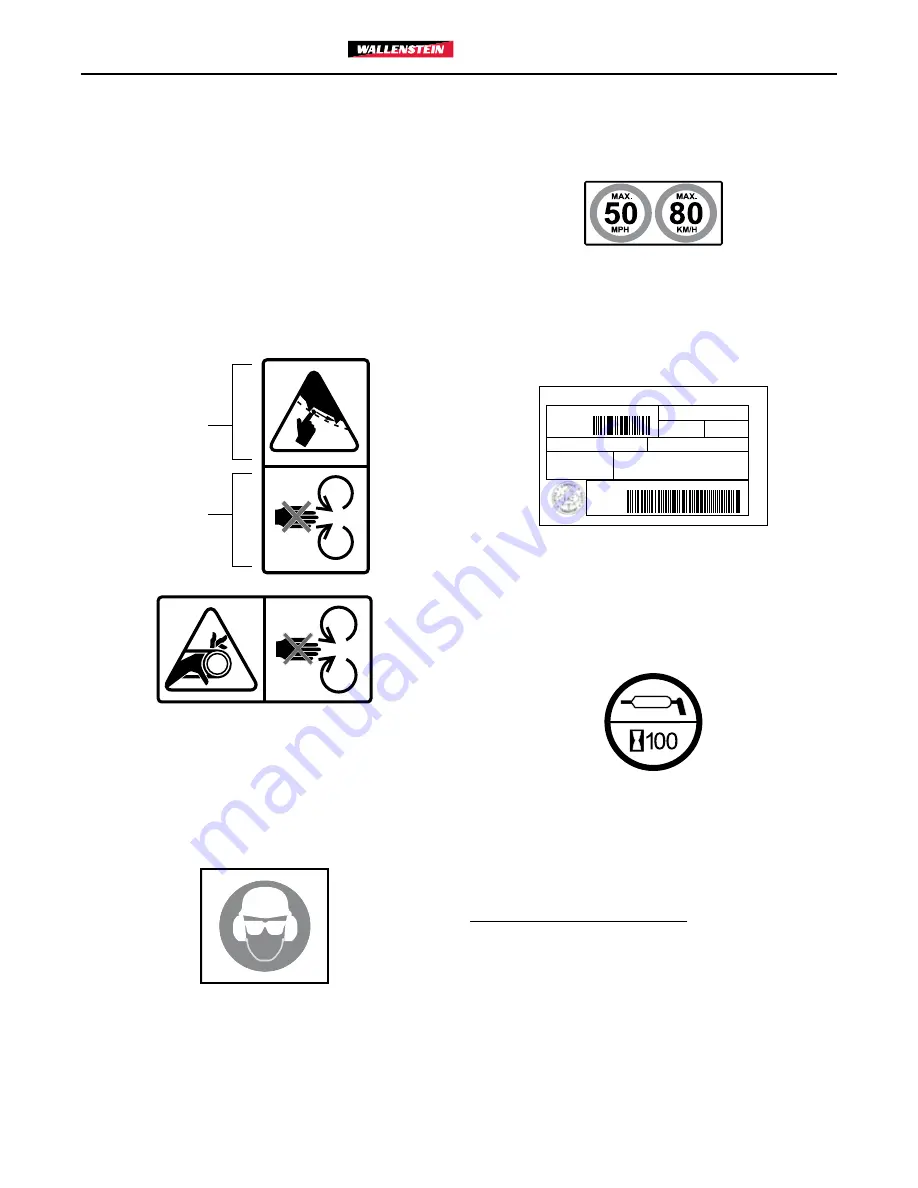
6
BXT Series
1.4 Types of Decals on the Machine
When getting familiar with the Wallenstein product, notice that
there are numerous decals located on the machine. There are
different types of decals for safety, information, and product
identification. The following section explains what they are for
and how to read them.
Safety Decals
have a yellow background and are generally two
panel. They can be either vertical or horizontal.
The top (or left-hand) panel shows the safety alert (the potential
hazard), and the bottom (or right-hand) panel shows the
message (how to avoid the hazard).
Hazard
How to avoid the
hazard
Safety Notice Decals
are blue with a white background and
generally rectangular with single or multiple symbols. This decal
informs what Personal Protective Equipment is required for safe
operation.
Informative Decals
are generally pictorial with a white
background and can vary in the number of panels. This type of
decal provides additional information to the operator or explains
the operation of a control.
Product Decals
indicate machine model and serial number, and
other important information.
VIN/
NLV:
MODEL: ##########
#########
Manufactured by:
Wallenstein Equipment Inc., 7201 Line 86, Wallenstein ON N0B2S0, Canada
TYPE OF VEHICLE/TYPE DE VEHICLE:
TRA / REM
GAWR/PNBE (KG):
GVWR/PNBV (KG):
###
DIMENSION- RIM/JANTE
/
E
R
I
T
:
PNEU:
COLD INFL. PRESS/PRESS DE
CONFLA A FROID (PSI/LPC):
THIS VEHICLE CONFORMS TO ALL APPLICABLE STANDARDS
PRESCRIBED UNDER THE CANADIAN MOTOR SAFTEY REGULATIONS
IN EFFECT ON THE DATE OF MANUFACTURE / CE VEHICLE EST
CONFORME A TOUTES LES NORMES QUI LUI SONT APPLICABLES EN
VERTU DU REGLEMENT SUR LA SECURITE DES VEHICLES
AUTOMOBILES DU CANADA EN VIGUEUR A LA DATE DE SA FABRICATION.
###
###
###
###
Maintenance Decals
have a green background and can vary
to the number of panels. This decal shows a type maintenance
required and frequency interval.
See the section on safety signs for safety decal definitions.
For a complete illustration of decals and decal locations,
download the parts manual for your model product at
www.wallensteinequipment.com.