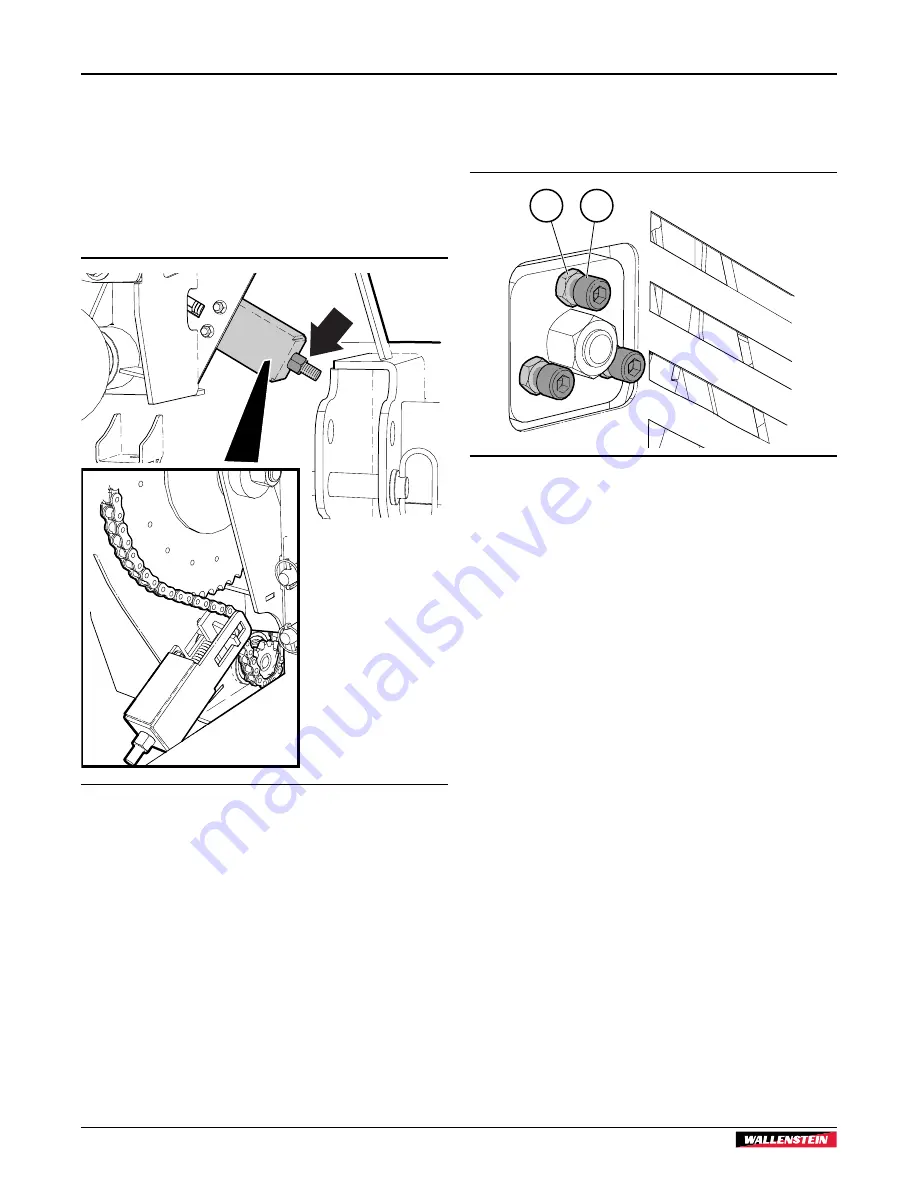
Service and Maintenance
FX85, FX110, FX140
PTO Skidding Winch
40
7.5 Drive Chain Tension
The winch is designed with a roller chain to transmit the power
between the PTO input and the clutch / winch. The chain tension
is automatically set through a spring-loaded sliding tensioner.
The chain tensioning system is designed with an internal
compression spring to set maximum chain tension during
operation. No adjustment is required.
00603
Fig. 50 –
Chain Tensioner
7.5.1 Drive Chain Replacement
If replacing the roller chain, follow this procedure to release
tension on the chain:
1.
Turn in (tighten) the adjusting nut on tension bolt until chain
tension is released (minimum chain tension).
2.
Remove the old chain and install the new chain.
3.
To set the chain to maximum tension, turn out the adjusting
nut on tension bolt within 1/4" (6 mm) from end of tension
bolt.
7.6 Clutch Adjustment
Adjust the clutch using the following method if it begins to slip
or goes out of adjustment.
00604
1
2
Fig. 51 –
Clutch Adjustment
1. Jam Nut
2. Socket Head Capscrew
Procedure
1.
Loosen the three jam nuts on the front side of the winch.
2.
Turn socket head capscrews inward by hand until they just
contact the pressure plates.
3.
Tighten bolts equally until the desired amount of free play
is felt on clutch lever. Pull on rope to feel free play in clutch
and adjust as required.
4.
Tighten jam nuts.
5.
Check clutch setting before resuming work. Start PTO and
check for drag on the clutch.
Drag can cause the winch rope to inch in without the rope being
pulled. If the rope is inching in with the clutch disengaged, go
through the above steps again to readjust.
Summary of Contents for FX Series
Page 1: ...OPERATOR S MANUAL PTO driven Log Skidding Winch FX Series Part Number Z97090_En Rev May 2021 ...
Page 54: ......
Page 55: ......
Page 56: ...www wallensteinequipment com ...