the
machine. Hard hats, protective glasses, protective shoes,
gloves, reflector type vests and ear protection are types of
equipment that may be required.
•
Avoid loose fitting clothing, loose or uncovered long hair,
jewelry, and loose personal articles. These can get caught
in moving parts. Jewelry may also ground a live circuit.
•
Prolonged exposure to loud noise may
cause permanent hearing loss! Power
equipment with or without equipment
attached can often be noisy enough to
cause permanent, partial hearing loss.
•
Wear hearing protection on a full-time basis if the noise in
the operator's cab exceeds 80 dB. Noise over 85 dB on a
long-term basis can cause severe hearing loss. Noise over
90 dB adjacent to the operator over a long-term basis may
cause permanent, total hearing loss.
•
Keep bystanders away at a safe distance at least 10 ft
(3 m) from stacking zone. Mark the zone with safety cones.
•
Use the machine only in daylight or good artificial light.
•
Perform the
Pre-operation Checks
before starting work
(see
•
Do not risk injury or death by ignoring good safety
practices.
Equipment Safety Guidelines
•
Replace any safety sign or instruction sign that is not
readable or is missing. Location and explanation of safety
signs start on
.
•
Do not modify the equipment in any way. Unauthorized
modification may result in serious injury or death and may
impair the function and life of the equipment. Unapproved
modifications void warranty.
•
Never exceed the limits of machine if its ability to do a job,
or to do so safely is in question.
•
Protective cab guards must be provided on a log loader
unless the absence of guards does not pose a hazard to the
operator.
•
Shut down the machine and place it in a Safe Condition
before performing any service, maintenance work or
storage preparation.
•
Make sure that all the components in the hydraulic system
are kept in good condition and are clean.
•
Before applying pressure to the system,
make sure all connections are tight.
Check lines, hoses, and couplings for
damage.
•
Do not attempt any makeshift repairs to the hydraulic lines,
fittings or hoses by using tape, clamps or cements. The
hydraulic system operates under extremely high pressure.
Such repairs can fail suddenly and create a hazardous and
unsafe condition.
Safety
LXG210 Series
Log Grapples
Safety
8
Summary of Contents for LXG210 Series
Page 36: ...www wallensteinequipment com ...